According to the Bureau of Labor Statistics, unemployment in the US was at a historic low of roughly 3.6 percent in June 2023. This figure represents a 50-year low, and although that’s good news for the country, it may pose a big problem for individual companies looking to fill open positions or expand their businesses. Whereas once employers ran job ads and applicants showed up, today, the choices available to HR departments may not be as robust. Qualified, skilled candidates may not be as easy to find as they once were.
Innovative Thinking
Today, companies need to think creatively to successfully address shortages of trained personnel. Finding good employees has never been easy, but in the current landscape, it is especially challenging to find the right fit. Here are five tips for finding your business the help it needs in today’s world.
Automate Existing Operations
Today could be the perfect time to complete an audit of your factory’s automation status. This is especially true in the food industry, where new automation in tasks such as deboning, packaging, and forming are becoming commonplace. Automatic data collection and digital technology have also taken giant steps forward. Today, electronic sensors can collect data directly from equipment and communicate wirelessly with computers to drive Smart Factory analytics. Improved productivity and automation can free up employees, who can be re-trained for open positions elsewhere in the business.
Cross-Train Employees Within Your Company
Although cross-training won’t directly increase headcount, having a pool of qualified employees available in-house can be important. Changing customer demands can cause temporary fluctuations in production requirements within your plant. With careful cross-training, newly qualified employees can be shifted from line to line or department to department to meet output fluctuations.
Hire Temporary Contractors and Freelancers
As of 2018, 35 percent of the American workforce was made up of freelancers and independent contractors, and the number is expected to climb to 50 percent in the next decade. The popularity of freelance positions in business is growing as more and more individuals of technical and professional skill sets look to take on independent status in the workplace. Though many specialized skills may not be available in the local labor markets, training and moving low-level employees to higher-skilled positions can provide flexibility. When a low-level position opens up, the job can be filled with a contractor. Using a combination of in-house training, internal personnel shuffling, rescheduling, and hiring freelancers can make good business sense.
Recruit Seniors, Veterans, or Disabled
Many highly professional individuals retire in their 60s yet seek to stay busy. These individuals can be a tremendous reservoir of talent for companies seeking employees. Stories abound about companies using retired individuals to supplement existing staff. Nevertheless, seniors may not want to work full-time or may look for flexible schedules. For companies willing to work with variable but predictable schedules, retired personnel may be a great option. A salesperson with 40 years of food marketing experience could bring value to a food producer, even if they only work half-time.
Many veterans leave the service with valuable skills. In addition, veterans’ work ethic, leadership skills, and dedication to accomplishment make them terrific candidates for skilled positions. Jobs such as maintenance, supervision, or office work can be areas of interest to veterans.
Hiring those with disabilities is also an option for some positions. Working with local rehabilitation centers or state agencies can provide a company with a source of ready-trained individuals with sufficient skills to fill some positions. If an internal worker can be trained, moved to a position requiring a higher skill level, and replaced with a skilled disabled person, everyone benefits.
Work with Local Colleges, High Schools, and Trade Schools
One way to develop both current and future employees is to establish working relationships with local schools or training centers. Programs can be designed to institute internships for young people interested in careers in your industry. An alternative is to identify jobs for which part-time positions can be established and filled by students. Furthermore, over time, many of these temporary employees can become very experienced and qualified long-term employees.
Finding Qualified Manpower in Manufacturing
It appears that today’s tight labor market is part of a long-term trend that may be a fact of business life for some time to come. To address this problem head-on, companies must think of creative ways to find, train, and keep skilled employees. Those looking to expand their workforce should first look internally. By improving production line efficiencies, companies can free qualified employees who can then be reassigned. This reduces the need for hiring new employees.
Companies can use KPIs to identify areas of opportunity, reassign personnel, and reduce the need for additional hiring. Worximity, a provider of Smart Factory analytics, can help. We offer a complete suite of real-time data capture and analysis tools. Data is collected via sensors located on production lines, then wirelessly communicated to computers. Data is analyzed, and the measures are displayed on Worximity’s in-factory dashboard named Tile+. The Worximity system, which can be implemented in as little as one day, is reasonably priced and currently available for demo at our website.
Customer demand could be increasing in conjunction with low unemployment, which only adds to the requirements for qualified people. There are many alternatives for finding more resources, including internal efficiencies, nontraditional approaches, and out-of-the-box thinking.
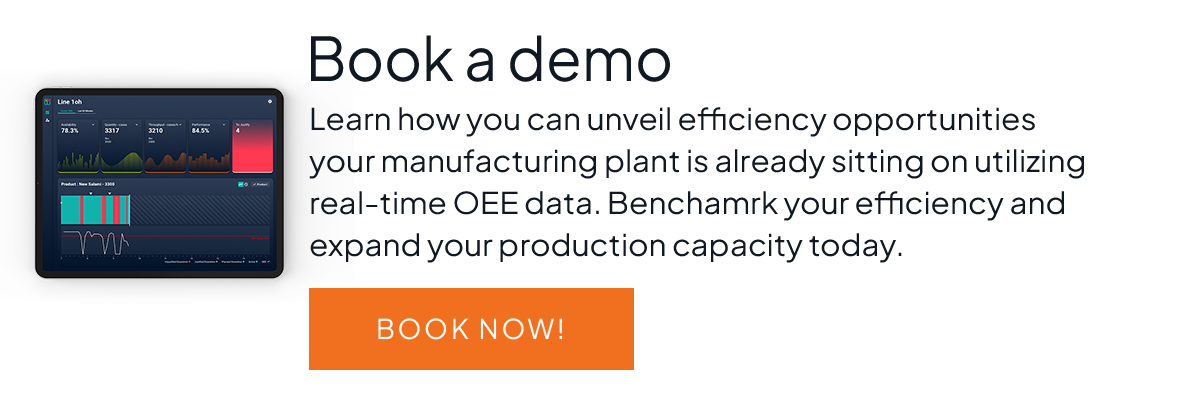