Within Lean Manufacturing, lean consultants often find that Overproduction has the most significant impact on the success of the business. Anytime that a part, assembly or final product is produced that is unable to be used or sold due to lack of an (internal or external) customer, the business has created Overproduction Waste.
In addition to the direct cost to the company of Overproduction Waste, Overproduction Waste can also contribute to Inventory or Transportation Waste, compounding the destruction of value for the business.
Overproduction Waste can happen when parts, assemblies or products are produced which are not needed, but also when items are produced before they are needed. In order to reduce overproduction waste that creates idle inventory, firms move away from 'Just in Case' manufacturing to 'Just in Time' manufacturing.
This change smooths workflow and can dramatically decrease WiP (Work in Process) inventory investment. Reducing WiP inventory frees capital to invest in other areas of the business such as automation and modern machinery and technology, thereby accelerating competitive advantage.
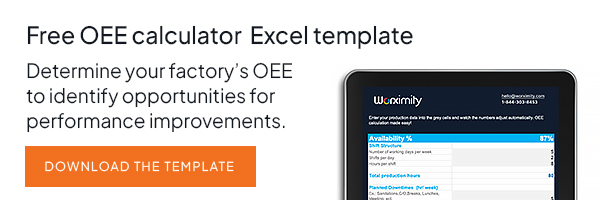
There are three commonly recommended steps to address Overproduction. First off using TAKT Time helps to even the rate of manufacturing between production stations. Then (second) addressing setup time is essential to reducing overproduction. By making setup times as short as possible, it becomes cost-effective to significantly reduce the size of production runs so that less overproduction is likely. Third you can implement a ‘pull’ system, or Kanban system to strictly control WiP.
There are still many organizations who ‘fly blind’, manufacturing parts, assemblies of finished products at a steady pace regardless of internal or external demand. The result is overproduction waste.
This Overproduction Waste can be due to:
- long setup times, leading to the desire for long production runs
- manufacturing ‘Just in Case’ items are needed internally or externally
- poor understanding of customer needs
- producing for a forecast as opposed to having inventory ‘pulled’ as it’s needed
- product design changes while existing designs are in process
- badly implemented automation
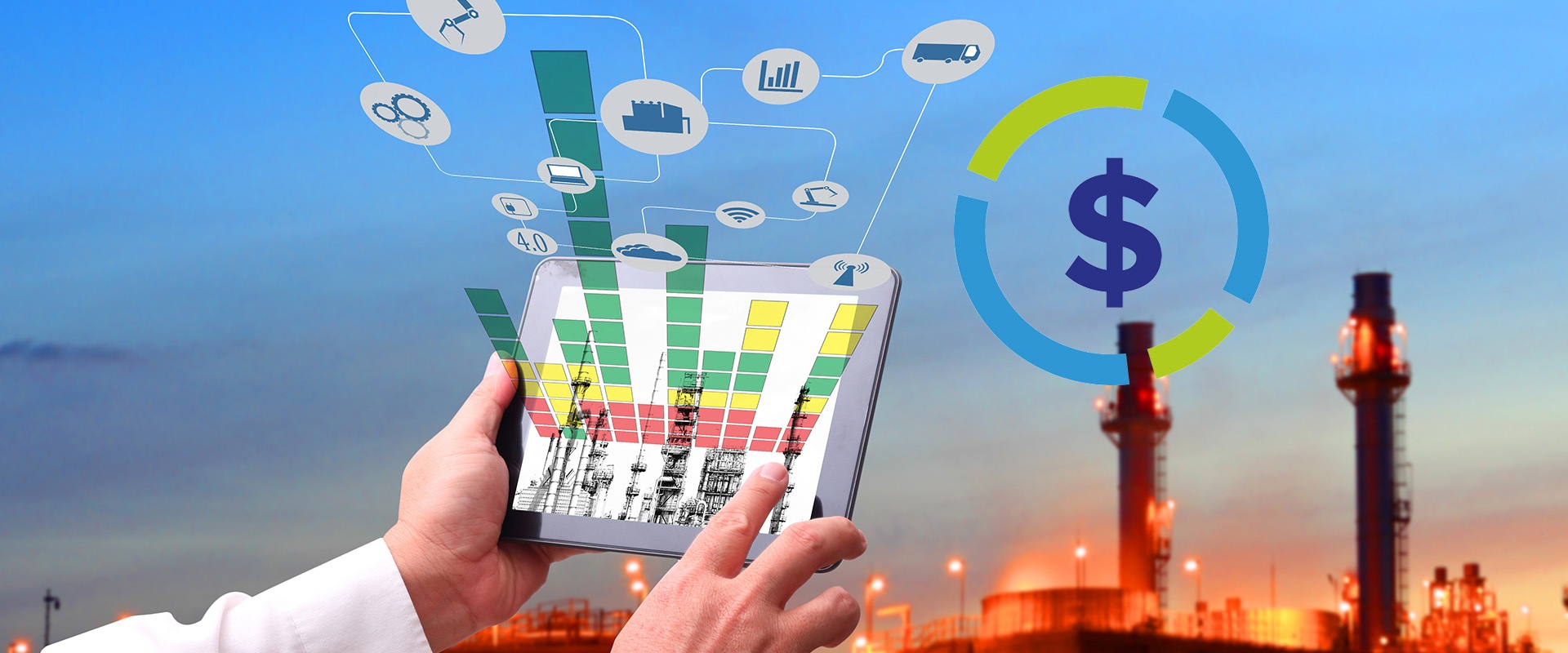
Best Practices for reducing Overproduction Waste in Lean Manufacturing includes ‘working from the end customer back’ so that all production benefits the end customer first. Getting to a ‘pull system’ from finish to start can eliminate virtually all overproduction waste. You can see however how you’d need to do things like eliminate setup times and bottlenecks so that your workflow is flexible from end to end.
This is how Overproduction Waste is eliminated in Lean Manufacturing.
"Overproduction doesn’t just occur on the shop floor. Producing printed reports that don’t provide actionable insights because they aren’t read, aren’t timely, or don’t have the information necessary to make good decisions is a form of overproduction. Using networked factory sensors to gather real-time information that can be presented in customized dashboards that provide fast, actionable information can reduce office Overproduction and lead to quick ROI." - Mathieu Pepin
The eight wastes of lean manufacturing can be remembered with the acronym DOWNTIME:
Read Types of Waste in Lean Manufacturing - Part 3 - Waiting Waste
Download our Free Lean Manufacturing Industry 4.0. to understand how technology can help you reduce your waste.
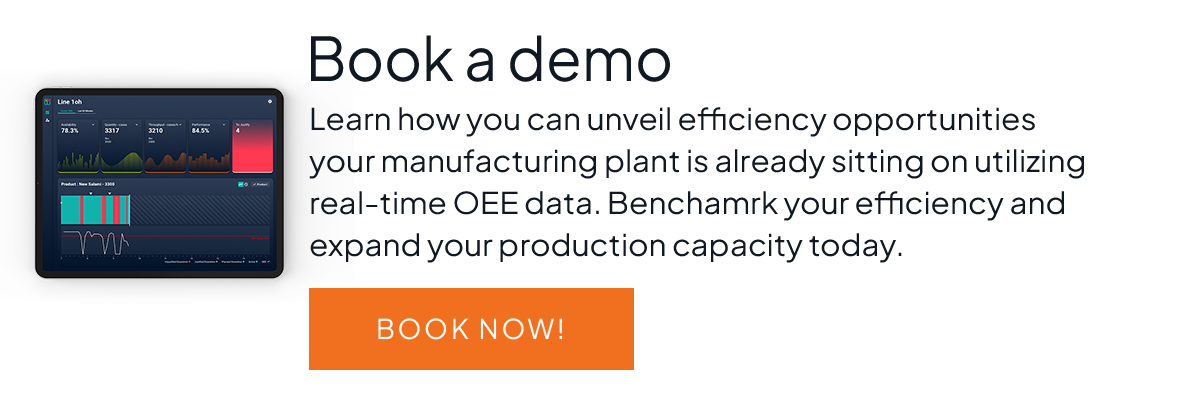