What is OEE?
Overall Equipment Effectiveness (OEE) is an important tool in lean manufacturing and continuous improvement. Considered today to be a best practice in manufacturing, the technique and theory was developed in the 1960s by Seiichi Nakajima as extension of the Kaizen system in Japan.
Smart Factory Analytics is breathing new life into OEE as a practice. Real time analytics can make all the difference in optimizing OEE...and the combination can be a game changer for manufacturers!
What makes OEE so useful?
By consolidating numerous KPIs into a single score like OEE, you can gain an immediate window into the total efficiency of a factory, shop, shift, or even a single machine. OEE does this by providing a framework for measuring productive manufacturing time, and giving a percentage based on the collected data according to three metrics.
There are two main ways to use OEE:
Measuring OEE on individual pieces of equipment or synchronized lines, enables us to monitor OEE factors in real time. Measuring OEE at the plant level monitors overall progress. By measuring for a particular machine or process you can identify problems as they occur and pinpoint the best improvement opportunities.
However, when you measure plant-wide OEE you gain a yardstick to measure the overall impact of your efforts through your OEE score, as well as the scores for the factors of OEE, such as availability, performance, and quality which gives detailed insights into what impact your efforts are making.
A Game Changing Solution - OEE + Smart Factory Analytics
The Internet of Things (IoT) is revolutionizing life and industries around the world, and OEE is no exception. In a manufacturing setting, IoT data collection tools make smart factory data analytics much easier to get access to, and can allow managers and production staff to monitor OEE in real-time. Being able to access OEE data for a production processes means that problems can be quickly addressed as they arise. Over time, patterns can emerge because data acquired directly into an analytics platform enables you to develop dashboards and reporting that can be difficult to generate using manually collected data and spreadsheets.
Using OEE to Determine Focus for Improvement
Different ranges of scores mean a different primary focus and different opportunity set for improving profitability. Even the most efficient plants are always trying to improve, but they have different focuses than average or lagging facilities.
To see how you stack up, you can see Average US OEE Rates Here and benchmarks to see if you're OEE is Best in Class here.
- In the best plants and above average plants (OEE of 70%) it is often best to focus on improving availability by focusing on reducing short-stops.
- For average performers (~50%-70%) equipment failures and other causes of unplanned major downtime are typically the biggest concern.
- For underperforming plants, (below 50%) it is most important to focus on tagging downtime events to provide improvement insights and reduce equipment failure.
Potential of OEE and Smart Factory Analytics
Implementation of OEE with smart factory analytics is revolutionizing manufacturing across industries. By 2022 the increase in efficiency from Smart factory and analytics is expected to add $500B to $1.5T to the global economy1, and the implementation of smart factory analytics is growing 7X faster than the general manufacturing industries growth rate.
There is also likely to be incredible productivity gains from OEE such as:
- 13X increase in the rate of improvement of on-time delivery of finished products
- 12X increase in the rate for quality indicators
- 12X increase in rate for CapEx & Inventory efficiency gains.
- 11X for logistics & transport costs reduction
- 7X for Overall Productivity improvements
- 9X for labor cost improvements
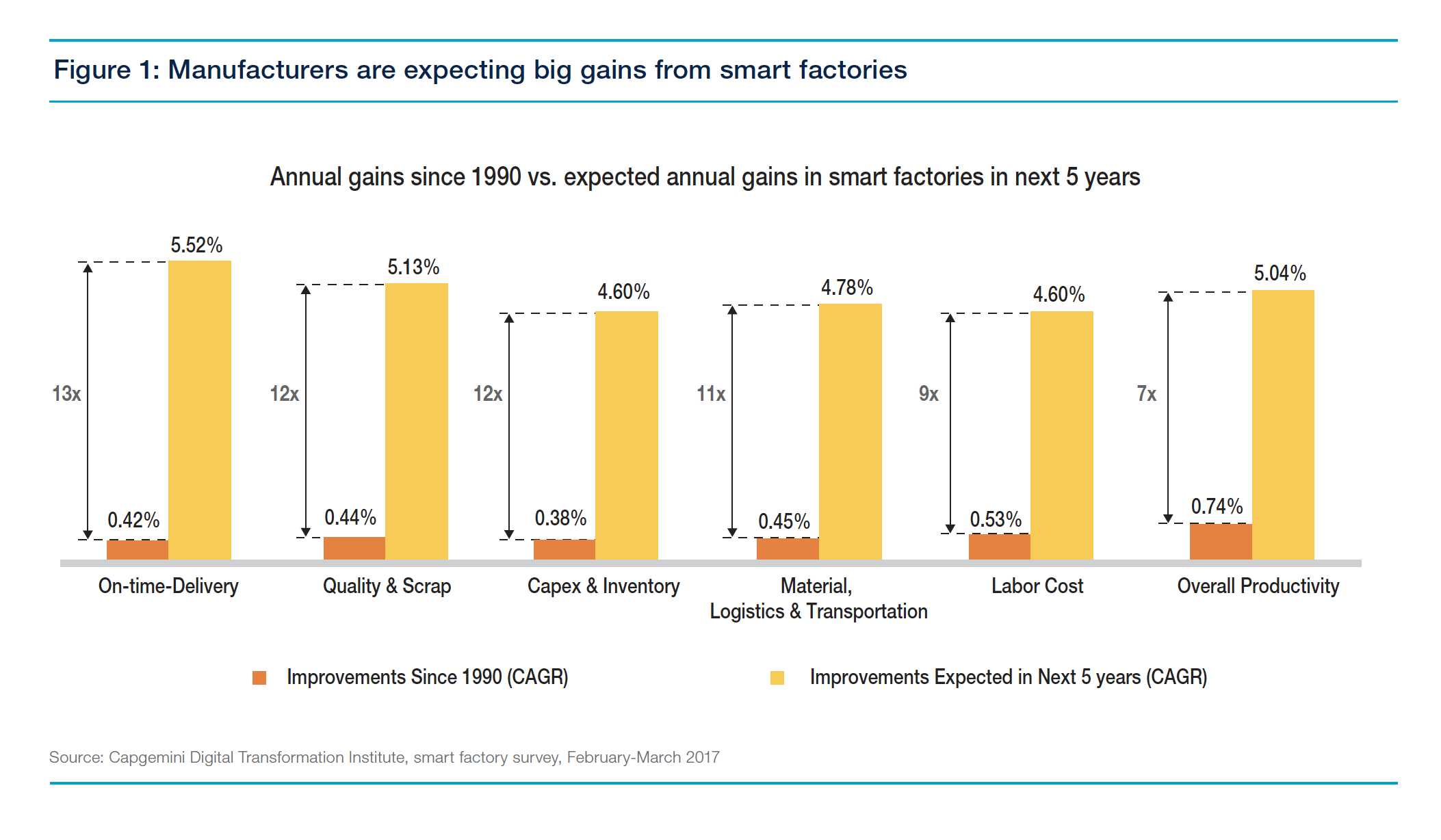
(Source: CapGemini)
Current Level of Implementation
OEE is a key to smart factory implementation, where the US is leading the world, with 54% of factories having operational smart factory initiatives, and an additional 36% planning to implement a system.
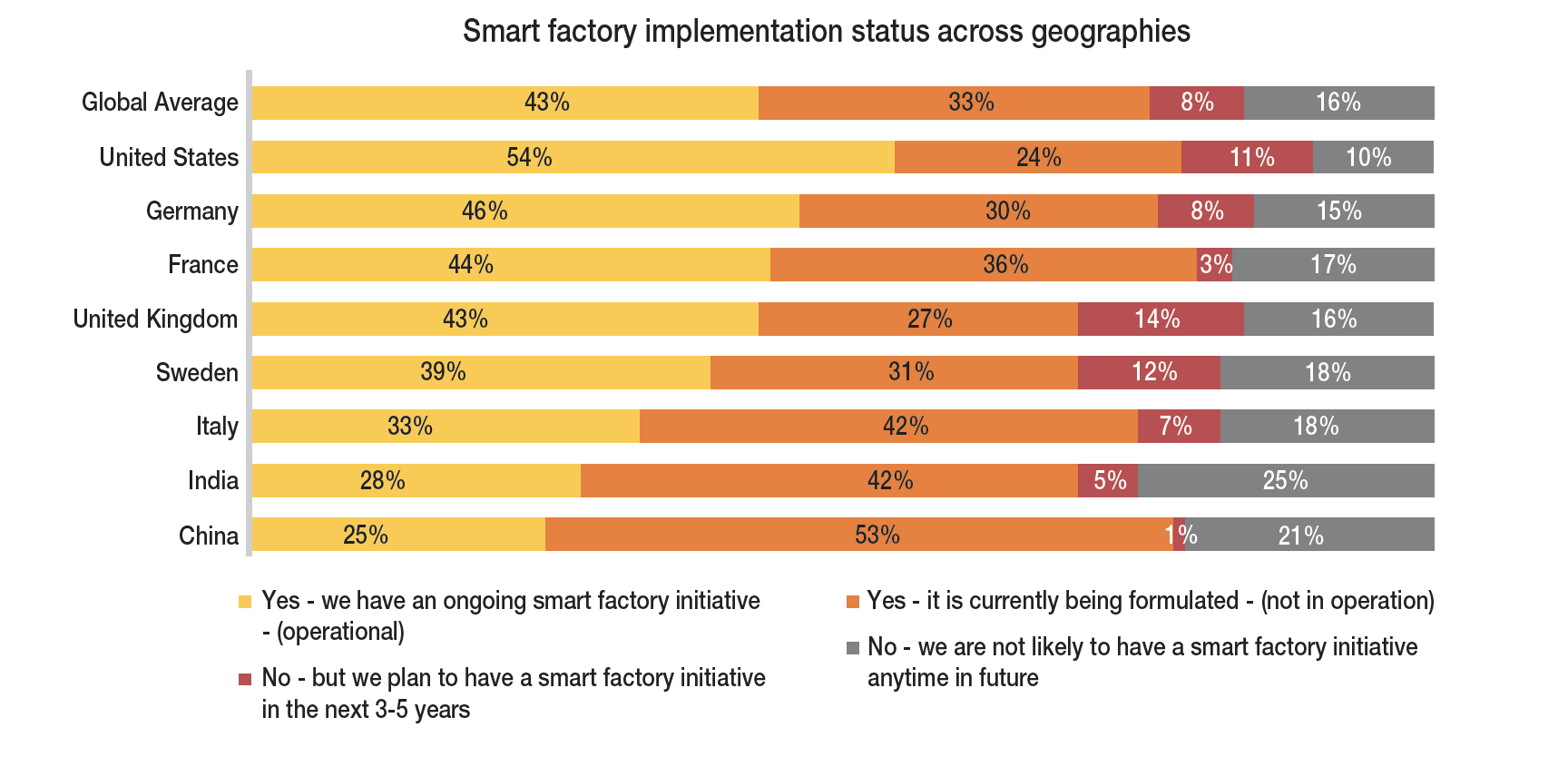
(Source: CapGemini)
OEE & Customer Service
As the smart factory revolution continues, customer standards are following suit. As customers become more aware of the impact of smart factory analytics, they are increasingly asking for or requiring accurate OEE reports, rather the approximation of metrics in traditional factories. Quality Smart Manufacturing and Internet of Things Technologies are vital for providing customer with this information, so that they can trust that finished products will arrive on time with high quality consistently.
Interested in more information on OEE and Smart Factory Analytics?
1 https://www.industryweek.com/technology/smart-factories-could-add-500-billion-global-economy-5-years