In virtually every manufacturing sector in North America, and in particular in the food industry, there is a big challenge...to hire and retain a competent workforce. Even with all of the technological advances in manufacturing processes, employees are still extraordinarily important to keep critical processes running and they’re getting harder to come by.
According to a report released by The Conference Board the demand for entry level blue-collar jobs in agribusiness, manufacturing, construction and the like has grown steadily since the trough in 2008 (due to the financial crisis) and in manufacturing alone, 57% of the predicted 3.5 million jobs that will exist by 2025 will go unfilled.
According to Gad Levanon, the lead report author for the report, “Compared to a few years ago, blue-collar workers are now much more likely to...experience rapid wage growth.”
Even with increasing pay, entry-level blue collar jobs tend to be lower paying than in other sectors of low skilled workers such as construction. This means that relatively low skill manufacturing workers have other opportunities, and that turnover in manufacturing floor jobs is high, and getting higher.
It is no wonder that challenges exist in hiring and retaining an adequate manufacturing workforce, particularly in food manufacturing. With that in mind it is important for manufacturers to compete to develop methods to remedy their blue-collar employment prospects. While base pay may not be able to move much, other programs can be created in order to attract and retain more prospective employees.
According to Daniel Pink, in his book Drive, beyond a reasonably competitive salary, there are three factors that motivate (and as a result, retain) employees:
Autonomy - the desire to experience self-direction.
Mastery - the urge to improve one’s skills
Purpose - the desire to do something that is perceived as important
Fortunately, these play right into Industry 4.0 and creating Workforce 4.0
Continuous Improvement (CI) processes rely on worker involvement. In order to facilitate CI, workers need to have the actionable information that they need in order to make good decisions. Industry 4.0 initiatives such as Smart Factory Analytics provides line workers with the information that they need gain Autonomy in their decision-making.
Focus on people and culture to drive transformation
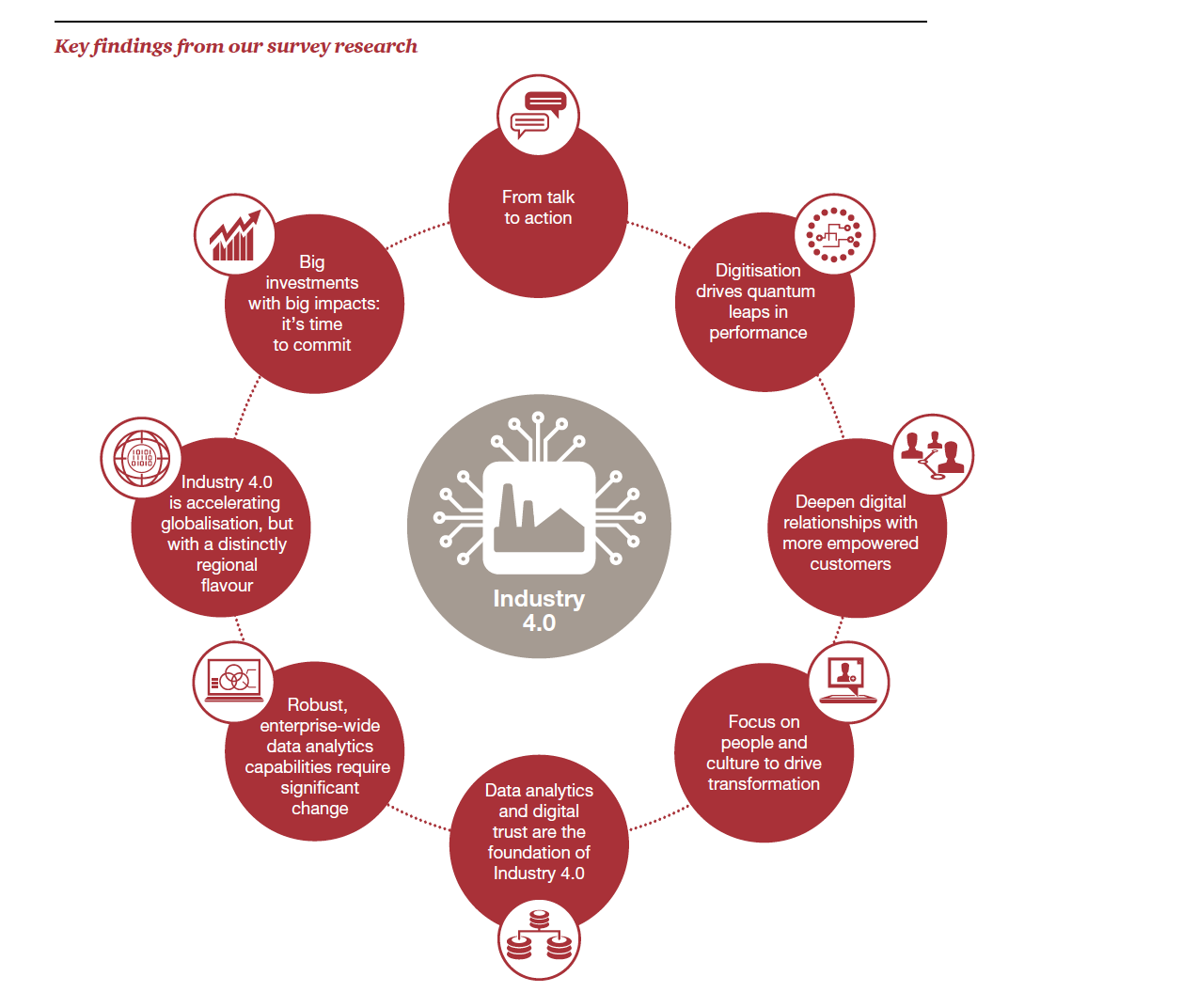
Image Courtesy PwC - Industry 4.0; Building the digital enterprise
From the PwC report Industry 4.0: Building the digital enterprise, they found 8 key findings, including that “Our survey respondents say that their biggest implementation challenge isn’t the right technology, it’s a lack of digital culture and skills in their organization. Industrial companies need to develop a robust digital culture and to make sure that change is driven by clear leadership from the C-suite.” In other words, companies that invest in training as they implement Industry 4.0 technologies, can not only gain competitive advantage against competitors that don’t but they’ll also find that workers are achieving Mastery...and therefore are more likely to be motivated and less likely to leave the company.
Employees who are involved in Lean Manufacturing implementations are helping to drive important sustainability changes as part of their work. This is one way that blue collar workers in manufacturing businesses can feel like they are making a larger difference, or Purpose through what they do in their daily jobs.
A contributing factor to the challenge of hiring a workforce in manufacturing, and in particular the food industry is that there is a lack of information about what it will look like in the near future. Sustainability, Lean Manufacturing, Continuous Improvement and Industry 4.0 are all initiatives that leading manufacturing companies are undertaking.
Gaining worker involvement through employee empowerment, providing mastery through training and offering a larger purpose through sustainability and investment in their own career paths can be the difference makers to compete for hard to find workers.
Want to begin to prepare your workforce for Industry 4.0? Get the guide here!