Over the past decade, the manufacturing industry has experienced what some may call "productivity stagnation and demand fragmentation", leading to a serious need for innovation. That's where the Fourth Industrial Revolution comes in. This revolution is bringing tremendous increases in efficiency with minimal worker displacement. McKinsey & Company has identified sixteen of what they named "lighthouses", being the world's most advanced companies implementing 4.0 technologies. As mentioned, "they demonstrate how forward-thinking engagement of technology can create a better, cleaner world through new levels of efficiency in manufacturing. Likewise, they illustrate how Fourth Industrial Technology at scale can transform the nature of work itself by upskilling and engaging human workers"
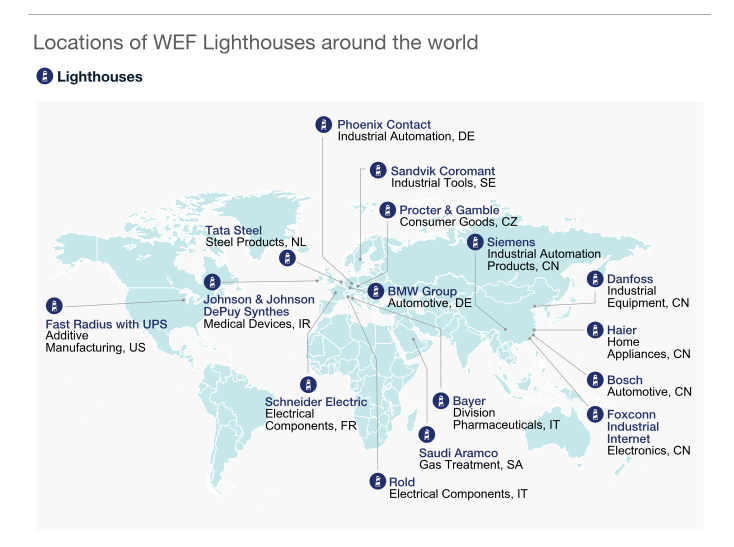
So what trends are driving this shift? Connectivity, flexible automation and intelligence. Technology adoption can have huge impacts on organizations. a McKinsey Global Institute analysis revealed that companies considered as laggards will have an important gap to bridge between companies that are currently opting for technologies such as artificial intelligence within the first five to seven years of falling behind. Those seen as forerunners are to expect a cumulative 122% cash flow change while followers will see impacts nearing 10%.
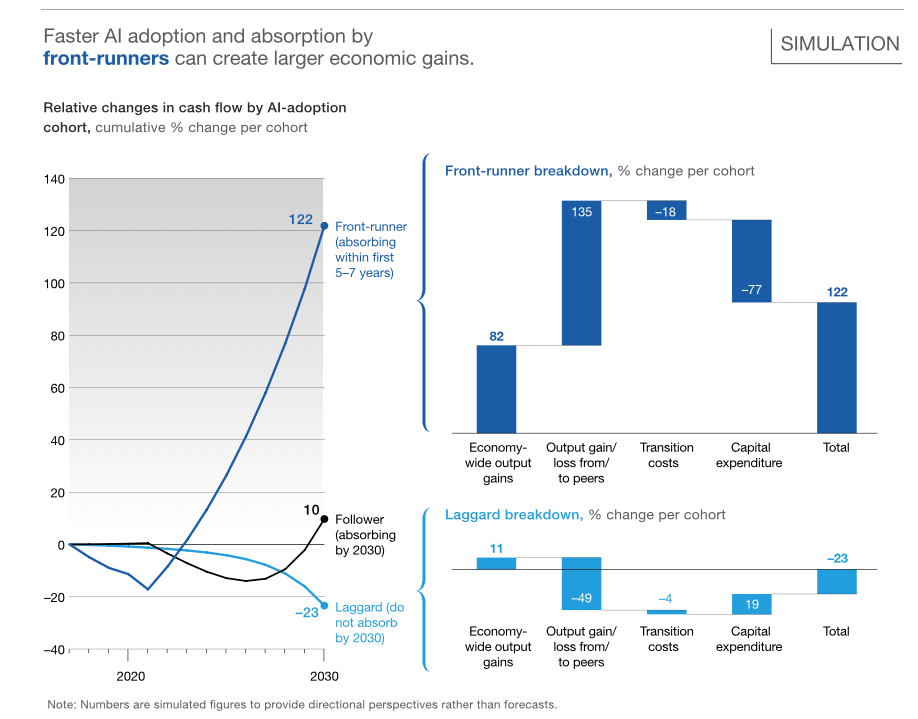
What does it mean to be a lighthouse?
What is it that these organizations do differently in their strategies, decision-making and daily operations? We will uncover what it is they do differently to fully take advantage of 4.0 advancements.
- Injections in human capital: Lighthouses are not aiming to replace their operators by 4.0 technologies. Instead, they invest in technologies that contribute to making their operators' tasks and routines less repetitive, more interesting, diversified and productive. In fact, a McKinsey report states that actually less than 5% of occupations consist of tasks that are completely automatable. On the other hand, 62% of professions have minimally 30% of their work that can be automated.
- Resetting benchmarks: Essentially, these organizations are redefining standards for operational and financial key performance indicators. By doing so, operations are altered, leading to performance increases. Consequently, with 4.0 technologies, they are able to further engage in continuous improvement initiatives.
- Open innovation and collaboration: To succeed in your shift to 4.0 manufacturing, it's important to surround yourself with the right enablers. More often than not, lighthouses are involved in ecosystems that foster innovation such as universities, start-ups, small-medium enterprises, and other technology suppliers.
- Minimal replacement of equipment: Your current equipment does not represent a barrier to innovation. Hefty investments in your facilities are not necessary to implement 4.0 technologies. Many of these lighthouses only transformed existing, underdeveloped operations.
Now that you've learned more on the characteristics that make lighthouses front-runners in terms of innovation, the second article will cover some methods and value drivers to scale this shift within your factories.
Stay tuned!
To consult McKinsey & Company's full report, click here.