While noticing where, when, and how rejects occur are all important considerations to make when trying to improve production efficiency, the tools used to measure and log rejects are just as important.
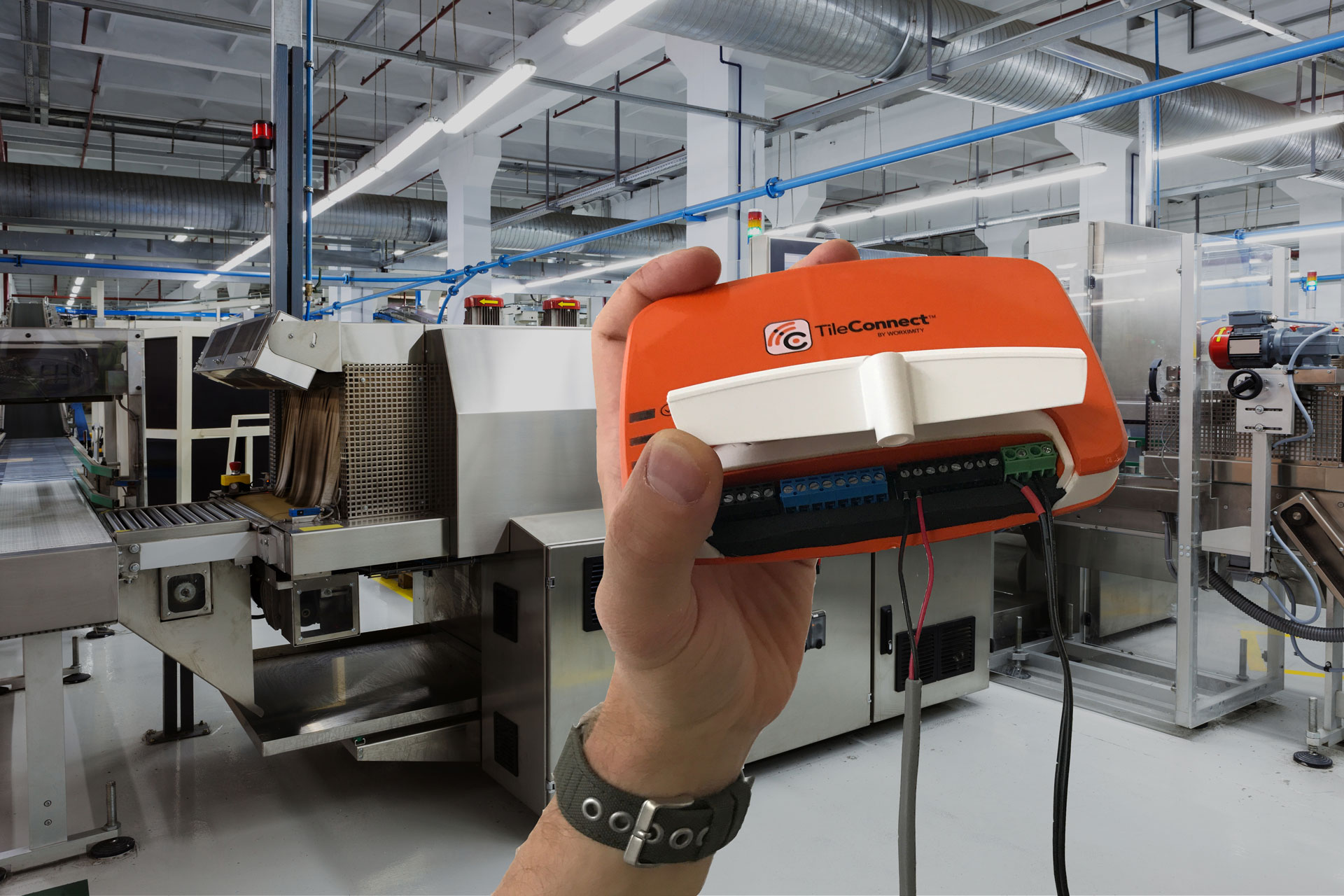
One method of measuring and logging rejects is with a quality control worker who manually checks the product for quality and records data by hand, with paper or via manual entry in a computer. While this method works, it wastes time, labor, and is costly in the long run.
Measuring the parts via autonomous technology, by sensor or automatic micrometer for example, is a much faster and more accurate quality control check, as it is not subjected to human error. Besides improving accuracy, an autonomous reject system will also improve insight into the problem, potentially taking preventative action before the problem occurs. With this type of system, more “checkpoints” can be created (perhaps even one after every manufacturing process) allowing problems to be found as they arise. Autonomous data entry will also save labor, as an employee no longer has to do it on the clock.
While the design of these systems are largely industry and plant specific, converting and using an autonomous measuring and logging system for rejects will safe time, materials, money, and improve the overall efficiency of the production process.