In order for manufacturing companies to adhere to the principles of lean manufacturing, mistakes and defects must be properly defined, addressed, and ultimately prevented in an effective and efficient manner. This means accounting for anyone or thing that is involved in the manufacturing process.
In order to implement this goal into reality, the manufacturing process should be viewed as a dynamic process that is robust enough to react when things don’t go as planned. This requires that every component is aware of the current state of the product, as defined by its location in the assembly line, weight, motion etc. All of these objectives can be attributed to the broad philosophy called Poka-yoke which was first championed by engineers at Toyota as part of the Toyota Production System which was developed in the mid 20th century.
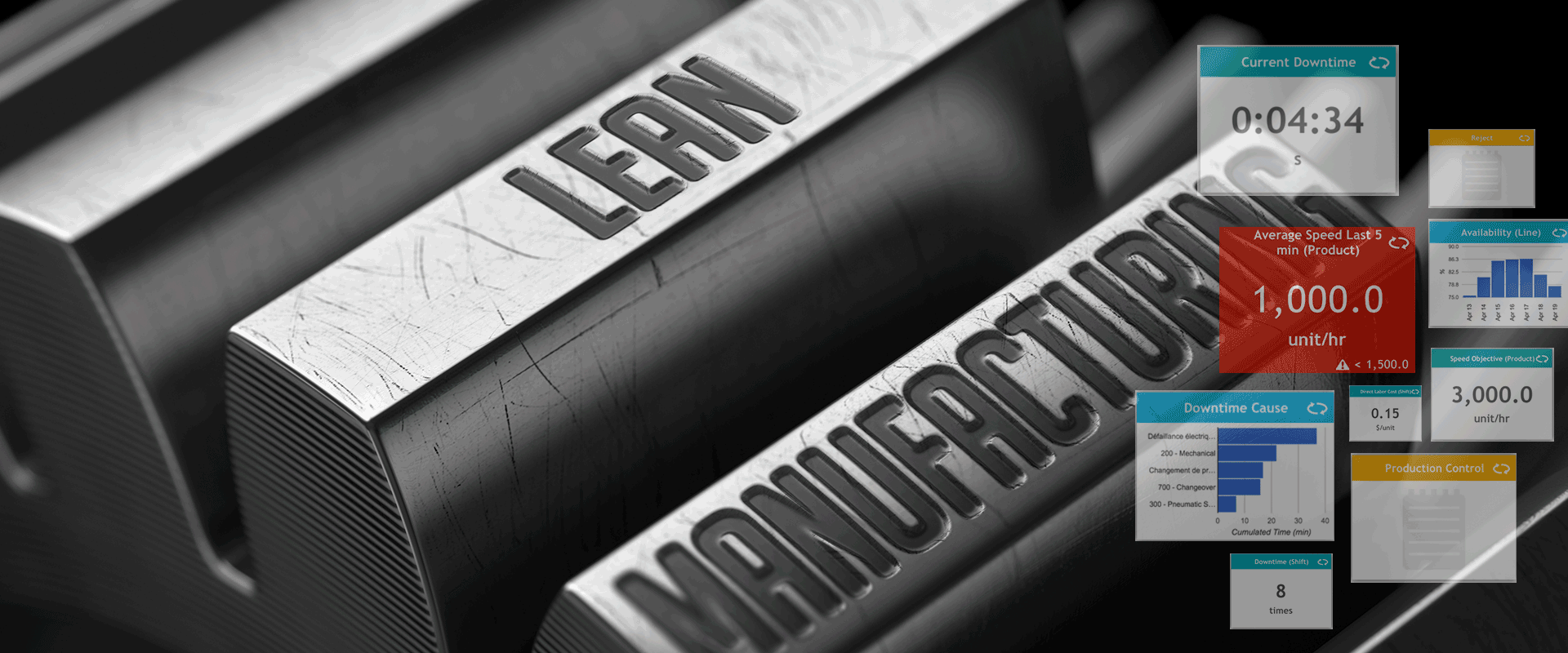
Poka-Yoke, the definition
Poka-yoke roughly translates to mistake-proofing in English, and a Poka-yoke device is anything that prevents an error from occurring within the manufacturing process or is used to make defects easily detectable so that they can be sorted or fixed.
Poka-Yoke, the scope
A Poka-yoke device can span from something that only exists in the manufacturing plant, to a part of the end design that is meant to prevent misuse by the end user. The three pronged outlet plug is often seen as an example of the latter.
The following paragraphs will go over the types of Poka Yoke device often used within the manufacturing plant.
- Contact
- Fixed Value
- Motion/Step
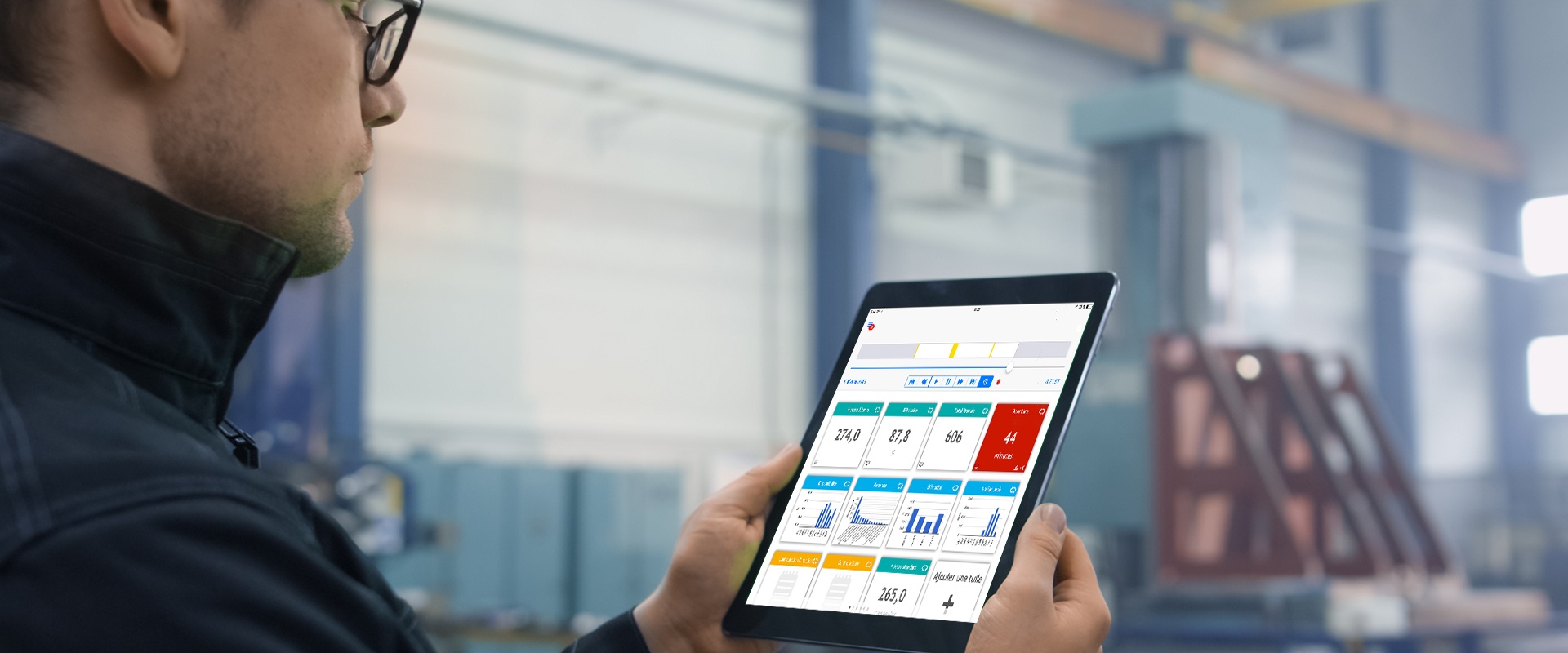
Poka-Yoke, the contact Method:
A Poka-yoke device within the contact method category is used to inform components of the manufacturing process, whether it be a person or machine, about the current state of the product by detecting a physical contact or contact with a source of energy (i.e. electricity, photoelectric beam).
Poka-Yoke, the Common Error Prevention Examples:
- Limit Switch: Activated when contact is made. This can be used to ensure that a hole is driven to the correct depth.
- Electrode: When conductive parts are used, their presence can be detected by using an electrode which closes a circuit when contact is made.
- Guide Blocks/Pins: Used to ensure proper alignment of a part by simply including custom pins or rails in a workstation design to constrain the location of the part to one obvious location.
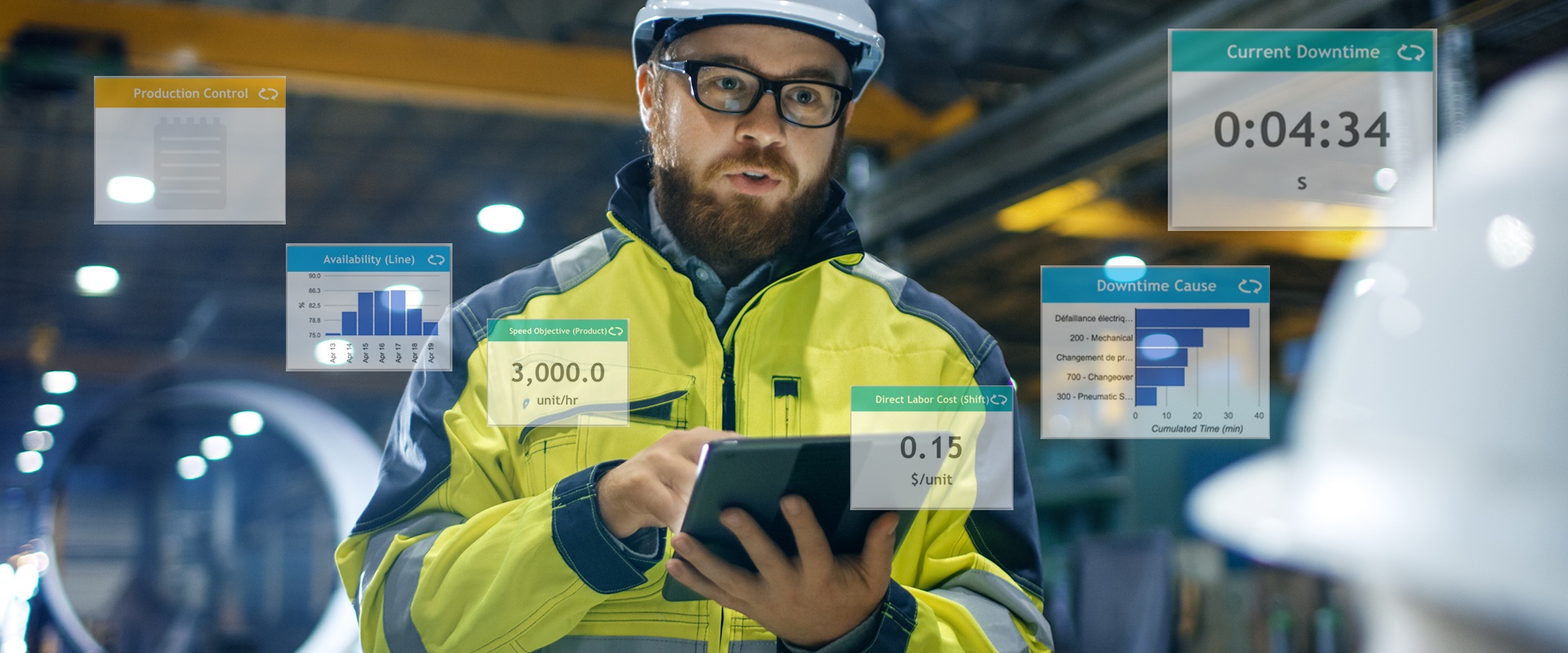
Poka-Yoke, the Common Error Detection Examples:
- Weight Sensors: Quick and easy way to determine if a product is missing pieces.
- Dimension Sensors: Could be implemented by physical inspection or a built-in feature (i.e. a mesh that only lets items of a certain size through).
- Part Bins: These can be used to track if the correct number of parts have been included in a design a particular workstation.
These are just a few examples of how errors can be prevented and detected by taking advantage of existing devices and technologies that use physical contact as the mode of detection. This idea is unanimous in any manufacturing application, but the ways in which it is implemented can vary widely depending on given process and materials being used.
Fixed Value Method:
The fixed value method applies to sources of error that arise when a certain fixed value is not met. This could simply be the number of screws in a part, the torque that a bolt is limited by, or the number of times a product is labeled. Whatever the manufacturing application, there are bound to be processes within the workflow that require a fixed value to be met in order to meet quality standards.
The following examples give an idea of how these types of errors can be eradicated.
Common Error Prevention Examples:
- Counters: Simple devices that measure occurrences, via contact, motion.
- Logic Controllers: If a certain number of operations aren’t completed at a workstation, a controller can stop the conveyor belt to eliminate the error from propagating.
- Part Dispensers: At a workstation, a dispenser can feed the prescribed amount of a part into a part bin, such that each cycle results in an empty bin to ensure that the right amount was used.
Common Error Detection Examples:
- Part Bins
- Lights/Alarms: A more general tactic for detecting errors, but can be implemented of be triggered by a lack of a fixed value.
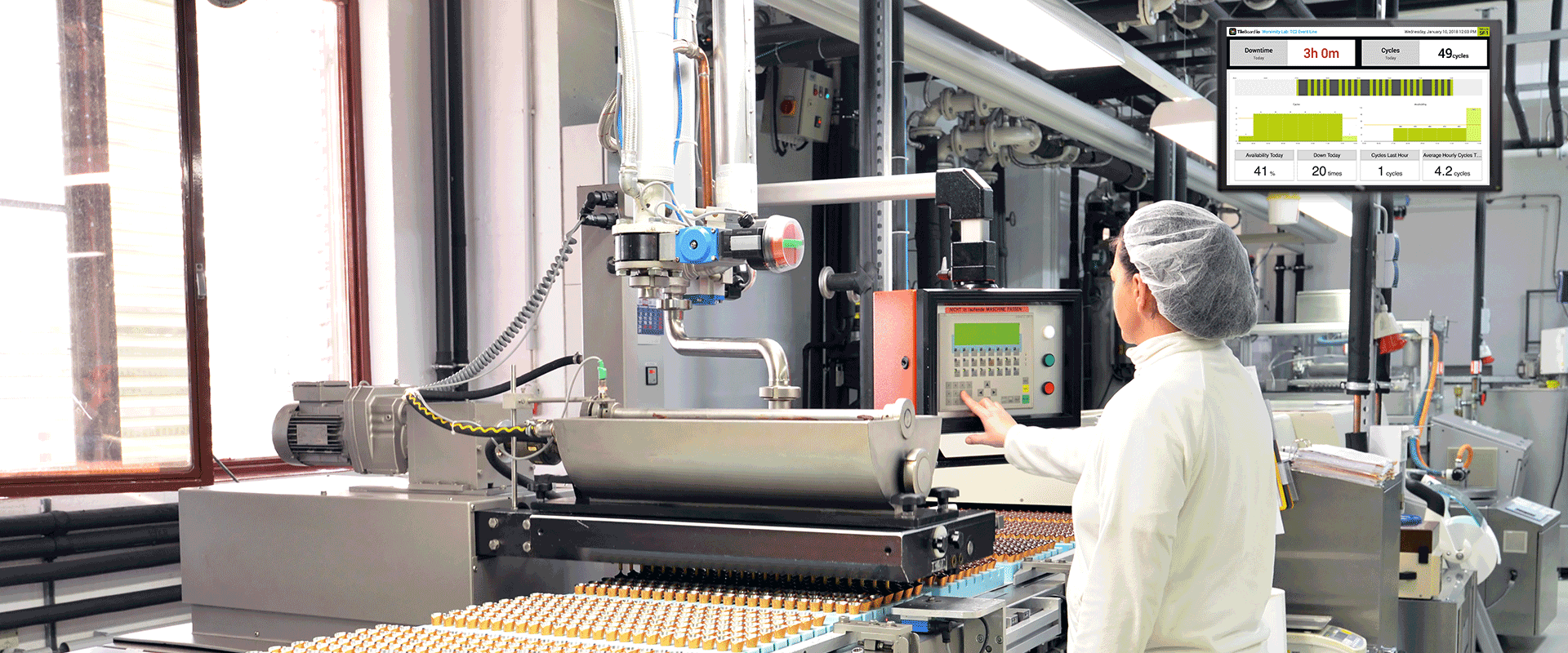
Motion/Step:
The final broad category of Poka-Yoke devices is related to preventing and detecting errors stemming from an improper sequence of events. The manufacturing process can be informed of such errors by implementing any one of the examples below, among other techniques:
Common Error Prevention Examples:
- Timed Gate/Switch: Used to track if a process happens in the correct amount of time.
- Numbering Scheme: Having prescribed parts be in the order of assembly.
- Ordered Instructions: Having instructions at workstations be in a fixed order.
- Successive Checks: Having multiple people check an item as it is passed down the line to get quick feedback.
Takeaway:
The use of Poka Yoke devices will only be successful if the following questions are answered first:
- What causes errors?
- Why are errors occurring?
- Is there an easy way to detect if an error occurred?
- In the event of an error, how can it be contained or isolated?
Once these questions are addressed and answered, the right Poka Yoke device will become apparent.
Click here for more on Lean Manufacturing concepts
References:
- Tutorial, www.mistakeproofing.com/tutorial.html.
- Dolcemascolo, Darren. Mistake Proofing Poka Yoke Lean Overview, www.emsstrategies.com/dd110104article1.html.
- “POKA-YOKE.” Reference for Business, www.referenceforbusiness.com/management/Or-Pr/Poka-Yoke.html.
- “Poka Yoke.” Lean Manufacturing Tools, leanmanufacturingtools.org/494/poka-yoke/.
- “Toyota Production System.” Wikipedia, Wikimedia Foundation, 16 Mar. 2018, en.wikipedia.org/wiki/Toyota_Production_System.