In the 4th quarter of 2019, trade uncertainty and trade wars are dominating business headlines. A recent article in The Wall Street Journal, Trade Uncertainty Clouds Global Growth Prospects is typical of the current news environment. In the article, they note that…”small steps toward a trade truce between China and the U.S. last week likely aren’t enough to diminish uncertainties that are holding back global economic growth”.
You’d think that this would be the number one issue concerning manufacturing executives. Astoundingly, it’s not.
According to the most recent quarterly executive survey by NAM (The National Association of Manufacturers), while in 2018 manufacturing executive optimism had hit an all-time high with 95.1% of executives holding a positive outlook for manufacturing, the last two quarters have seen a historic drop in manufacturers’ outlook, accelerating a worrisome trend. In the third quarter of 2019, we were down to 67.9% of manufacturing respondents saying that they were either somewhat or very positive about their own company’s outlook. This is an unprecedented drop in manufacturing executive sentiment, with the decline in optimism plummeting from 95.1% positive, to 89.5% holding a positive view through 79.8% and now 67.9% of manufacturers holding a positive view of their own future prospects.
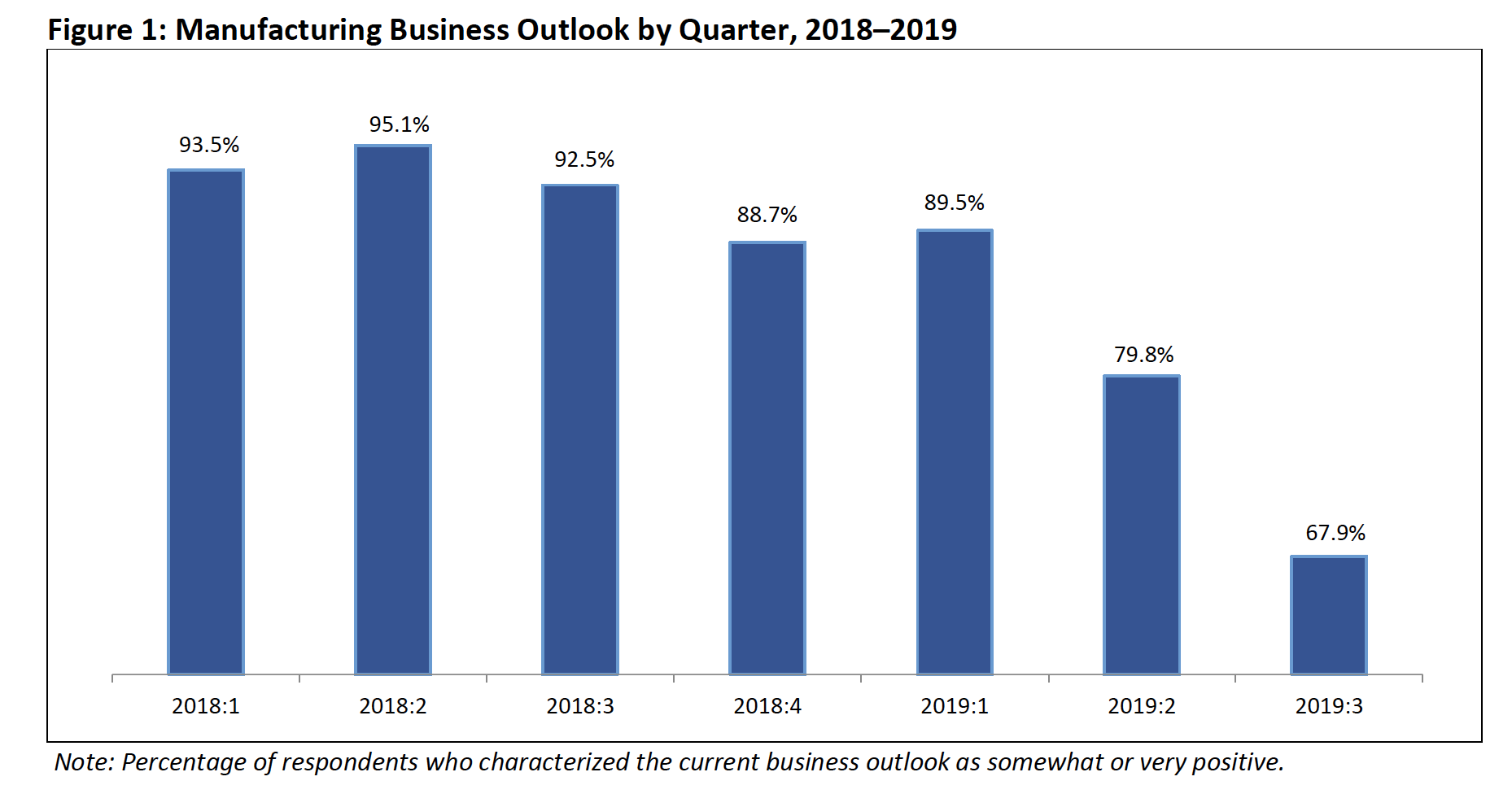
Image Courtesy - NAM Executive Confidence Survey Q4 2019
Was trade uncertainty the number one driver of this increasingly pessimistic view? No, it was the increasing desperation in filling skilled labor jobs, with no relief in sight.
The survey reports that labor shortages are severe, with a crisis looming on the horizon. 78.7% of respondents said that they have open positions that they cannot fill, and one-third of respondents noted that they are now forced to turn down new business because they cannot find talent.
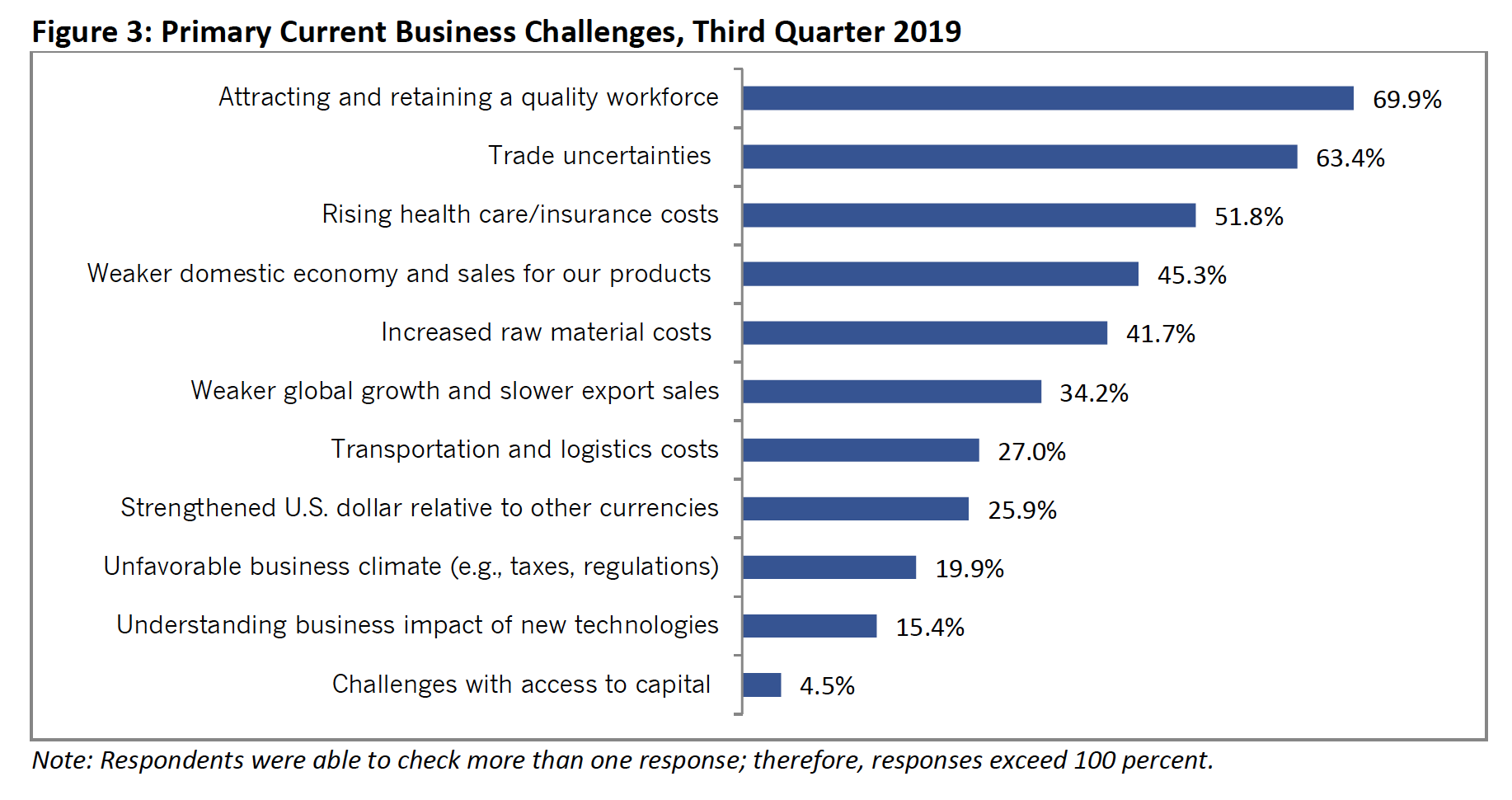
Image Courtesy - NAM Executive Confidence Survey Q4 2019
The number one concern of manufacturing executives isn't trade uncertainty, its attracting and retaining a quality workforce!
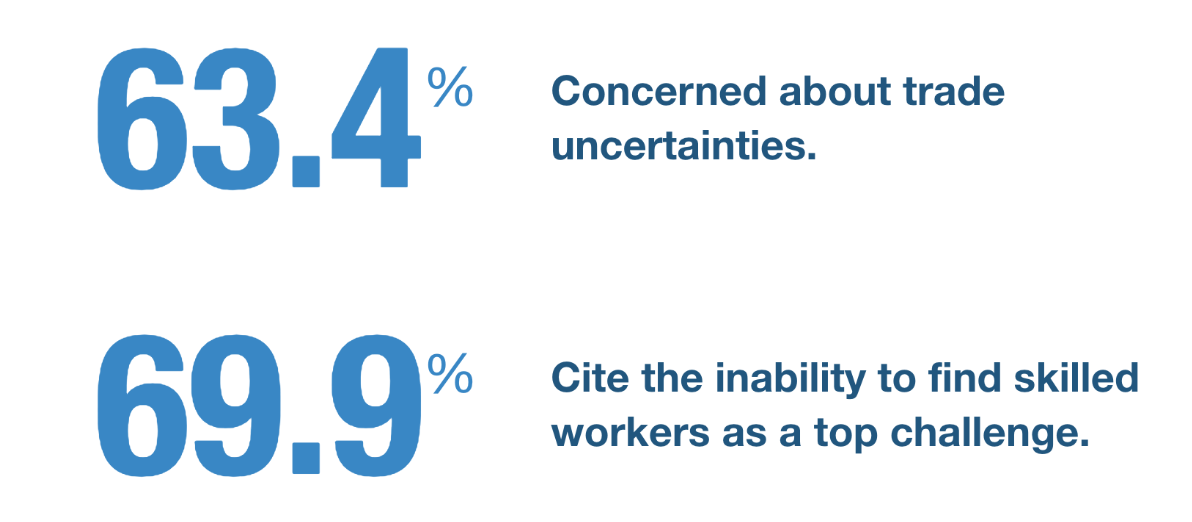
To add further pain for manufacturers, according to a joint study by Deloitte and The Manufacturing Institute, by 2028 “additional manufacturing value added of US$454 billion could be at risk if qualified workers cannot be found to fill the open jobs”, that loss in revenue represents an incredible 17% of the total projected US manufacturing GDP for 2028.
In Deloittes companion report, the Manufacturing Skills Gap Study:
"Manufacturers in the United States are experiencing some of the highest levels of growth we’ve seen in decades, yet the industry seems unable to keep up with the resulting rebound in job growth,” said Paul Wellener, vice chairman, Deloitte LLP, and US industrial products and construction leader. “With nearly 2 million vacant new jobs expected by 2028, compounded by 2.69 million vacancies from retiring workers, the number of open positions could be greater than ever and might pose not only a major challenge for manufacturers but may threaten the vitality of the industry and our economy."
What can manufacturers do to respond to this crisis?
We all know that manufacturers are investing in automation, but interestingly the most innovative manufacturers are taking a completely different tack.
Deloitte also surfaced some surprising insights in these studies. They’ve identified two major barriers to recruitment of skilled labor into manufacturing.
The first is public perception, and the second is the approach to recruiting taken by manufacturers.
It turns out that despite significant investments in technology and automation, the public has a dated view of what manufacturing employment looks like today. Manufacturing jobs are largely viewed as unstable, due to a history of layoffs across manufacturing sectors. However, it turns out that the bigger barriers to recruitment are that manufacturing jobs are largely viewed as non-technical vs. say building apps, and are viewed as relatively unsafe.
Manufacturers that are taking these insights to heart are turning to changing the perception of their target recruiting audiences through changing their messaging. Large companies with budgets can afford to run TV commercials, such as the Caterpillar ‘Let’s do the Work’ campaign. However, smaller manufacturers can do things to change the perception of their prospective workforce regarding the opportunity for prospective workers to learn advanced technologies.
By featuring what once were repetitive line manufacturing jobs as being powered by Smart Analytics, manufacturers can turn their investments in Industry 4.0 into a recruiting message.
With the ability to monitor manufacturing 24 / 7 anytime / anywhere via a Manufacturing Analytics SaaS solution, the opportunity exists for manufacturers to embrace the remote / work from home opportunities that tech companies have taken advantage of to expand their workforce.
Monitoring critical or hazardous processes with Industry 4.0 technologies that can eliminate employee risk and embracing other IIoT safety technologies such as wearables that monitor and prevent nearby hazards can go a long way to helping businesses make the case for manufacturing being far safer than it ever was. While manufacturers have been investing in these technologies, they’ve largely kept this news to themselves, unwittingly limiting their own recruitment opportunities.
Deloitte also determined that manufacturers also have an outdated perception of what makes the right employee.
Many manufacturing companies still have a rigid hiring criteria based upon relevant past experience and years in an industry. This stifles the opportunity to expand the recruitment pool. With the investment in technologies such as real-time machine analytics, lesser experienced workers can be placed into roles that previously might have required significant experience but now can be filled by someone who has the intelligence to learn on the job and the creative capacity to problem solve while being supported by real-time insights delivered on via an iPad or mobile device.
Besides revealing new insights that manufacturers can improve their image regarding their use of advanced technologies and improvements in safety, Deloitte of course concluded that another opportunity to improve recruitment is through increasing wages. This can be difficult for manufacturers without a corresponding increase in productivity to cover the wage increase. Fortunately, investments in IIoT technology can lead to significant productivity improvements, enabling manufacturers to confidently explore increased wages that can help fill those jobs that enable the company to take on more business.
Despite the seemingly dire outlook for manufacturing labor shortages, there are creative steps that manufacturers can take to improve their own outlook. These are predicated on investing in Industry 4.0 technologies while thinking in terms of marketing these investments to prospective employees. Manufacturers can help future employees to understand their tech-based career prospects, their increased safety, the manufacturers newfound ability to be flexible with work arrangements and the ability for manufacturers to compensate employees with increased wages for working with them to increase productivity.
Interested in learning more about revolutionizing your business with Industry 4.0 technologies? Get the guide below!