Overall Equipment Effectiveness (OEE) is a vital part of any manufacturing company’s continuous improvement initiative. The system provides a powerful framework for determining the causes of waste in a factory, and showing how they interact and compound. But like any system, to make it work the user must understand the pieces. This article is a breakdown of all the necessary terms one must understand to implement OEE in their workplace.
Overall Equipment Effectiveness (OEE)
This term refers to percent of Fully Productive Work accomplished during Planned Production Time, and takes into account all losses. Fully Productive Work refers to work that directly contributes to creating value, excluding maintenance and changeout. Planned Production Time is the term used to describe the total time minus the Schedule Loss, or all time the factory is meant to be actively manufacturing.
Loss Factors
The Loss Factors are the individual pieces that subtract from a perfect OEE score of 100%. These Loss Factors are Availability Loss, Performance Loss, and Quality Loss
Availability Loss is the loss derived from Planned and Unplanned Stops during Planned Production Time. A Planned Stop is a period of changeover, setup, or a make-ready event during which no value is produced. An Unplanned Stop is a stop due to equipment failure, which halts production.
Performance Loss considers Slow Cycles and Small Stops during production. A Slow Cycle is any cycle that takes longer than the Ideal Cycle Time, which is the theoretical maximum speed at which a discrete item may be produced. A Small Stop, also called a Minor Stop or Idling is counted as any pause in production that is not significant enough to be tracked as Stop Time.
Quality Loss refers to the loss incurred by faulty parts, including Rework Parts. This is measured as a combination of Startup Loss and Process Loss. Startup Loss or Reduced Yield includes all defective parts produced from startup until equipment reaches stable (steady-state) production. Process Loss includes any defective part made once the production is stable. A Rework Part is a part that although initially rejected, can be fixed and sold to the customer. However, due to the fact that its initial production was not purely value-adding time, that time is counted as a loss.
Altogether, Planned and Unplanned Stops, Slow Cycles and Small Stops, and Startup Loss and Process Loss are known as the Big Six Losses.
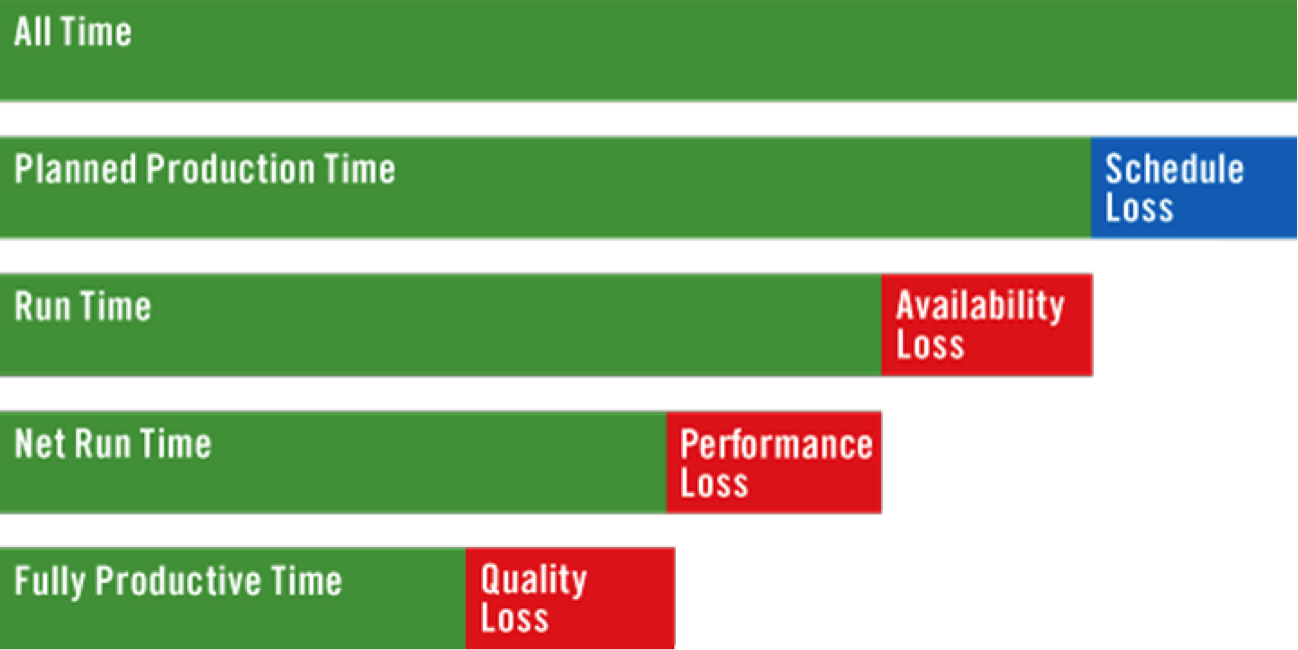
Know Your OEE Terms Courtesy https://www.leanproduction.com/oee.html
Loss and Time
Given the many different variables that go into OEE, it isn’t surprising that there are also many ways to describe the interplay of the various losses. And because of the time-based nature of OEE, these terms describe loss in relation to the Big Six Losses and All Time.
All Time covers the entire duration of the work day, equipment functioning and no. Planned Production Time is defined as All Time minus Scheduled Loss, which was already defined above.
Run Time is the Planned Production Time minus the Availability Loss. This is the duration of time during which equipment is actively producing value, ignoring Small Stops and Idling.
Net Run Time is the Run Time minus Performance Loss. This is the most detailed measure of the time loss due to equipment not functional at optimum capacity.
Finally, Fully Productive Time is defined as the Net Run Time minus the Quality Loss. This metric takes Net Run Time, and discounts any time during production where loss was incurred by creating a defective part. The ratio of Fully Productive Time to Planned Production Time is how the OEE is calculated. The resulting number is a percentage out of 100, which takes into account every loss as it compounds.
Being able to effectively use the language of OEE will ensure a smooth implementation of the system. By having a common understanding of the underlying theory behind each term, management and workers alike can avoid confusion and successfully carry out important continuous improvement in their factory.
Worximity is deeply committed to the philosophies of Continuous Improvement and Lean Manufacturing in food manufacturing. Using our IoT technology we provide company wide visibility into the statistics that matter to manufacturers and accelerate TTV (Time to Value) of investments in company culture and training to achieve outstanding productivity.