Meat producers and transformers have everything to gain by monitoring their operations in real time. During many key stages of the transformation process, it is possible to collect data that will give you a quick picture of the current situation. Is your equipment operating at full capacity? What is your OEE? Could you optimize your yield? Are you systematically losing money because of overproduction? Are some products just not profitable? Are the right people working on the right production lines?
So many questions, all of which can be answered thanks to real-time data collection and by monitoring your KPIs on an intuitive dashboard. To help you out, we've therefore prepared a series of 5 posts, each of which describes one of the five key measures you should be keeping an eye on:
.png)
KPI #1 - Downtime
The objective is to reduce start-up times, the time required to make product changes, set up time in the morning and the time required to solve any mechanical problems. By connecting packaging lines equipped with machines such as Multivac's Thermoforming packaging machine, it is possible to follow in real time the duration of downtime events, downtime frequency and the principal causes of your downtime.
The slaughtering, deboning lines and cutting lines are also usual bottlenecks in meat transformation factories. By installing sensors that can identify downtime occurences and provide relevant information regarding same (some are even equipped with alarms to notify plant managers when a downtime event lasts longer than the established standards), your teams' reaction time will be improved.
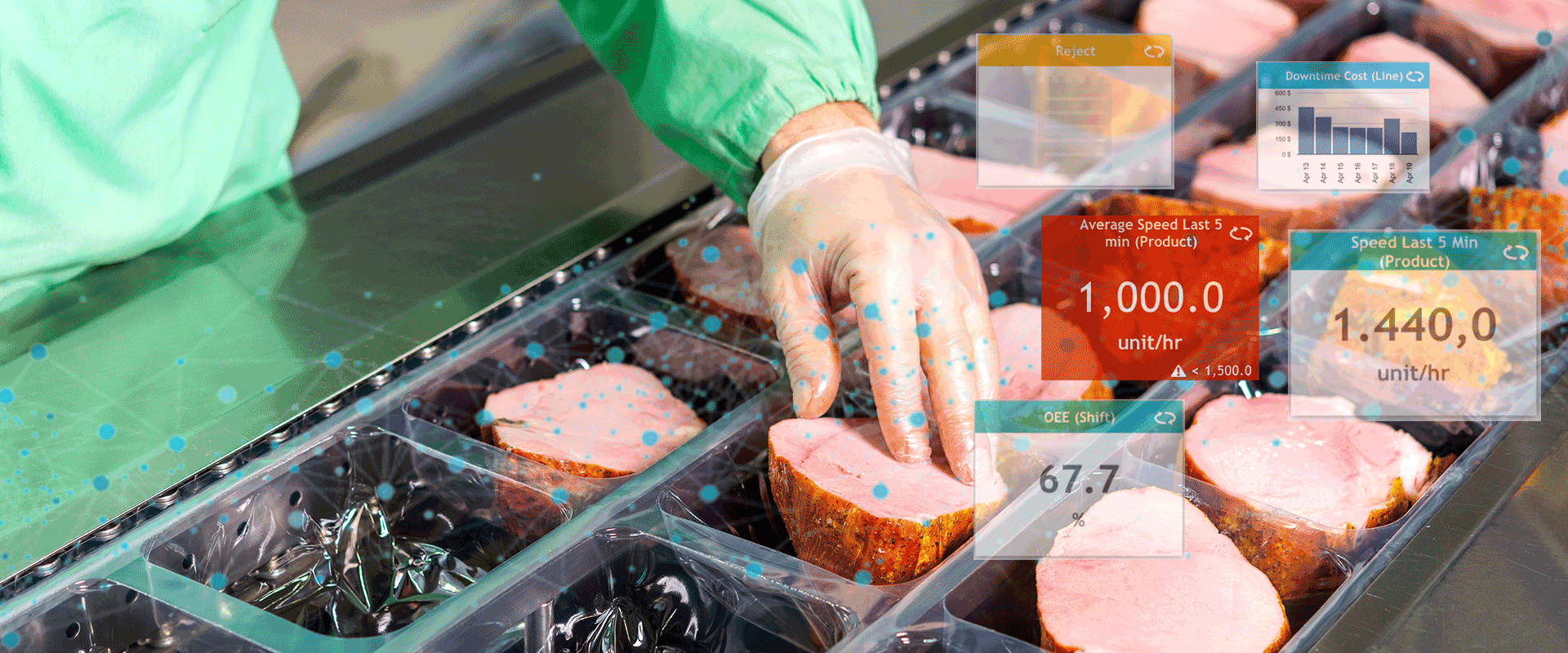
Reducing downtime, a case study.
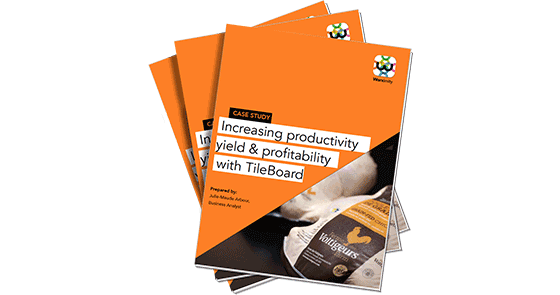
DISCOVER HOW VOLTIGEURS FARMS IMPROVED ITS PRODUCTIVITY AND ITS YIELD AND INCREASED ITS PROFITABILITY THANKS TO TILEBOARD.
« Worximity offered some flexible solutions that were adapted to my needs and corresponded to my vision of things. You have to be creative when looking at data in order to better collect it, combine it and make it meaningful. TileBoard helps me look at my company from a different perspective and I can only imagine what we will be able to accomplish in the next years as smarter connectivity solutions become available.»
Junior Martel, Director, Operations and Commercialization
Voltigeurs Farms
Read 5 Critical KPIs That Meat Processors Should Monitor in Real Time - Part 2