Thermoforming food packaging is a complex process, which leaves it ripe for upset conditions and downtime. It’s quite common for the thermoforming packaging line to be the bottleneck in a food production operation, and frustratingly for food manufacturing operations managers or lean practitioners, because of the nature of various thermoformed package processes, the bottlenecks can be intermittent and hard to predict. With the pressure on food manufacturers to package an ever wider range of products on one packaging line, reducing thermoforming machine downtime can be even more difficult.
Multivac is the leading manufacturer worldwide of thermoforming packaging machines for food processing. Multivac delivers over 1,000 thermoforming packaging machines every year worldwide and Multivac thermoforming machines strike a perfect balance of standardization and customizability. When optimizing thermoforming packaging lines, one common recommendation is to standardize where possible, and use ready-made package designs. This can reduce the impact of poor package design on productivity, throughput and downtime. However, there are times when marketing and product development has good reason to require a custom package design. Multivac straddles both worlds well, with standard options but high customizability.

Standard Thermoformed Plastic Food Container, Courtesy Multivac
Food packaging thermoforming processes typically use the following steps:
Package Design: The design of the package is critical to thermoforming process success and reduced downtime. Standardized packages lets food manufacturers take advantage of the deep knowledge that exists to reliably produce a widely used package made from a known plastic compound. As you’ll see in the following, there are so many factors that need to be managed in a typical thermoforming operation that dialing in and running your own package design can produce a situation where you have to learn on your own which factors are critical to reliability and quality.
A core part of package design is material selection. There are a number of plastic (HDPE - high density polyethylene, LDPE - low density polyethylene, PP - polypropylene, PET - polyethylene terephthalate, Styrofoam - polystyrene are the most common) types which can be thermoformed for food packaging, and within each individual type plastic compound manufacturers will provide their own compounds and material mechanical specifications. Knowing that the right material is being selected and that the material will be available cost-competitively at acceptable quality for the design life of the packaging line is vital. Switching packaging materials in a thermoforming packaging line can introduce seemingly invisible variables that can impact production rates, downtime rates and product quality.
Process Selection: Below are some of the wide variety of package thermoforming processes. Some require auxiliary systems such as vacuum, pressure and cooling, which increases system complexity and introduces more downtime failure points. An experienced packaging engineer should be engaged when implementing a new thermoforming packaging line.
Mold Development: With a package design in place, which includes material selection, a qualified mold maker is engaged to produce molds. Like with the thermoforming material selection, molds come in a range of materials. Since thermal conductivity of the mold is an important factor in production reliability, the ability to efficiently and effectively clean the mold affects downtime and product quality, the avoidance of micropores which can’t be cleaned is a food grade standard and corrosion management and durability of the mold often create trade offs, a seasoned engineer or mold provider is recommended. In engineering metals, material selection for thermal conductivity, corrosion resistance and wear resistance are often at odds and an experienced designer can help you to understand these tradeoffs and make a good design selection.
Sheet Feeding: Sheet feeding itself has a few options:
The entry point of most thermoforming packaging lines is the sheet (or web) of formable plastic. Thermoforming by design requires a ‘thermoplastic’ which is a plastic that becomes soft and formable at a higher temperature than ambient room temperature. The opposite of ‘thermoplastic’ is ‘thermoset’ which are plastics that are crystalline in nature and won’t soften with heat. This means that the plastic selection is somewhat limited to the range of plastics which are able to be thermoformed and not all plastics are available for this process.
The sheet may be on rolls, in which case the need to change out rolls as they empty is a requirement. Alternatively, a larger investment is an extrusion line, whereby pellets are driven through a heated plastic extrusion process (usually a screw pump with a heated jacket) and passed through rolls which form the sheet. The advantage of adding an extrusion line is that it can run continuously, reducing a critical and costly contributor of thermoforming downtime, which is roll changes. The disadvantages of introducing an extrusion process at the front of the thermoforming packaging line is the considerable added capital expense and the added complexity of adding machinery and controls to operate and maintain the extrusion system.
Package Molding Processes: There are 4 typical food package thermoforming processes. Three of these processes center upon molding a food package to accept the food product and one is sealing a film over or around the packaged food after the package is filled.
Male / Female Mold: Thermoform molding can be accomplished with a male and female mold, which is what most people think of when they think of molding. The plastic sheet is drawn between two mold halves, the mold halves come together and form the part and then the mold halves separate. The part is then either pulled from the female mold or ejected off of the male mold. Two part molds are most often used when molded parts need to meet a tighter geometric tolerance.
Vacuum Molding: In vacuum molding, the sheet is positioned over a one-part mold and vacuum draws the plastic up into a female mold. This can be less expensive than investing in both a male and female mold but the part tolerances may be looser as the part may not tightly be drawn into the mold. This process also introduces a vacuum system which can introduce process variability and maintenance costs.
Pressure Molding: Pressure molding as you can imagine is the opposite of vacuum molding. In this process the plastic sheet is positioned over the mold and pressure pushes the plastic film onto, or into, the mold. Pressure molding is a compromise between vacuum molding in that applying pressure will often form the plastic to tighter tolerances in or on the mold but you don’t need to buy or maintain a second mold half. Again though, providing pressure means that you need complex equipment and controls to operate and maintain.
Heat Sealing: Heat sealing means applying a film around or over a package and sealing the package tightly to maintain food freshness. Blister packs often have a printed film applied which is heat sealed to the container after filling while meats are often wrapped in a clear plastic which is heat sealed on the bottom.
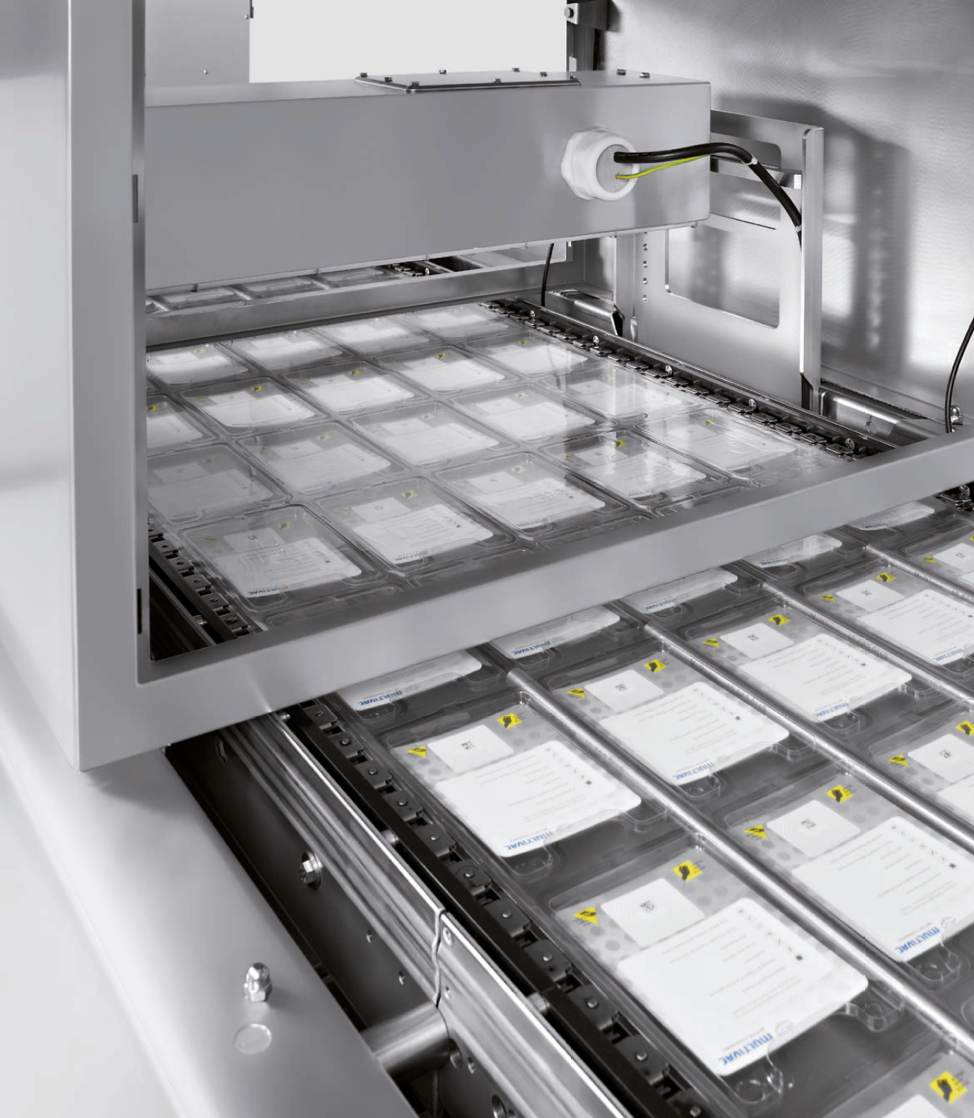
Example of food packaging with thermoformed bottom package and film sealed cover. Courtesy Multivac
A thermoforming packaging line often is integrated with label printing, inspection and box or container packaging to produce a final product ready for shipment.
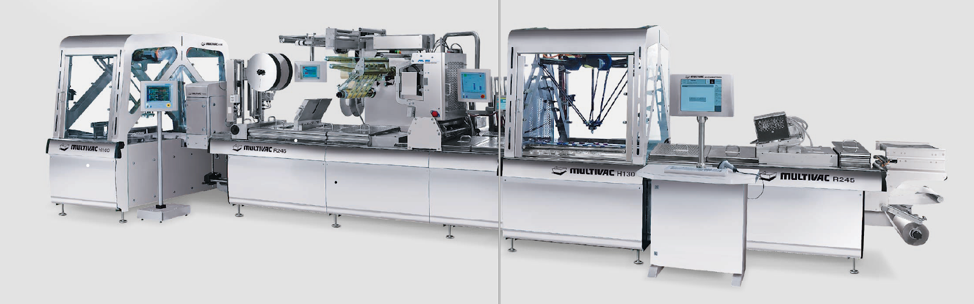
Example of an integrated thermoformed packaging line which includes thermoforming packaging, product feed, product labeling and final inspection, Courtesy Multivac
As you can see, food packaged thermoforming can be an extraordinarily complex set of steps to keep operating reliably! This can make reducing downtime a challenge for thermoforming package system operators.
What causes food package thermoforming downtime and how can Worximity help you to keep your thermoforming packaging equipment, such as Multivac, operating reliably?
Worximity and Thermoforming Material Feed
Thermoforming processes manipulate a plastic sheet in order to produce a thermoformed package. The reliability of the plastics supplier to deliver a plastic sheet that consistently meets specs is vital to eliminating downtime. Thermoforming processes can jam with poor plastic sheet quality. Formed container products may not reliably release from the mold, or products may fall out of tolerance if the plastic raw material varies too much. Some containers must maintain the right level of translucency or transparency or accept printing or labeling well, and plastic sheet variability can affect all of these properties.
A Smart Factory Analytics tool such as Worximity can monitor the thermoforming machine to show you when an upset condition occurs. This lets your operators quickly address sheet misfeeds, jammed rolls and poor quality product, reducing downtime and increasing OEE.
Worximity and Thermoforming Material Heating
The sheet coming off of the roll, or being delivered from an extruder is passed through an oven to heat it to just the right temperature in order for reliable thermoforming. In addition to variability in the sheet material, variability in sheet speed through the oven or in internal oven conditions can cause upset conditions like those mentioned above and lead to downtime. This can be difficult to maintain when product changeovers are frequent, as different products will require dialing in different oven parameters. Lines that are started before oven temperatures adjust or if the speed is not adjusted properly can lead to production downtimes.
Sheet coming from an extruder has an advantage that the incoming sheet to the oven is often delivered at a consistent temperature throughout the thickness of the sheet, being still warm from the extrusion process. Sheets being fed from rolls has to be heated from the outside to the center, and thicker plastics may be difficult to heat all the way through consistently, leading to thermoforming variability and downtimes. Sheets that are not hot enough may not fully form and sheets that are overheated may ‘sag’ during the thermoforming process leading to inconsistent quality of product.
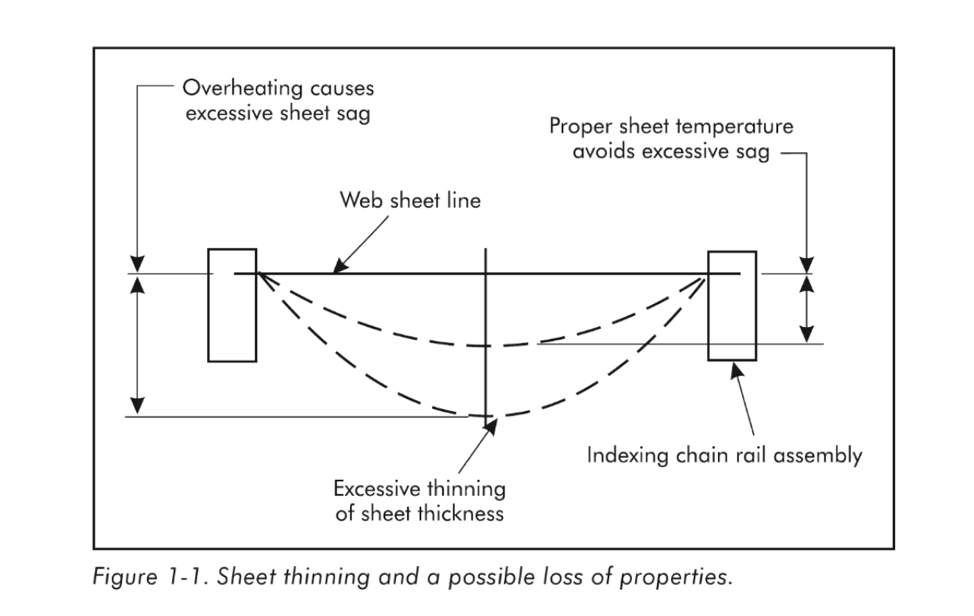
Thermoforming heating issues. Courtesy Thermoforming: Improving Process Performance
The ability to monitor machine and oven parameters can position thermoforming operators to see processes moving out of tolerance and act proactively to adjust parameters to keep the process operating at production speed. Worximity provides the adaptability to tap into both machine data in order to position operators to have a real time dashboard that they can respond to in real time and prevent downtime.
Worximity and Thermoforming
The thermoforming molding process has mechanical attributes, such as mold opening and closing acceleration and velocity as well as support system attributes such as vacuum / pressure, cooling water temperature and flow and more, all of which contribute to reliability and uptime.
Having the ability to tie monitoring and real time visibility into disparate systems such as those across a complex system like a Multivac integrated system is a strength of Worximity to reduce thermoforming downtime such as with Multivac system.
Worximity and Thermoformed Package Trimming
Package trimming can be subject to issues such as mis-alignment or wear. Inspection systems such as high speed visual inspection are often used to monitor trimming accuracy and quality.
Tying the outputs of these systems into an integrated dashboard such as Worximity can provide proactive scheduling of the replacement of wear components to reduce unplanned downtime.
Summary of Issues that can cause downtime which Worximity can prevent in Multivac thermoforming systems:
Sheet:
- Sheet material too thick
- Sheet material too thin
- Sheet material poor, inconsistent or off-spec mechanical properties
- Sheet roll near end of roll / sheet not feeding
- Sheet roll changeover time and frequency
- Downtime times and frequency
Heating:
- Sheet velocity through oven
- Oven temperature and status of key oven components
- Downtime times and frequency
Vacuum / Pressure:
- Vacuum or pressure statistics and status of systems
- Downtime times and frequency
Cooling / Heating Systems:
- Key component, motor, pump, valve status
- Operating temperatures at key points
- Downtime times and frequency
Thermoforming:
- Mold starts and stops due to poor quality or products hanging up
- Critical mold factors, acceleration, velocity, key temperature points.
- Downtime for cleaning or setting up a different product
- Downtime times and frequency
Trimming:
- Status of trimming operation
- Number of cycles indicating wear
- Visual inspection systems indicating out of tolerance
- Downtime times and frequency
Product quality:
- Status of visual inspection for product translucency or transparency
- Product reject rates
Production Rates:
- Rates of product inputs and outputs at a macro-level
- Overall Downtime times and frequency
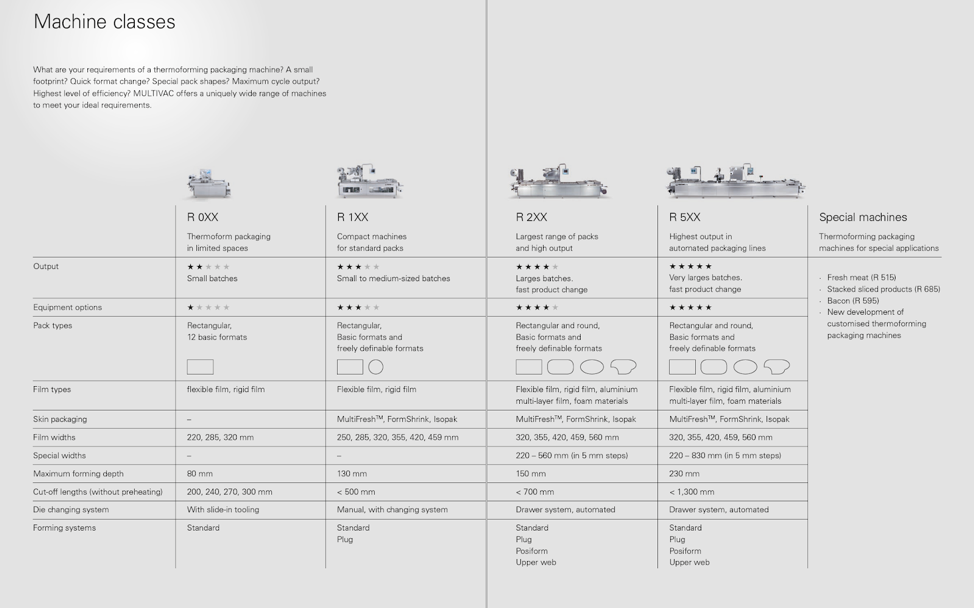
Multivac provides a wide range of thermoformed package line systems, which balance standardization and customization well. Courtesy Multivac
Why add Worximity to an existing thermoforming system such as a Multivac system when there are already controls in place?
As shown above, a manufacturer such as Multivac often will develop a standardized set of products and options in order to remain competitive. While there may be some flexibility in options, because of the specific nature of a given thermoplastic package line, the monitoring available may not be specific enough to deliver high throughput and low downtimes.
Additionally, a Smart Factory Analytics solution such as Worximity can provide a dashboard for each key role in the process, increasing the availability of real time insights and reducing response times to downtime events.
Perhaps most importantly, Worximity can be configured to gather a wide range of interrelated parameters over an extended period of time. This allows for retroactive analysis to spot trends which can pinpoint opportunities to reduce thermoforming line downtimes.
If you're operating or considering implementing a food packaging thermoforming line, such as those made by Multivac, talk to a Worximity specialist and learn about our proven thermoforming downtime reduction implementations.