There’s a lot of talk and content about Industry 4.0, IIoT (Industrial Internet of Things) and related topics such as Smart Factory Analytics. It can be difficult sometimes for a manufacturer to discern what of this information is hype and what is factual, or at least what is applicable in the real world.
One way to look at all of this from a manufacturers perspective is to step back and try to define ‘what is our vision as a manufacturer looking forward into the future?’. To help you out with this exercise, we did a survey of the ‘factory of the future’ information landscape and created a summary here with handy links to help you to establish your vision as a manufacturer.
We wanted to take a broad look at what is possible in the not too distant future as well as what leading factories are doing today. We also wanted to provide you with some reference points so that you can assess where your company is today on your factory of the future journey and to create a vision of what is possible for your company in the not-too-distant future.
A key theme that runs through our research is reference to ‘digitization’. technologies such as the ‘digitized factory’ or ‘factory digitization’. The ‘Factory of the Future’ is another theme.
We explored these two themes for you and you can read about our reporting for you below.
CB Insights, in their article Future Factory: How Technology Is Transforming Manufacturing has identified 8 key criteria for a factory to officially be a ‘factory of the future’. The way that they organized these criteria we found interesting.
Most articles on IIoT technology for manufacturing tend to focus ‘from the bottom up’. What we mean by this is that they present an inventory of available technologies such as IoT sensors or VR goggles and work they way ‘up’ to potential applications and solutions for manufacturing. In the CB Insights article, they take a different approach. They work from the start of the manufacturing process (product development) and work to the end of the manufacturing process (product distribution). This creates an interesting and comprehensive viewpoint.
You can weigh your opportunity and progress for factory digitalization against these 8 criteria, but before we get there, we’d like to take a look at what manufacturing companies are doing today for IIoT implementations.
How are companies doing generally? In 2015, PwC surveyed more than 2,000 companies from 26 countries in the industrial production sectors, including engineering and industrial manufacturing.
One-third of the respondents said their company had already achieved advanced levels of integration and digitization, and 72% expected to reach that point by 2020. ‘An overwhelming majority (86%) of the survey respondents said that on the basis of their experience to date, they expected to see both cost reductions and revenue gains from their advanced digitization efforts’ says the PwC study. This means that there’s progress, but certainly against the CB Insights criteria, for all but the most advanced manufacturing businesses, there will be a long way to go to achieve full factory digitalization and become a factory of the future.
How factory digitalization began and what does it mean?
Smart Factory technologies are a subset of factory digitization technologies. Digitization is the process by which factories evolve to become factories of the future. It is a representation of the 21st-century factory that is built on integrating data and human assets. There are numerous recent technological developments that are coming together to drive this manufacturing revolution. Factory digitization is a response to the need for companies to continuously improve their operations, increase productivity, improve quality, deliver a wider proliferation of products on demand all while lowering costs. This need will continue far into the future.
Factory digitalization is the implementation of IIoT technologies across the entire value chain, including while processes are occurring within a factory as well as before and after a specific manufacturer adds value.
Companies are embracing factory digitization technologies to:
improve economic efficiency
gain the ability to be proactive rather than reactive
shorten product development and introduction cycles
radically compress delivery cycles
enable a vast proliferation of products to be produced with equal, or even far fewer, resources
integrate with higher-order value chains to mesh with supply chains that extend from the consumer back to raw materials
improve safety
Examples of Factory Digitization and Existing Factories of the Future:
One company that’s pioneering advanced factory digitalization is Bosch. “Through networked production, the Bosch Group expects to achieve cost savings of around one billion euros and additional sales of one billion euros by 2020)”.
In one of their factories, one multi-product line “can now produce up to 200 different hydraulic modules from 2,000 parts, with nine stations networked in the line. Via an RFID chip, which is networked with the component-specific data in the system, the chips recognize which work steps are necessary and which components have to be assembled and how. Each section finds its own way through the production line and requests the appropriate materials. This is where trained employees come into play, who are shown a photo or film with the necessary assembly steps for the finished product on an interface.”
Clearly this is advanced factory digitalization and a move to ‘lot sizes of one’ or ‘mass customization’ which is a macrotrend in manufacturing today.
Fanuc, the Japanese robotics manufacturer runs a fully “lights-out” factory, operating since 2001. In this factory, robots build other robots completely independently for almost a month at a time. Not only are the lights off most of the time, but so is the heat and air conditioning.
Clearly, most manufacturing companies will have a long way to go to meet this level of advanced manufacturing, but these two examples demonstrate what your vision for your factory of the future might entail.
So how do you go about envisioning your factory of the future and start to close the gap between what IIoT technology makes possible and what you’re actually applying in your factory?
Going back to the CB Insights article mentioned above, we list 8 areas where you might explore and ideate to shape your own future.
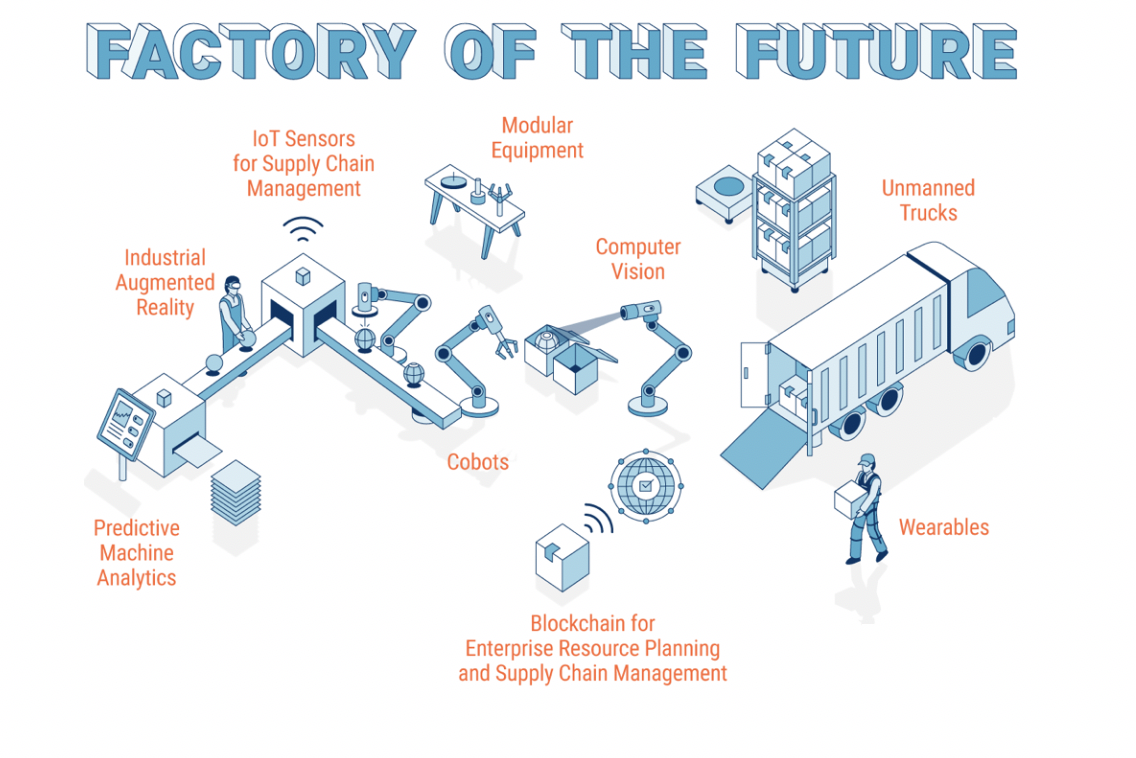
Image Courtesy CB Insights
1. R&D
Companies are using advanced multi-physics engineering programs to conceive, develop and troubleshoot products before detailed design even begins. ‘Multi-physics’ means that you can build a representation of a physical object, like you would in any 3D CAD system, but once the object model is made, you can then simulate behavior and failure points. A multi-physics engineering program allows you to embed material properties in the object and place it under loads to see what deflections look like and physical failure might entail. You can simulate the same object using CFD (Computational Fluid Dynamics) modeling to simulate gas or liquid flow through or around the object, simulate combustion, calculate heat transfer and more. What used to take months or even years of physical simulation using load testing equipment, wind tunnels and cold and hot chambers can now be compressed to weeks or even days. Products and components exit the conceptualization and design stage far closer to the end product than ever.
Between product conceptualization and model building, companies are using massive materials databases developed by 3rd parties to source material specifications. VR Goggles allow manipulation of 3D component and assembly models to simulate manufacturing and verify product design.
“One company working in chemistry and materials science is Citrine Informatics (below, left). Citrine runs AI on its massive materials database, and claims it helps organizations hit R&D and manufacturing milestones 50% of the time. In 2018, Citrine raised $8M from Tencent to aid its international expansion — the next year, it announced a partnership with LANXESS to work on the use of AI for plastics production. Similarly, Deepchem (right) develops a Python library for applying deep learning to chemistry.”
3D printing then allows for the quick production of factory realistic components for refinement and fit testing in the real world. According to CB Insights, “accelerating product development is the #1 priority for firms using 3D printing”.
2. ERP
Lean Manufacturing has shorn many manufacturing value chains of waste with many manufacturing systems utilizing parts nearly as fast as they arrive at the factory gate. Honda famously has a factory that holds only one hour’s worth of parts.
However, it may yet be possible with factory digitalization to further compress inventories. In decentralized manufacturing, companies are building a web of geographically dispersed mini-factories that produce components and materials on demand, radically shortening logistics distances. Very small run items, particularly those suitable for additive manufacturing, are produced on demand in smaller lot sizes.
“Companies like Xometry and Maketime offer on-demand additive manufacturing and CNC-milling (a subtractive method that carves an object out of a block), fulfilling parts orders across its networks of workshops”.
A technology that you’ve probably heard of is blockchain, but outside of financial services you often don't hear much about it. ERP software tracks materials, resources and labor across an individual company. Block Chain technology holds the promise of distributed ledger ERP systems spanning global value add chains, allowing each manufacturer to manage their own systems and have unprecedented visibility into supply and demand, while having trusted real time data to work with.
“Blockchain and distributed ledger technologies (DLT) projects aim to unite data from a company’s various processes and stakeholders into a universal data structure. Many corporate giants are piloting blockchain projects, often specifically aiming to reduce the complexity and disparities of their siloed databases.”
3. Smart Factory Analytics
Smart Factory Analytics such as Worximity enable the easy provision of real time dashboards across your manufacturing system. Dashboards can be customized to provide just the right information at just the right time depending upon each participants role.
“According to lean manufacturing metrics (measured by overall equipment effectiveness, or OEE), world-class manufacturing sites are working at 85% of their theoretical capacity. Yet the average factory is only at about 60%, meaning there’s vast room for improvement in terms of how activities are streamlined."
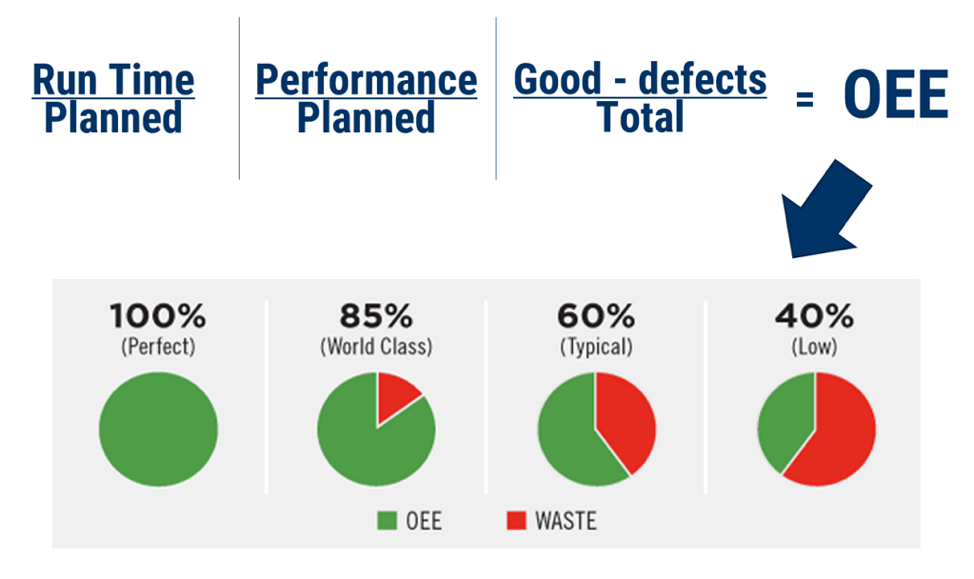
Image Courtesy CB Insights
Smart Factory Analytics software such as Worximity drive waste down while radically improving OEE to help you to reach world-class performance.
4. Labor Augmentation
Multiple IIoT technologies are transforming how manufacturing labor is done. Augmented Reality, or the use of VR goggles enable information to be provided on a just-in-time basis. This technology supports mass-customization by providing work instructions on the fly. It also enables instantaneous training and support for equipment maintenance and repair.
“In addition to being a hands-free “browser” that can communicate factory performance indicators and assign work, AR can analyze complicated machine environments and use computer vision to map out a machine’s parts, like a real-time visual manual. This makes highly skilled labor like field service a “downloadable” skill (in a manner not unlike The Matrix).”
Cobots provide mechanical force multiplication for workers in the form of companion robotics and exoskeletons to reduce injury and fatigue and improve productivity per worker.
5. Production and Assembly
With respect to 3D printing, as noted above, much of the investment focus is on product development. However, for certain applications, additive manufacturing can streamline product assembly operations by producing components on the spot as needed. One-off 3D printed parts enable a vast array of product variations to be produced from one work center.
The addition of robotics to the point of ‘lights out’ is one possible outcome of advancing your factory, but there are still lots of gains to be made by utilizing Smart Factory Analytics to remove waste from your production operations. Advanced automation and autonomous vehicles are one way to potentially take a step towards lights out, but even adding a 7th axis to a traditional 6 axis robot can reduce the labor and time required to shuttle parts to and from workstations.
“Whether these are truly collaborative or rendering human labor redundant remains to be seen. After a Nissan plant in Tennessee added autonomous guided vehicles, no material handlers were laid off with the increased productivity. European aircraft manufacturer Airbus also uses a mobile robot, which works alongside humans to drill thousands of holes into passenger jets.”
6. Quality Assurance
Modern factory digitization efforts such as advanced product simulation can help to bake quality into products. Computer vision is increasingly being used to discern product quality on moving production lines where human speed and the risk of boredom setting in creates issues. Smart Factory Analytics can help to eliminate the production of products that don't meet spec and can help you to ascertain equipment health to meet predictive maintenance goals before products go outside of tolerance.
“Venture-backed startups like Instrumental are training AI to spot manufacturing issues. And famed AI researcher Andrew Ng has a manufacturing-focused startup called Landing.ai that is already working with Foxconn, an electronics contract manufacturer.”
7. Warehousing
The drive to ever-reduced inventory on the balance sheet is one way to lessen warehousing costs. Lights-out warehouses are a natural extension of lights-out manufacturing.
“With the rise of e-commerce, demand for warehouse space has exploded. Last year, the average warehouse ceiling height was up 21% compared to 2001, and spending for new warehouse construction hit a peak in October 2017, with $2.3B spent on construction in that month alone.”
The drive to automate this incredible increase in warehouse space is immense to maximize ROI on these investment. You can see examples of warehouse automation here.
8. Logistics
Trucking ‘telematics’ have been in use for quite some time, using cell or satellite location and communications technology to track and route trucks for the highest level of efficiency and enable supply chain visibility even as deliveries are mobile. Now, autonomous truck fleets are set to disrupt logistics and shake costs even further from product mobility.
Blockchain and IoT technologies are launching to revolutionize ERP systems across companies as noted above, and products in motion are no exception.
“Once the product is packaged and palletized, getting it out the door efficiently is a daunting task. With thousands of SKU numbers and orders to manage, the complexity can be astounding — and enterprise resource planning (ERP) software has proliferated to handle it.
But there’s still room for IoT and blockchain to get even more granular with real-time supply chains.”
Brands
Brands will increasingly tout their reduction of waste not in terms of cost savings (although this will always be important) but in terms of less resources consumed. Leading consumer products companies are embracing the Circular Economy, where products are designed with recycling and reuse in mind. Using factory digitization technologies provides opportunities to reduce geographic footprint, embrace ‘buy local’ beyond food production and can reduce energy costs.
Conclusion
Smart Factory Analytics is proven to be the low hanging fruit for creating your IIoT or factory of the future story. With fast implementations and quick ROI, software such as Worximity snaps right into your continuous improvement programs and accelerates and improves your results as you move more and more lean.
That doesn’t mean that you shouldn’t have your eye on the future of IIoT technologies for manufacturing and think about what your factory of the future looks like!
Interested in starting you factory of the future journey? Reach out and schedule a demo!
What the future holds for factory digitization
Based on future projections, Digitization will only continue to improve and become more reliable in the future. Digitalization and the concept of Industry 4.0 go hand in hand with each other as they both deal with the main goal of increasing efficiency inside companies. industry 4.0 will continue to improve itself and in turn, increase the scope of what digitalization can do and make it a better resource for companies to use. Once there is complete incorporation of these two things into one another, demand will keep on increasing and every factory that wants to remain competitive in the near future will have to incorporate digitalization into their company.
How llot increases productivity
Companies that have implemented llot into their businesses have experienced many forms of productivity rising from workers being able to work more productively to companies being able to produce more products at a better rate. lloT technology has also made the average worker be more receptive to being able to handle more complex tasks at hand and be more capable of handling more responsibilities that now 1 person can do compared to 4 people that were needed at hand for the same task.
How llot is connecting workers around businesses
LloT technologies also connect and empower workers by giving them more responsibilities and being able to work concurrently with the technology that is implemented in a lloT Setting. This works by maybe that because of lloT making complex processes simpler, an ordinary factory worker who may have needed to have more experience could take on the task at hand with lloT technology helping them complete the process. The worker would then become more intelligent and be capable of handling more tasks than what was originally thought the worker could handle by himself.
How lloT technology is putting customer satisfaction at its forefront
One of lloT technology’s focus and drive to improve customer satisfaction stems from the fact that lloT takes into consideration the whole process as a whole and looks for ways to improve it to make it more efficient. One of the main ways customer satisfaction is taken into consideration is the analyzation of the results being that the results are analyzed to record how the general population of the seller’s perspective would react and applying necessary changes if needed. everyone from the owners to the buyers of said resource will be studied and analyzed to make sure that quality is met on both sides to ensure continued business. If the results are poor, lloT will be able to recognize this and apply the correct methods to ensure that this negative outlook is changed.
The future of lloT Technology
LloT Technology has seen the rise of popularity and experts believe it is not slowing down. The market cap has dramatically changed over the years from professionals predicting a max cap in the millions in 2011 to now currently having a cap in the Billions. The results have spoken for themselves and paint a picture that companies are becoming more and more in favor of implementing lloT. The main driver is the implementation within businesses to make sure that companies are kept ahead of the curve and stay competitive in this day and global economic environment.
https://www.cbinsights.com/research/future-factory-manufacturing-tech-trends/
https://www.lead-innovation.com/english-blog/digital-factory
https://www.mapi.net/blog/2018/06/using-digitalization-make-manufacturing-competitive-weapon
https://blogs.oracle.com/scm/the-digital-future-of-manufacturing
https://www.ge.com/digital/blog/everything-you-need-know-about-industrial-internet-things