When traditional manufacturing processes are used, when one part of the manufacturing phase is completed there is usually a waiting period before the next phase can be continued. With Lean Manufacturing the waiting time (Waiting Waste) for a product is narrowed down to a much shorter period of time or eliminated completely.
With more careful planning and coordination it’s possible to get a quick return on investment from your manufacturing operation.
In Lean Manufacturing, Waiting Waste is inventory that is sitting idle, whether it’s between manufacturing stations or end product waiting on shelves or in warehouses waiting to be demanded. Waiting Waste ties up significant capital in many businesses and the cost of capital drives up costs throughout the organization. When product is sitting, no value is being produced.
Types of Waiting Waste include:
- parts or assemblies waiting in queues for the next step in the operation
- people waiting for material, equipment or tools to perform their operation
- finished products waiting to be shipped or sitting in stores
- idle equipment
Waiting Waste is an indicator of uneven production. As we noted in Part 1 of this series, but setting up a ‘pull’ manufacturing system from the end customer back, manufacturing processes can be adjusted to eliminate waste, including waiting waste, throughout the system.
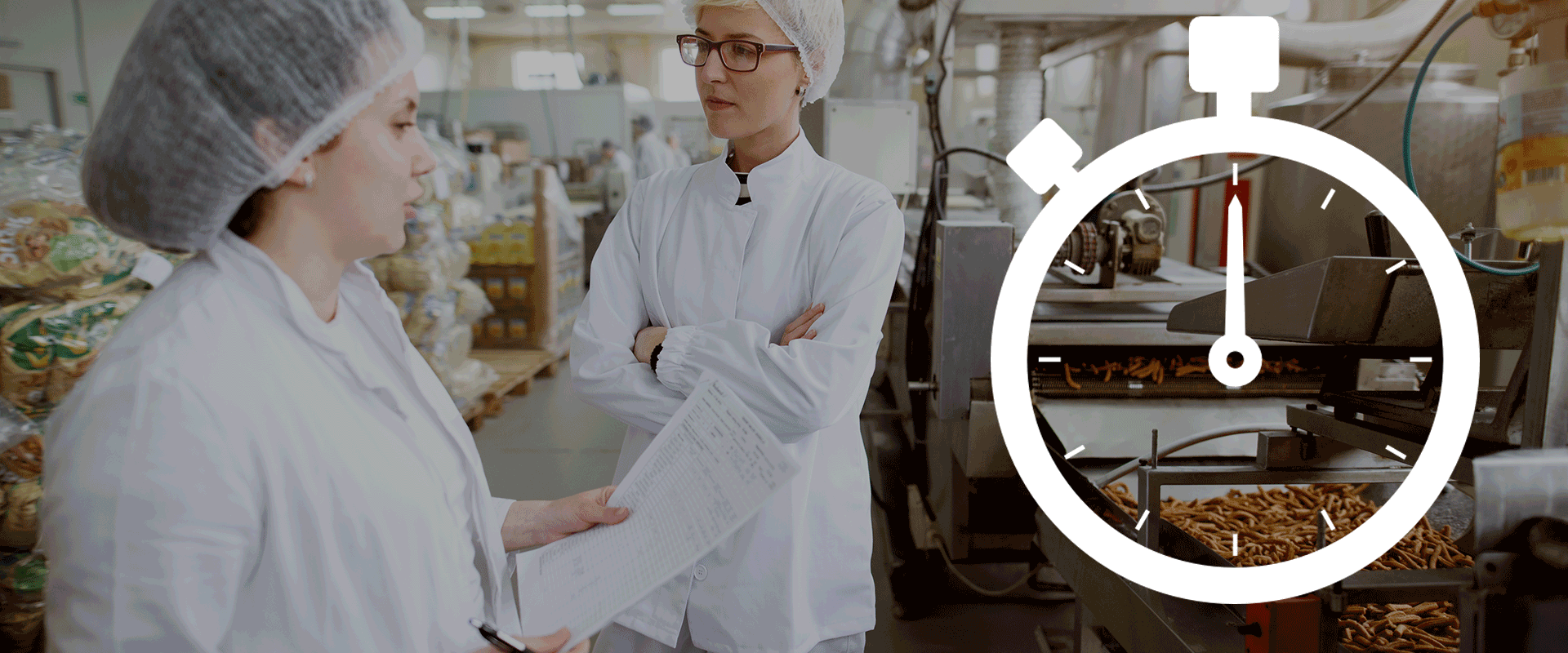
Typical causes of Waiting Waste include:
- unplanned downtime
- production bottlenecks and not balanced production workloads
- setup times that are too long
- producing to a forecast instead of a pull system
- not enough people
- people out unexpectedly
- poor quality built into the process
- ineffective internal communication
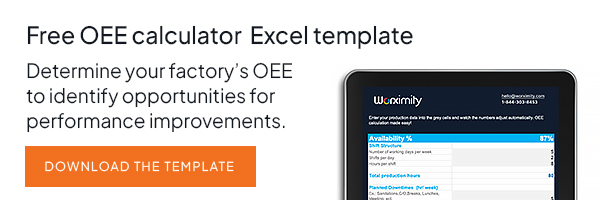
Steps that Lean Consultants recommend to reduce or eliminate Waiting Waste include:
- redesigning processes to ensure even production flow or even single piece flow in response to the manufacturing process ‘pull’
- standardizing instructions, training and processes
- developing multi-skilled / flexible human resources so that people can respond quickly and be re-tasked to other areas as demand changes
It is sometimes the case that managers believe they are saving costs by minimizing payroll but when a closer analysis is done, hidden costs such as waiting waste are actually more costly than having properly staffed production systems.
"Like with Overproduction Waste, Waiting Waste doesn’t just happen on the manufacturing floor, but can happen in the office areas as well. Simple things like email response times or waiting for information in order to make adjustments to the business are waiting waste as well. Office waiting waste can spill over into manufacturing waiting waste as equipment capacity can’t be managed well with poor or untimely information."
An example of using Smart Factory Analytics to reduce waiting waste is Viau Foods who improved his yield, reducing the amount of waste meat from 500 kg to 50kg daily.
The eight wastes of lean manufacturing can be remembered with the acronym DOWNTIME:
Read Types of Waste in Lean Manufacturing - Part 4 - Non-Utilization Waste
Download our Free Lean Manufacturing Industry 4.0. to understand how technology can help you reduce your waste.