You’ve seen major improvements in quality with your Lean and Six Sigma programs. Why mess with what’s working and cause disruption with Industry 4.0
That’s a common question I hear from manufacturers, and luckily there’s a good answer. Industry 4.0 does not have to completely reinvent everything in your process. In fact, we recommend starting with your current KPIs and implementing a monitoring solution that gives you better data about those KPIs.
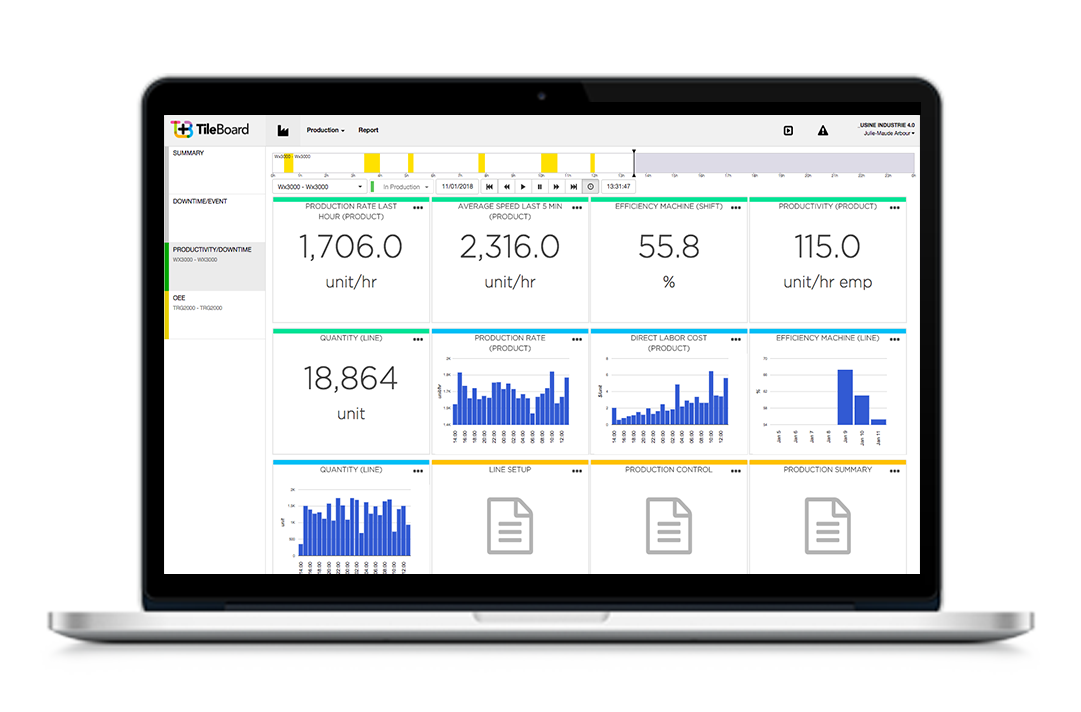
Real-time, easy-to-read KPIs support continuous improvement
Another assumption I run across is that Industry 4.0 is so technically complex, it requires complete retraining for everyone involved. This isn’t true. Yes, you will need technical people involved for the implementation, but if you’ve selected the right solution, connectivity will eliminate technical barriers, not add them.
Here’s an example of what I mean: Right now, if your managers and operators want to know how a line is performing against average KPIs, can they find that information in seconds? Or, would they have to do some manual monitoring or request that someone in IT manually run a special report? With a monitoring system that displays KPI information on color-coded display boards in easy-to-read charts and graphs, operators and others on the plant floor know the real-time status of all KPIs displayed. That same information can also be sent to managers’ smartphones – technology they’re already comfortable using. Yes, there is some technical complexity involved with configuring sensors and controllers, but a basic monitoring solution can be set up in hours.
FIND OUT HOW A SMART BAKER GAINS 27% IN RESPONSIVENESS IN CASE OF DOWNTIME
Aggregate data can increase quality for internal customers
Do you know how much time your production cells spend waiting for the previous or next operation? What if you had visibility on the top 5 bottlenecks and the amount of wait time each one caused in the course of an average cycle or per week? Would you be better equipped to take corrective action? Monitoring solutions implemented as part of an Industry 4.0 solution can illuminate problem areas that were difficult to identify without data being captured automatically. Small pauses may seem like a non-issue or simply part of the usual routine to an operator, but when the numbers are added up, they can reveal a bigger problem that needs resolving to help the entire production line operate more efficiently.
Use Industry 4.0 to increase value to the end customer
Think of Industry 4.0 as connection and communication. By connecting the factory floor to management, you’ll have higher quality, current data to use for strategic decision-making. For example, with more data you’ll be able to decide when, how, and if it makes sense to add more low-volume high-mix products to your offering. Would customized products be a competitive advantage if you could produce them more cost-effectively? Would you gain market share with a more diverse product offering and the ability to react faster to market demands? Could you achieve more success with short-run products that support specific market initiatives? By gathering and analyzing real-time plant floor data, you can go beyond estimates to finding solutions that support your goal of customer satisfaction and engagement.
To learn more about KPI monitoring and displays see Real-Time dashboard