What exactly does a smart manufacturing facility look like? If you walked into a smart factory—one uses IIoT; that leverages data collection and analytics, performance, machine and downtime monitoring, overall equipment effectiveness and giveaway, and other related technologies—you may not be able to note anything extraordinarily different before your eyes.
But, in a paper for Hitachi Consulting, authors Greg Kinsey (Vice President, Industrial Solutions & Innovation, Hitachi Vantara) and Mark Nott (Vice President Global Solutions & Innovation, Hitachi Consulting,) they note, "once you started talking to people, you would understand the dramatic contrast between a digital manufacturing environment and a traditional one. In the smart factory, people would feel they have more knowledge at their disposal about operations. They’d be in better control of their processes, and they’d know what’s coming—predicting what might happen based on data and analytics.”
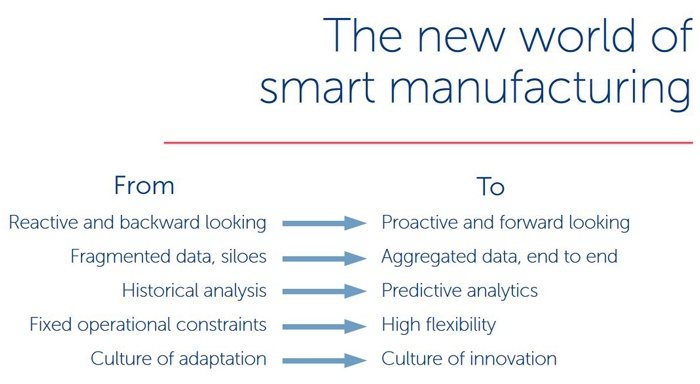
Image: Hitachi Consulting
And how does this really effect the bottom line or quality? “If you looked at the key performance indicators (KPIs) for the smart factory, you’d notice it has a higher quality level, more efficiency, increased throughput, fewer bottlenecks and more flexibility. It responds more easily to smaller lot sizes, variable customer requirements and changing conditions. Hot weather coming in? The smart factory has a weather forecast built into its algorithms, and it knows when to readjust processes to compensate for the heat.”
Kinsey and Nott write, “A smart factory with these capabilities is the goal of every manufacturing executive on the planet.” The question, they ask is, how can you get there?
Here are three ways smart manufacturing creates business value
1. Predicting and preventing downtime: Reducing the number of products that are out of sync with Takt time, increasing capacity and throughput, and reducing maintenance costs.
2. Predicting and preventing bottlenecks: Having materials arrive at the right time with each station working at full capacity, increasing throughput.
3. Predicting and preventing defects: Reducing cost of poor quality (CoPQ) and enabling better product mix.
Source + read the complete report.