The IIoT (Industrial Internet of Things) is a subset of the IoT (Internet of Things). IoT technologies include any non-consumer devices (such as phones and laptops) that are connected to the internet. Devices might be connected to the internet for the purposes of gathering and communicating data such as through sensors or cameras (the Ring doorbell is an example) or for providing remote control capabilities (such as the Nest thermostat device).
IoT, or ‘connected devices’ is a rapidly growing space, with global technology spend on IoT technologies expected to reach $1.2 Trillion by 2022.
IIoT technologies are IoT solutions that are applied in an industrial setting. This can include sensors and devices that are incorporated into industrial products themselves, such as for monitoring equipment health like aerospace turbine engines. It can also include technologies used for optimizing and improving the manufacturing operations that produce products.
A recent study of IIoT trends showed a significant shift in the topics companies were consuming from 2018 through 2019. While in 2018 topics of interest included sensors, virtual reality and 3D printing, over the course of 2019 as we approach 2020, the top topics evolved to include Cobots, Digital Twins and Predictive Maintenance.
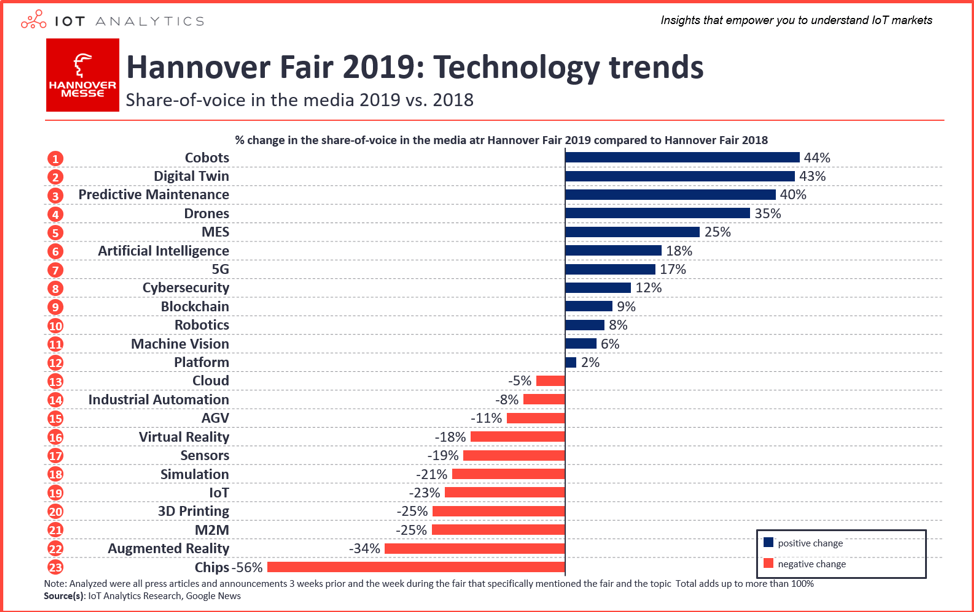
Moving towards 2020, the top 3 IIoT topics are Cobots, Digital Twins and Predictive Maintenance
Cobots
The days of 6 Axis robots operating independently behind safety cages may be coming to an end. Robots are becoming more mobile and collaborative. Mobile robots are being fitted with perimeter sensor technologies that are monitoring their surroundings so that they can work in close proximity to people while maintaining a safe environment. Some companies are going farther, testing wearable robot systems where an exoskeleton provides lifting strength beyond what a person is capable of while mimicking the intelligence and fine motor control of a human being.
The global cobots market size crossed $649 Million in 2018 and is expected to expand at a CAGR of 44.5 % between 2019 and 2025.
Digital Twins
Companies that design and develop high value industrial products are investing in digital twin technologies. They are embedding sensors into their products to measure important machinery health attributes such as localized temperatures, power input and output parameters and more. This enables the creation of ‘digital twins’.
A digital twin is a software-based engineering model of a real-world piece of equipment. The data collected from the sensors from the real-world machine is sent to the digital twin model and the model simulates the health of the machine.
This can help to manage operational costs by deciding when the equipment should be removed from service for routine maintenance such as an oil change. It can also be integrated with other data such as equipment vibration signatures to predict critical component failure. This can minimize consequential outcomes from premature failure and operational risk such as the resulting injuries or simply avoid the costs of repairing catastrophically failed equipment.
Gartner claims that 24 percent of enterprises are using digital twins and an additional 42 percent intend to invest in digital twin technology. Early adopters include large logistics businesses that are monitoring heavy trucks and locomotives. More famous examples include monitoring and modeling aircraft engines.
Related to Digital Twins is Predictive Maintenance
Digital Twins are one way to get to predictive maintenance capabilities but are by no means the only IIoT technology that can be used to predict machinery maintenance requirements.
Downtime is a significant cost-driver for manufacturing businesses and unplanned downtime can cost businesses dearly. Unplanned downtime compounds the cost of solving whatever brought the downtime about. Planned downtime can cost businesses money, however unplanned downtime brings with it all of the additional costs of paying for an idle workforce and having to replace lost production through overtime or subcontracting. There's also the impact on relationships with customers for missed deliveries.
The ability to move every equipment outage to be a planned event where parts are on hand and service resources are ready to step in and the impacts on production are mitigated presents a significant cost-savings opportunity for manufacturers.
While each of the three IIoT technologies outlined above will have a place in manufacturing optimization, they are largely the province of enterprise businesses. That doesn’t mean that small to mid-sized manufacturing businesses are left out of the IIoT revolution however.
From our article Industry 4.0 and Efficiency - A Global Perspective, we discovered that with respect to IIoT investments and ROI, “largely though, the ROI is being driven by higher efficiencies and the resulting cost savings..." rather than more complex reasons.
In other words, while cool futuristic IIoT implementations such as Cobots and Digital Twins may steal the headlines, the big gains will be made in implementing solutions that lower costs and deliver fast ROI such as Smart Factory Analytics.
Every manufacturing business can take advantage of these IIoT potentials:
Inventory Management
Using technologies such as RFID tags, manufacturers can manage inventory quantities and identify exactly where in a manufacturing process parts, assemblies and finished products are. IIoT inventory management solutions can drive Just in Time programs farther than paper and pencil ever could.
Production Management
Using Smart Factory Analytics technologies (such as Worximity!) companies can monitor production machinery directly, responding to upset and outage conditions more quickly and building a behavioral history over time that can drive better and faster results from continuous improvement initiatives. Smart Factory Analytics can even provide predictive maintenance capabilities without the expense of building complex digital twin models.
For additional strategic IIoT perspectives, read our articles below:
Strategic Roadmap for IIoT Success
Industry 4.0 and Efficiency - A Global Perspective
Empowering the C-Level Executives in Food Manufacturing with Real Time Business Intelligence
OEE & Smart Factory Analytics - The Game Changer for Manufacturers
Interested in learning more about what it takes to implement your own Smart Factory Analytics solution? Book a demo below!