In addition to the types of Wastes identified in Lean Manufacturing, 5 approaches are identified to combat these wastes.
The 5 S's of Lean Manufacturing are:
- Seiri (Sorting)
- By eliminating all unnecessary steps of the manufacturing process the amount of waste produced will be decreased and efficiency will be increased. Sorting through all unnecessary tools, part and instruction is an important first step to take that will help to achieve the end goal. By prioritizing items that help to streamline the manufacturing process and making them readily available, lean production is closer to being achieved.
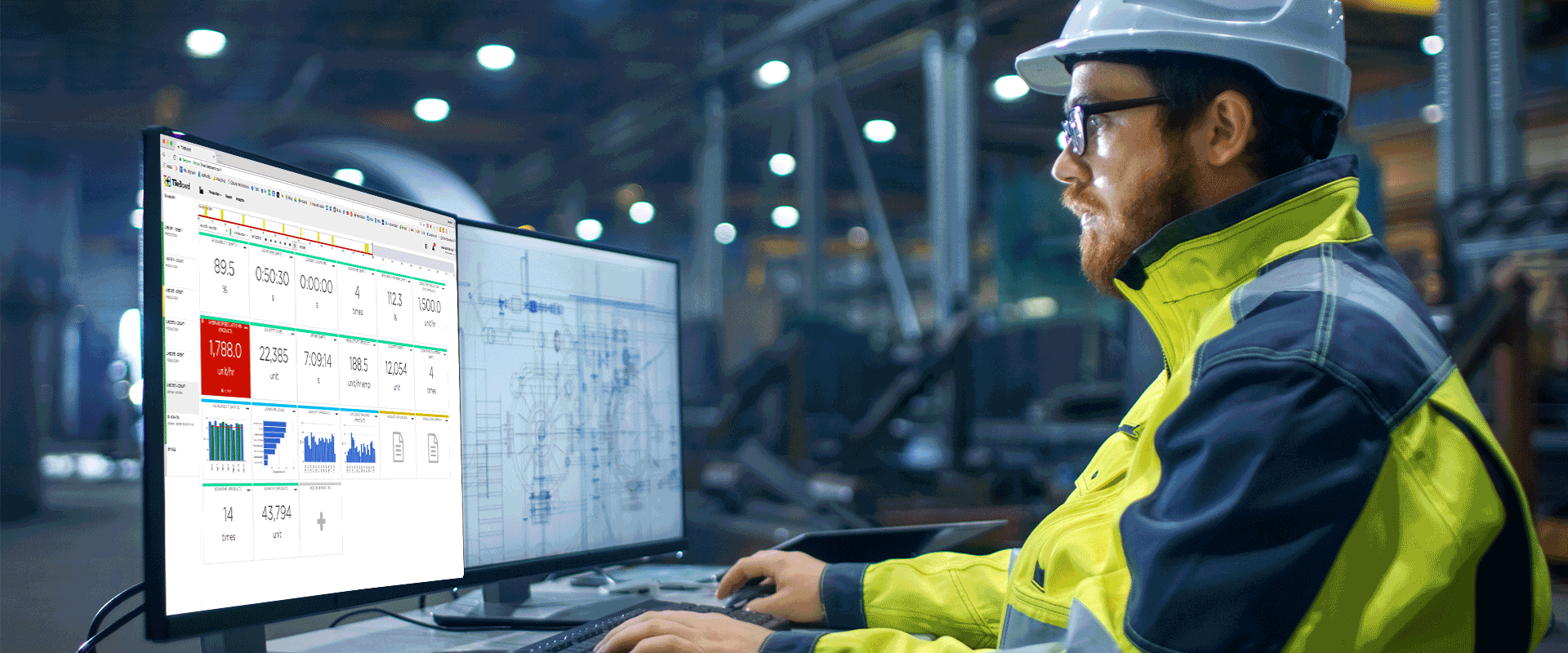
- Seiton (Straightening)
- Once items have been sorted and deemed necessary or unnecessary, each item that will be used in the manufacturing process will need a specific storage location that is clearly labeled. By assigning each item a specific space they can be arranged in order of use, so that when Lean Manufacturing begins the workflow can be improved, leading to less waste and maximum efficiency.
- Seiso (System Checking/Cleaning)
- Once steps one and two are completed the employees at a manufacturing site can focus on the actual machinery that is used to create the end product. Maintaining the equipment is a vital part of the manufacturing process because equipment that is neglected is more likely to break down, leading to waste. If equipment is cleaned at the end of each production day or on a regular schedule, then the likelihood of it malfunctioning is decreased. By regularly cleaning equipment employees will also be able to identify any irregularities that could lead to a breakdown of equipment.
- Seiketsu (Standardizing)
- All workstations in a manufacturing system that perform the same job must be organized in the same way to create flow and ease of understanding for employees. When this is achieved employees can also be easily moved around and continue their job at a different stage of the manufacturing process with the same level of efficiency. By standardizing methods of production, a repetitive process will become apparent to employees, which will lead to increased efficiency on the job.
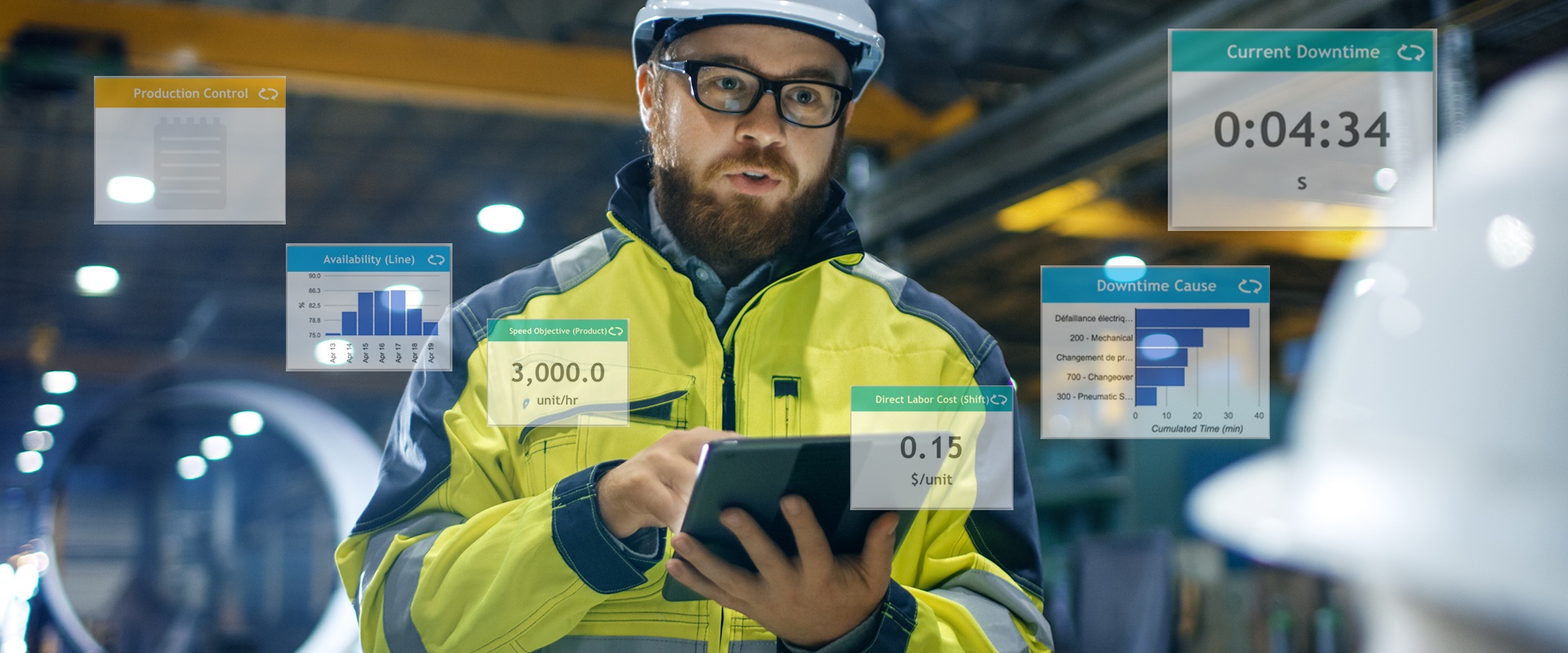
- Shituske (Sustaining)
- Once the preceding four steps have been taken in a manufacturing system, the system is closer to achieving a lean method of production. It is easy for a manufacturing system to revert to old ways that may seem easier, but actually create more waste and less efficiency. When the focus is placed on sustaining the previous four steps then a manufacturing system will see overall increased improvement. Managers and employees alike must work together in order to figure out how they can help each other sustain the previous steps as well.