When Lean Manufacturing approaches the issue of motion it is not related to the physical movement of products that are used to create the end result (Transport Waste), but rather the people or equipment that are used to create physical products.
Motion Wasted in lean manufacturing is the increased motion of machinery or a person due to an inefficient manufacturing process. Wasted motion increases the amount of wear and tear on both workers and machinery, therefore decreasing its lifespan or ability to work on at a manufacturing site. Not only does wasted motion cost money, it can also lead to unnecessary accidents and injuries.
Motion Waste can be caused by:
- Inefficient floor layouts
- Improper equipment
- Poor allocation of tasks between machinery, people or steps in a process
With Lean Manufacturing the amount of motion is kept at a minimum due to the well thought out and carefully planned timeline and pre-fabricated parts. When motion happens, there is no value being produced on a product or material.
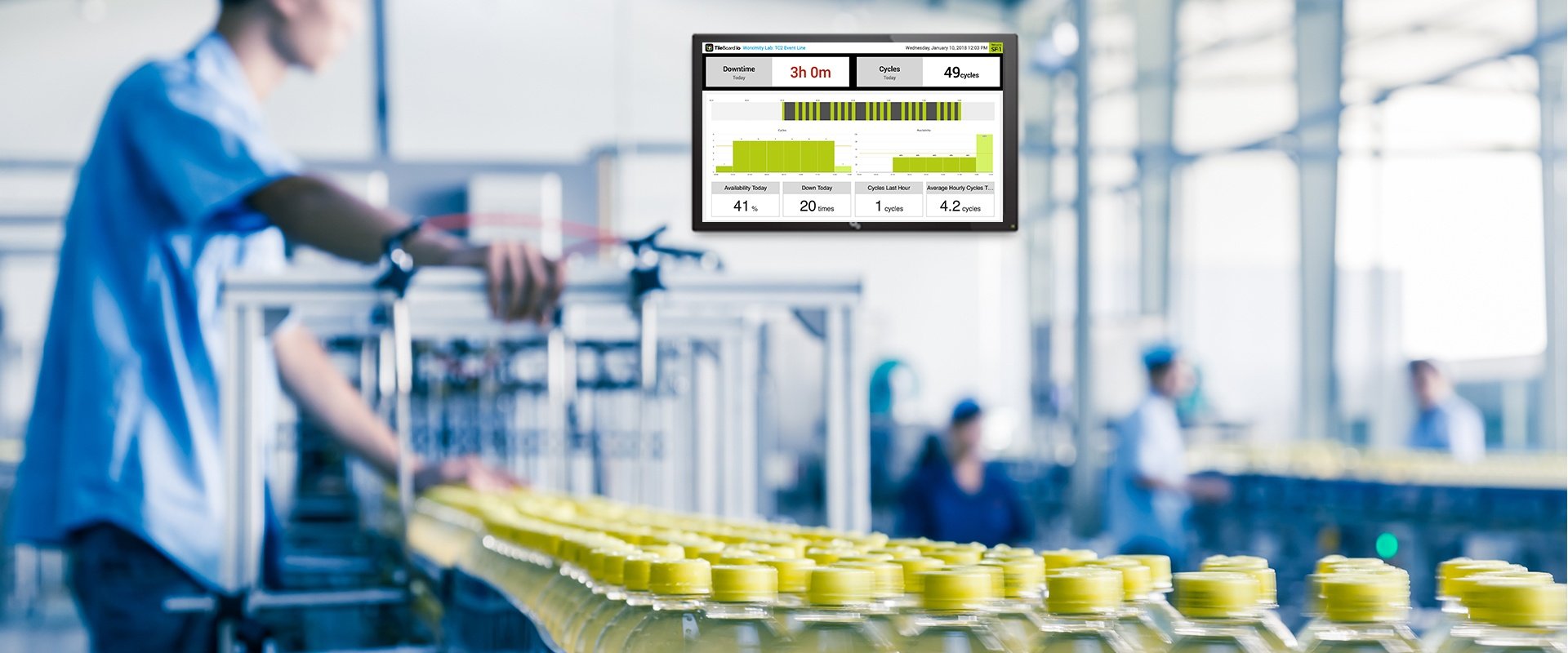
Motion Waste can often be categorized and measured by looking at activities such:
- walking
- reaching
- lifting
- lowering
- bending
- stretching
- or otherwise unnecessary moving, such as traveling to other facilities when other forms of meetings would do
"Having a real-time dashboard available on tablet, on mobile, on tv monitor in the factory or on a dektop computer in executive office can significantly reduce Motion Waste and improve collaboration.." - Adrian Evi, ing.
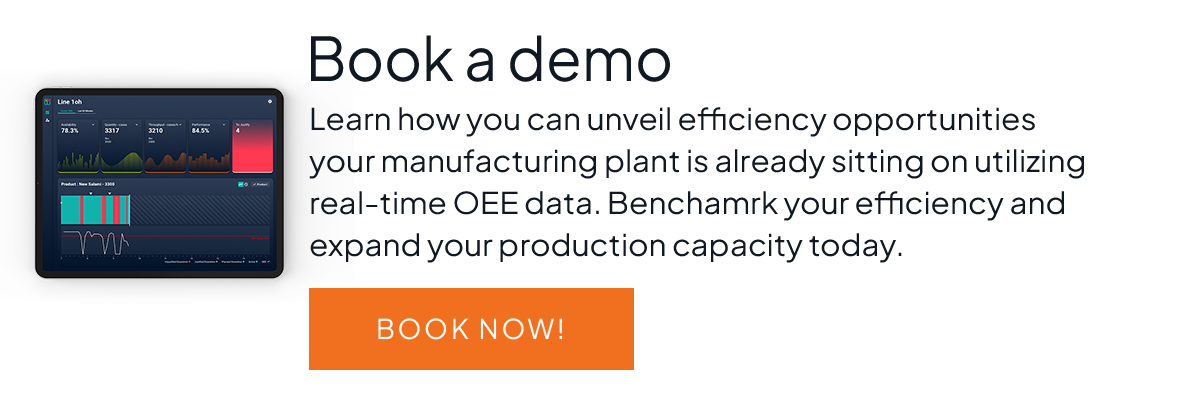
The eight wastes of lean manufacturing can be remembered with the acronym DOWNTIME:
Read Types of Waste in Lean Manufacturing - Part 8 - Overprocessing Waste
Download our Free Lean Manufacturing Industry 4.0. to understand how technology can help you reduce your waste.