The IoT (Internet of Things) is a rapidly growing technology space, with consumer, security and industrial connected devices projected to increase to 43 billion by 2023, an almost threefold increase from 2018, according to Mckinsey & Company. The IIoT, or Industrial Internet of Things is a subset of the IoT market and is transforming the manufacturing industry. It is changing the way in which manufacturers collect and process information, how machines interact with each other, and how workers use tools and operate machinery. IIoT technology provides companies and manufacturers with multiple benefits and advantages over their competitors and therefore it is a big and important topic in today’s manufacturing world.
Each day, more manufacturers invest in IIoT technology, and according to Forbes magazine, “global spending on IIoT Platforms for Manufacturing is predicted to grow from $1.67B in 2018 to $12.44B in 2024, attaining a 40% compound annual growth rate (CAGR) in seven years” and in fact “manufacturing is the largest IoT platform industry segment and will continue to be one of the primary growth catalysts of the market through 2024”.
IIoT technology enables the collection of data through distributed sensors in real-time. IIoT technology is thus able to provide a competitive advantage for manufacturers looking to improve their operations thanks to its' capability to continuously collect and present for analysis critical manufacturing data and trends. Data are ‘collected facts and statistics’ and ‘the basis for reasoning and calculations’, so having access to real-time manufacturing data is the root to creating many solutions in manufacturing.
According to the Forbes article above, factory-based IIoT solutions are replacing traditional MES systems in many factory settings. MES, or Manufacturing Execution Systems are software that are used by manufacturers to plan and manage complex manufacturing systems.
The functions of a modern MES include:
- Data collection and acquisition
- Scheduling
- Staff and resource management
- Process management
- Performance analysis
- Document management
Companies are learning that traditional manufacturing management software, such as an MES platform, that relies on humans to input data cannot keep pace with a modern manufacturing environment. Every input by a person has a cost, whether that be a labor cost, a lost production cost or an accuracy cost. By connecting software directly to sensors that measure production parameters (temperature, pressure, speed, off / on states etc.), machinery outputs and RFID chips, highly accurate (trusted) data can be collected and analyzed in real-time, and also collected for trend analysis.
These datasets however, can be very large and complex, and therefore difficult to use or understand. This is where manufacturing IoT analytics come into play; to allow manufacturers to own and understand the proliferation of data being collected.
The answer to how manufacturing IoT analytics helps manufacturers in processing their data is in the visibility it offers up and down the management heirarchy. In the case of Worximity, IoT devices pull relevant data about machine operating parameters, such as run time, operating speed, product output, etc. The data is gathered in real-time and sent to a SaaS environment for processing. Manufacturing focused SaaS software like Worximity Tileboard is capable of aggregating the data, parsing it and transforming it into the form of dashboards. These dashboards typically present important manufacturing analytics, that are delivered to factory workers, managers and senior manufacturing leadership through different user-friendly interfaces containing graphical and numerical readouts.
Because of this capability, IoT and IoT analytics are of significant interest to a wide variety of stakeholders in the manufacturing business or enterprise, because dashboards can be created to suit the needs of any manufacturing stakeholder role, including Operations Managers, Continuous Improvement Managers and more.
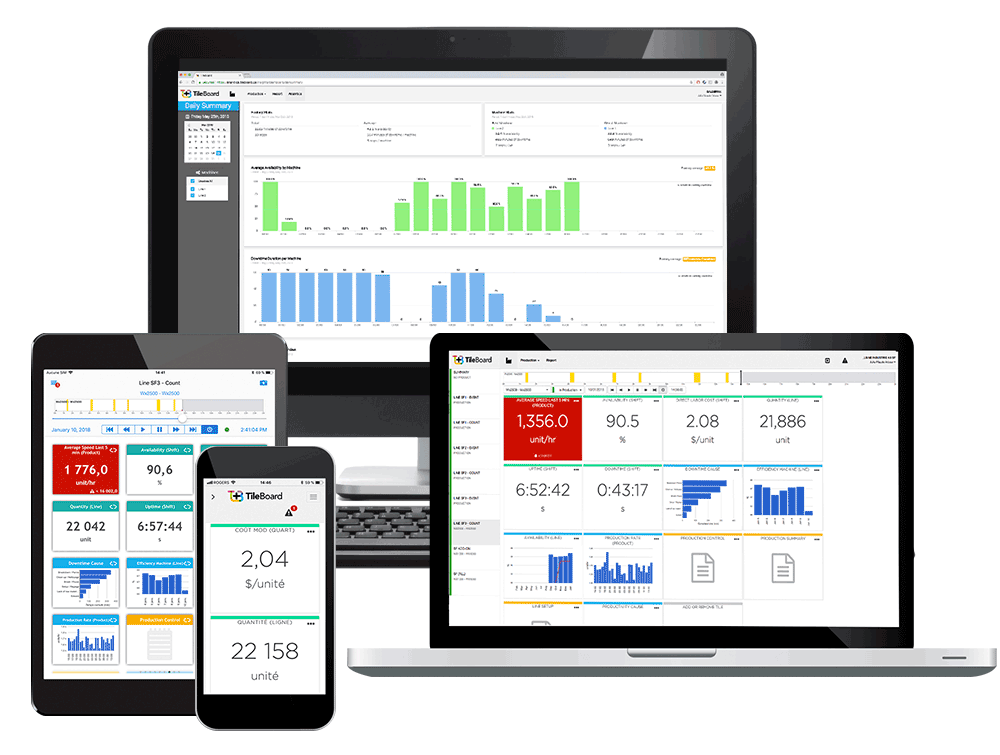
Example of Manufacturing IoT Analytics Dashboard
Workers, managers, and executives can then derive insights from real-time and historical data on analytics presented in dashboards and graphs that are easy to read and to understand.
IoT Analytics for the Factory Floor
Displaying analytics on the manufacturing shop floor has a lot of benefits that ultimately help in improving manufacturing performance. It allows front line workers to have a better understanding of their tasks and the desired goals. It unites workers and allows them to have a better communication between themselves and with executives as everyone has access to the data.
IoT Analytics for Continuous Improvement Managers Practitioners
For Continuous Improvement Practitioners and Managers, having access to real-time and trending data to evaluate the testing of production modifications associated with a suggested process improvement improves decision quality and compresses decision-making cycles.
Manufacturing IoT Analytics for CXOs and Senior Leadership
Having real-time business insights into manufacturing performance lets senior executives gain visibility into how improvement efforts are going, begin to ‘see into the future’ so that they can manage investor or owner expectations better, and quite frankly can reduce the anxiety of not knowing how things are going until final numbers are produced and need to be reported.
Manufacturing IoT Analytics dashboards improve company internal communications, increase transparency and accountability and empower decentralized decision-making in ways that were previously not possible.
There are multiple manufacturing KPIs that IoT analytics can keep track of, and that will help manufacturers in improving their operations’ performance.
The Most Common Manufacturing IoT Analytics Metrics Are:
- Overall Equipment Performance or OEE: one of the most insightful tools of lean manufacturing, OEE takes into account three different metrics: availability, quality, and performance and combine them into a single metric to tell how effective production plant machinery is performing.
- Throughput: considered the most important manufacturing metric, throughput measures the average number of units being produced on a machine, line, unit or plant over a specified period of time. Reported lower throughput means there are issues on the production line, allowing workers to look out for disruptions or bottlenecks.
- Downtime: downtime is a vital metric to monitor. A high number of downtime events means less throughput and loss of profits, which explains why IoT technologies give alerts when any halts in production occurs. For operations managers, keeping track of downtimes and ending them as fast as they can is on top of their list in order to increase productivity and throughput.
Several Ways Which Manufacturing IoT Analytics Benefits Businesses:
- Better Insights: thanks to active data collection and visualization, operations managers can monitor different assets, analyze multiple metrics at once and gain insight into processes’ performance and improvement opportunities.
- Big Data: with IoT analytics across the enterprise, CFOs and financial analysts can more accurately forecast operating results and reveal previously invisible big data trends.
- Streamlined Management: manufacturing IoT analytics dashboards can help to transform reporting from static paper-based or spreadsheet based data that is rarely used into dynamic and interactive insights that can power the future of the business.
- Quality Levels: thanks to cloud storage and IoT analytics, the business can now track WIP (Work in Process) and finalized products’ multiple measurements and characteristics from anywhere. This thorough and accessible information allows managers to perform root-cause analyses much easier than ever before.
- Maintenance: Machinery performance can be analyzed and predictive maintenance methods can be developed, which reduces risks of downtimes.
- Inventory Management: with real-time data IoT analytics, inventory levels can be successfully tracked and forecasted as production is occurring. These technologies reduce variability and errors in the movement of materials and give higher control over inventory. This can significantly lower inventory costs and contribute towards lean operations.
- Supply Chain: sensors that track materials and products when in the hands of suppliers, when going through production lines and when being shipped to customers allow operations managers to cooperate better with third parties and make important strategic decisions ahead of time. Also, slowdown of materials throughout value add processes can allow for bottleneck identification, which can result in bottleneck elimination and higher capacity and productivity.
- Internal Communications: a centralized platform that allows for easy data visualization will also permit operations managers to deliver information to superiors and front-line workers as fast and efficiently as possible. User-friendly IoT analytics software permits all parties involved to visualize and understand issues together. This connection to upper-management and access to performance dashboards can empower workers to ‘do their work right’ and cooperate more.
So, with manufacturing IoT analytics, KPIs such as the ones mentioned above are accessible in real-time while information is stored throughout time as well for trend analysis. This is where IoT analytics help manufacturers improve manufacturing performance. Workers, managers and executives can identify problems or dips in productivity as they happen and solve them much faster than without the ability to instantly visualize them. They are able to identify trends, such as in downtime or availability, and come up with strategies to improve on these metrics. All in all, manufacturing IoT analytics engage workers and senior management and allows them to optimize processes.
Interested in IIoT technology and the implementation of IoT analytics in your factory? Schedule a Discovery Call with a Worximity Consultant!