Since the 1980’s the food industry has faced increased competition from stores that stock their own labeled brands. Many times these products are created at a third party manufacturing site that specializes in that particular variety of food and creates it on a smaller scale, yet less expensive due to the lean methods that these subcontractor manufacturing facilities utilize.
The Lean Manufacturing method can be applied to the food industry in an effort to eliminate waste throughout the manufacturing process and maximize efficiency. Doing so would create greater profits and a higher level of satisfaction for the end customer. A range of lean methods such as, Value Stream Mapping (VSM) and the Just-In-Time (JIT) can be used in the food manufacturing industry to help improve production rates and efficiency. Due to the high turnover rates that are associated with raw materials and the set date that raw materials must be used by, they are some of the costliest and wasted items in the food manufacturing industry.
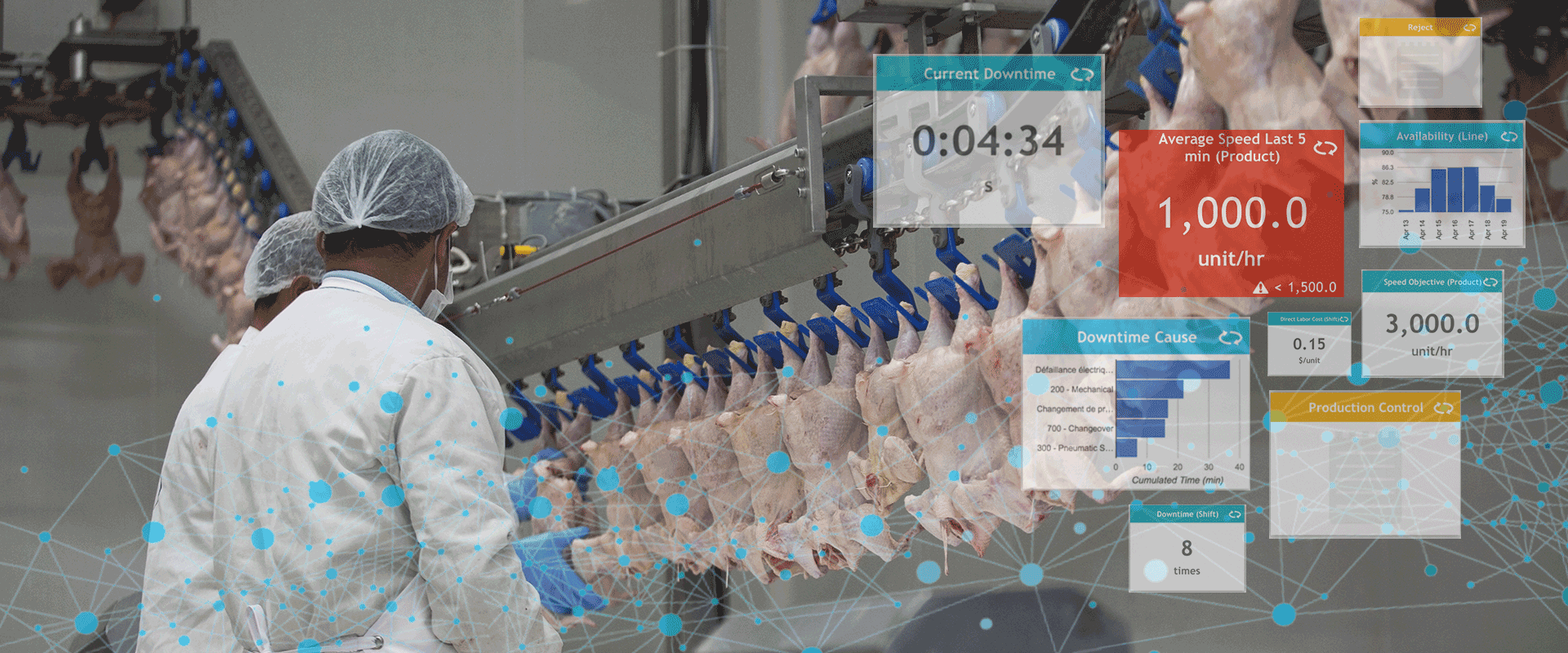
The solution that lean manufacturing in the food industry helped to create was that food manufacturing facilities needed a holding tank for the product so that could be stored for a certain amount of time until orders needed to be fulfilled. Once an order comes in, the product can be withdrawn from the holding tank and packaged, which usually is a relatively quick process. This method of production is called the Just-In-Time (JIT) method of production, it creates a pull system where once the end customer orders a product the manufacturer immediately produces the end product so that they hold less inventory and do not overproduce.
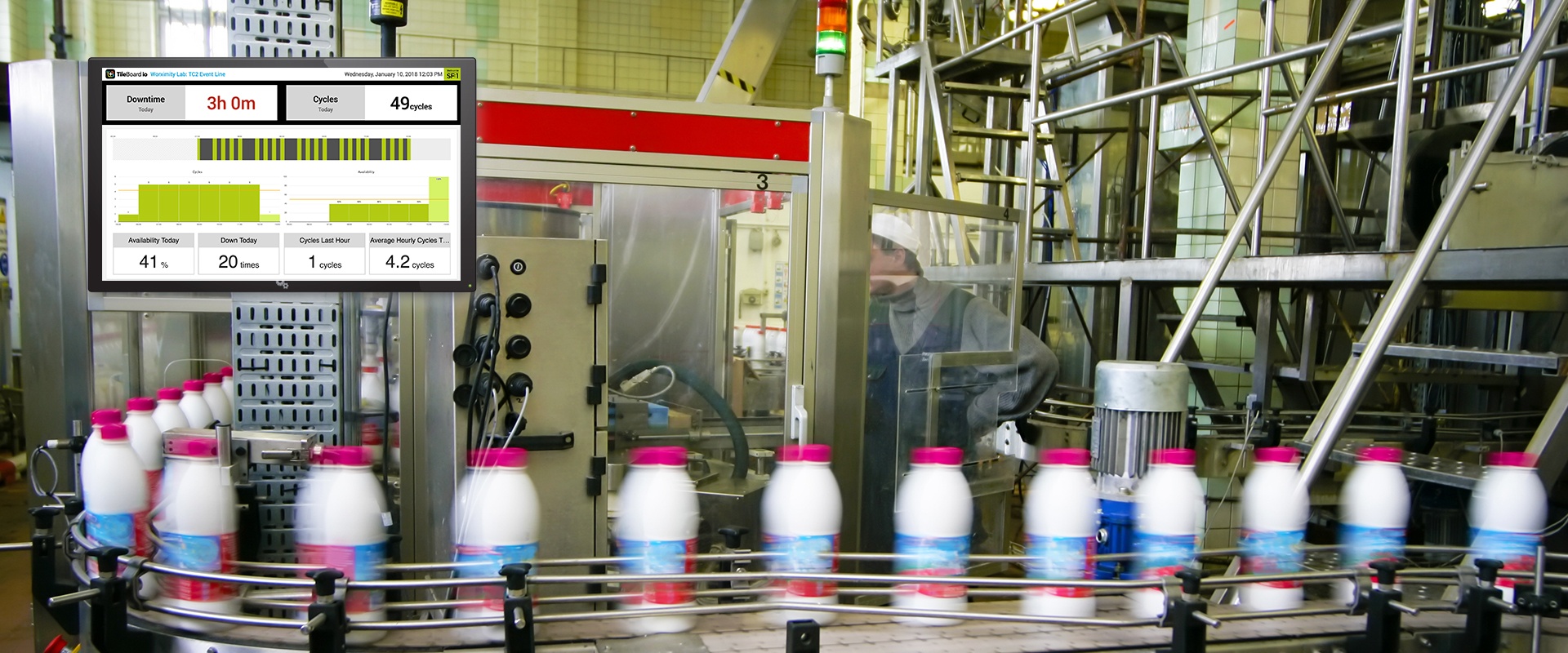
By using a Value Stream Map (VSM) in the food manufacturing industry it is easy to identify and eliminate certain types of waste associated with production that leads to lower levels of productivity and higher costs. In regards to the manufacturing process and how holding tanks reduced the amount of overproduction created, which is a form of waste or Muda as defined by the Toyota Production System (TPS), the Value Stream Map (VSM) was able to identify the lead time that it would take to package a product and proved that it was worthwhile to have a storage tank to sustain the finished food product for a longer period of time until it could be packed. By analyzing the Value Stream Map (VSM), food manufacturers are able to identify what steps during the manufacturing process were creating the most was non-value adding waste and could then work towards resolving those issues in an effort to decrease waste and increase efficiency.
Download our Free Lean Manufacturing and Industry 4.0. ebook now!