According to Forbes magazine, “it is estimated that in the last 25 years, global milk production has increased by 61% (average 2% per annum) and there would be an increase up to 177 million metric tons by 2025.” Despite the advances of plant-based milk and dairy analogs, milk and dairy products production continues to increase, showing consumer loyalty to dairy products in general.
While some dairy farms are introducing advanced manufacturing concepts such as Robotics, Lean Manufacturing and Industry 4.0, farms themselves are still largely a manual labor intensive business. However, once raw milk is delivered to a dairy processing facility, all of the primary processes of turning raw milk into value added products are machinery intensive.
This means that dairy processing facilities are ripe for disruption using Industry 4.0 technologies and in particular Smart Factory Analytics that monitor machinery activities directly to improve process efficiency.
The primary processes that add value to raw milk are shown here:
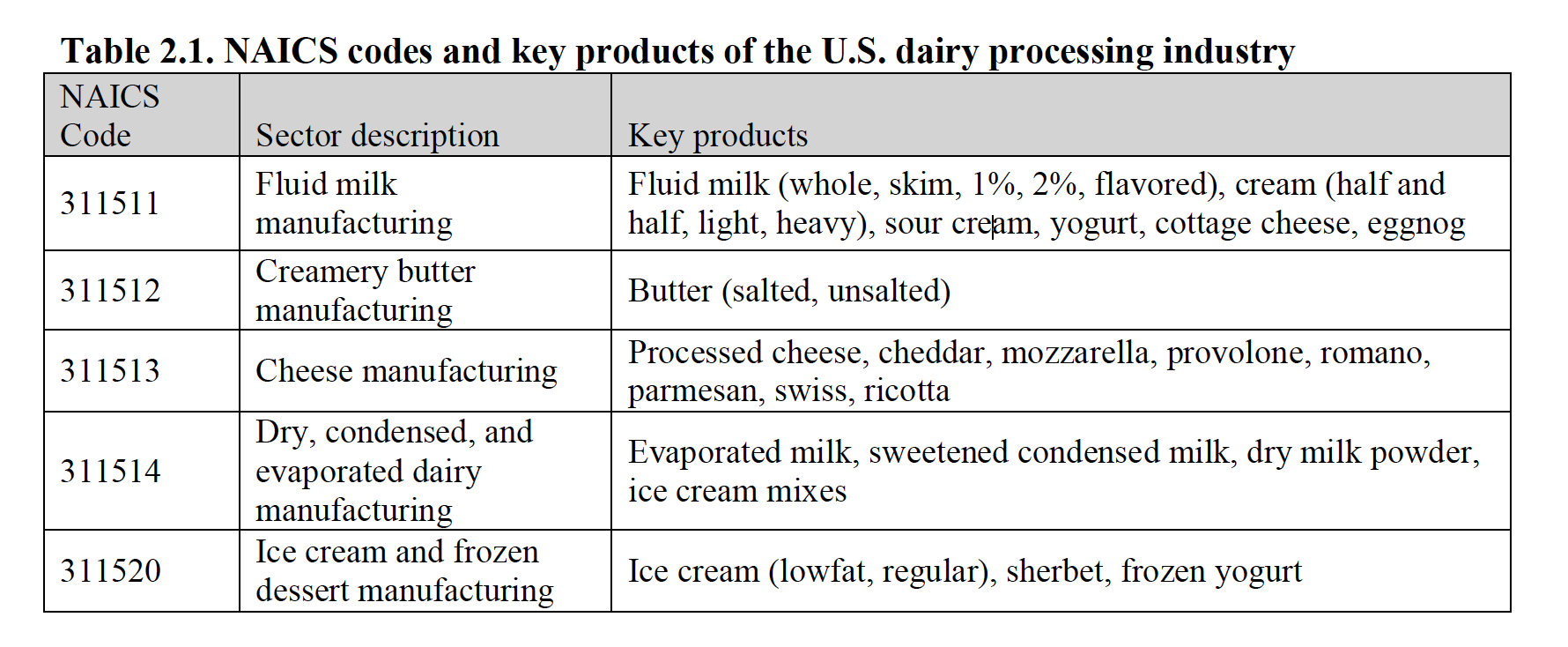
Primary Dairy Manufacturing Processes: Source EPA
Each of these processes requires capital intensive equipment and machinery and all of them require a packaging line of some type to package the final product and prepare it for shipping. Each of these primary dairy products manufacturing processes has opportunities for process efficiency improvements using Smart Factory Analytics tools such as Worximity.
1 - Raw Milk Unloading
When raw milk is received from the farm, it’s unloaded from the carrier, usually some type of tanker truck. The unloading process requires a pump, usually a positive displacement pump with a rubber impeller. After unloading, the truck itself is spray-washed by pumping hot water and sanitizer into nozzles fitted to the top of the tank which direct water over the entire internal surface of the truck tank. Because the trucks that pick up raw milk from the farms are only insulated and not refrigerated, timeliness of unloading is critical. You can’t have trucks backing up in the yard for extended periods of time without product deterioration. These trucks tend to be large, so any extended delays can cause significant cost in wasted raw materials.
The efficiency of the truck unloading bay is critical to get trucks into the plant and raw milk into tanks or a manufacturing process. Bottlenecks in this area can lead to spoilt products or loss of production in downstream processes.
Unloading: Worximity can monitor the flow meter of the unloading process in order to ensure that the unloading system is operating and to indicate if the system is operating at below capacity.
2 - Milk Clarification & Cooling
Raw milk is often then sent through a centrifuge for ‘Clarification’ to remove particulate contamination and cooled through a heat exchanger as it makes its way to storage or further processing. One challenge with processing dairy products is that heat exchangers can frequently foul. As heat exchangers become fouled, the exchange efficiency decreases, the energy to push the liquid through the heat exchanger increases and the flow decreases, extending process time and reducing process efficiency. This means that processes involving heat exchangers can become sources of bottlenecks due to slower processing or downtime due to exchangers having to be cleaned.
Clarification & Cooling: Worximity can monitor pump operating cycles and help to reveal extended processing times helping to identify bottlenecks such as heat exchanger fouling to keep cooling & clarification cycle times at maximum efficiency.
3 - Standardization
The milk is then usually ‘Standardized’ to normalize its fat and nonfat solids content to be that required for further processing into the intended end product. Milk is separated into skim and cream products typically using a centrifugal separator. Sometimes the milk is tested and then just enough fat is separated out to reach the desired target, and sometimes the milk is separated into the two components. In either case, centrifugal separators operate at high speeds so are subject to multiple failure modes and since most of the incoming milk passes through this area, they are a bottleneck potential.
Standardization: Centrifugal Separators like many types of rotating equipment lend themselves well to monitoring using Worximity. Worximity can monitor uptime to maximize process efficiency and identify unplanned downtimes so that maintenance response times can be compressed.
4 - Pasteurization, Steam Generation & Co-Generation
Most dairy products are ‘Pasteurized’ using a heat treatment process. This requires pumps to move the product and again heat exchangers are used at this step of processing. The manufacture of some dairy products such as yogurt requires more intense heating as well.
Sometimes the various heat treatment processes are done in batches but the ideal situation is a continuous process. Because milk under time and temperature changes its composition leading to unwanted flavor changes, keeping this process tightly controlled is essential.
Dairy processing facilities utilize immense amounts of steam for processes like pasteurization. Steam systems include boiler fuel pumps (and motors) and boiler feed pumps (and motors) and these systems may include regeneration loops which recover heat on process outlets, adding more pumps and motors to the system. Some dairies will have a Co-generation system, which uses steam generated by the boiler to drive a steam turbine which then generates electricity. While this can improve energy efficiency and energy utilization, it introduces another complex layer of rotating equipment which needs to me monitored and maintained. All of these pumps, motors and turbines are mission-critical to dairy processing operations.
Pasteurization, Steam Generation & Co-generation: Worximity can monitor the operating condition of critical pumps, turbines and motors, identifying trends which are indicative of process deterioration and product damage as well as conditions which might lead to steam outages which can shut down all operations.
5 - Homogenization
Almost all dairy processes incorporate homogenization. Homogenization breaks down fat globules in order to prevent separation of fat later. This prevents ‘creaming’ where cream rises to the top of a milk container. High pressure piston pumps drive milk through a small opening, creating a steep pressure drop and breaking fat globules into very small sizes, preventing creaming.
Homogenization: High pressure piston pumps require a specific maintenance cycle in order to maintain operating pressure and prevent leakage out of the piston seals. Worximity can monitor operating cycles to ensure that timely maintenance is accomplished, preventing outlet pressure drops that lead to poor product quality and process efficiency, machinery seizures (catastrophic failures) and product leakage to drain.
6 - Cooking and Fermentation
Some dairy processes require cooking or fermentation which means that tight time and temperature control is required as well as reliable vessel filling and draining.
Cooking and Fermentation: Worximity can monitor cooking and fermentation equipment to ensure product is neither over or under cooked. Monitoring fill and drain pumps can compress process cycle times improving process efficiency.
7 - Mechanical Work
Cheese and Butter requires Mechanical Work in the form of mixing, kneading and churning as well as pressing and cutting.
Mechanical Work: Critical equipment to ensure reliable cheese or butter making can be monitored to minimize downtimes and improve process efficiency.
8 - Freezing, Hardening & Evaporation
Additional dairy manufacturing processes include Freezing, Hardening and Evaporation.
Freezing, Hardening and Evaporation: Continuous freezers consist of conveyor lines which can break down due to their harsh environment. Monitoring conveyor lines can minimize downtime and improve process efficiency.
9 - Packaging
All dairy products are ultimately packaged. You can learn about the impact of Worximity on food processing packaging lines below:
Improving Throughput in Food Packaging Processes
How Worximity Improves Thermoforming Efficiency in Food Packaging Process
Why You Should Consider Monitoring OEE On Multivac: Thermoforming Packaging Machines
The Future of Food & Beverage Packaging for CIOs
How to Monitor Vertical Form Fill Seal Machines in Real Time
10 - Cleaning
Dairy processing is a cleaning intensive industry. Good Manufacturing Processes (GMPs) require that vessels and piping must be cleaned every time a different milk product is handled. Cleaning cycles consume a lot of potential manufacturing time, so monitoring and compressing cleaning cycle downtimes can lead to significant productivity improvements.
Understanding how Smart Factory Analytics can improve the process efficiency of the most common dairy production processes can enable you to deliver quick wins in overall plant efficiency.
To learn more about how a dairy radically improved its process efficiency, get the case study below!