There’s a lot of buzz about IIoT (Industrial Internet of Things) technologies, with significant capital flows from VCs into the space. There's also increasing strategic partnership activity and accelerating mergers and acquisitions deals related to IIoT technologies as well as increasingly optimistic predictions about the impacts of IIoT in industries as diverse as manufacturing, distribution and energy.
In any highly active Venture Capital (VC) or Mergers & Acquisitions (M&A) space, there will be hype, as start-ups aggressively compete for financial resources.
To try and model the interactions between the advances in technology, the competition for resources and market-share and time, Gartner has developed their Hype Cycle model. A key transition period of which is the ‘Trough of Disillusionment’. Obviously, for advanced technology customers, and IIoT technologies certainly fall into this category, you want to avoid the trough and enjoy either the Slope of Enlightenment or ideally the Plateau of Productivity!
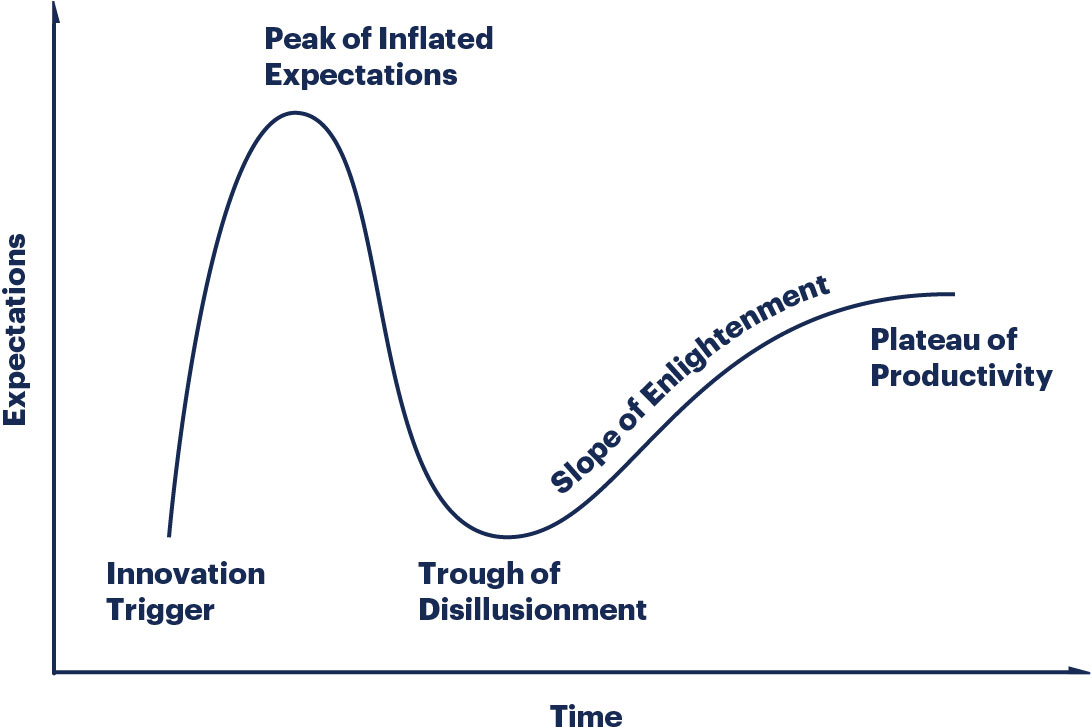
Gartner Hype Cycle Image Courtesy Gartner
As an end customer, how do you avoid falling into your own Trough of Disillusionment and reach the Plateau of Productivity? It’s important when selecting IIoT technology vendors that you have a way of cutting through the hype and focus on working with partners that are delivering real business results.
In this article, we'll lay out how the IIoT ecosystem is viewed.
We'll discuss how and why a key Worximity differentiator is that we focus on achieving synergy between your IIoT implementation and your people through incorporating Process and People into our solutions.
We'll also discuss why this approach is important to how we are consistently delivering real business results.
How is the IIoT Technology Ecosystem Viewed Today?
In an extraordinary report from PwC, Lead or lag? What the Industrial Internet of Things means for deals (you can download here) you can get a grasp of the level of customer and investor interest and investment in IIoT technologies.
There’s now widespread acceptance that the IIoT will revolutionize the way that products are manufactured, delivered, maintained and upgraded.
From the PwC report:
- By 2020, almost 21 billion-plus devices with built-in sensors will be connected to the internet.
- According to PwC’s 2017 Global Digital IQ Survey, 73% of executive respondents currently have IoT initiatives underway.
- Such forecasts are igniting rapid transformation across business. That, in turn, means new paths for both private equity and business investments.
- The industrial internet of things (IIoT) has the potential to dramatically boost productivity and cut costs across manufacturing, transportation, logistics and energy.
- It could also spur new business models.
- By building sensors and networking devices into their equipment, vehicles and facilities, industrial companies can manage their performance like never before. And they can use the resulting data to predict their maintenance needs and sharpen their operations.
- IIoT spending across the manufacturing, transportation and utilities sectors alone reached an estimated $325 billion in 2016. It’s expected to grow to nearly $600 billion by 2020.
- Industrial IoT saw its 4th straight year of growth in 2016, with investment totaling over $2.2B across 321 deals. That translates to a 21% boom in deals and a 5% increase in funding.
In this report PwC lays out the IIoT technology stack like this:
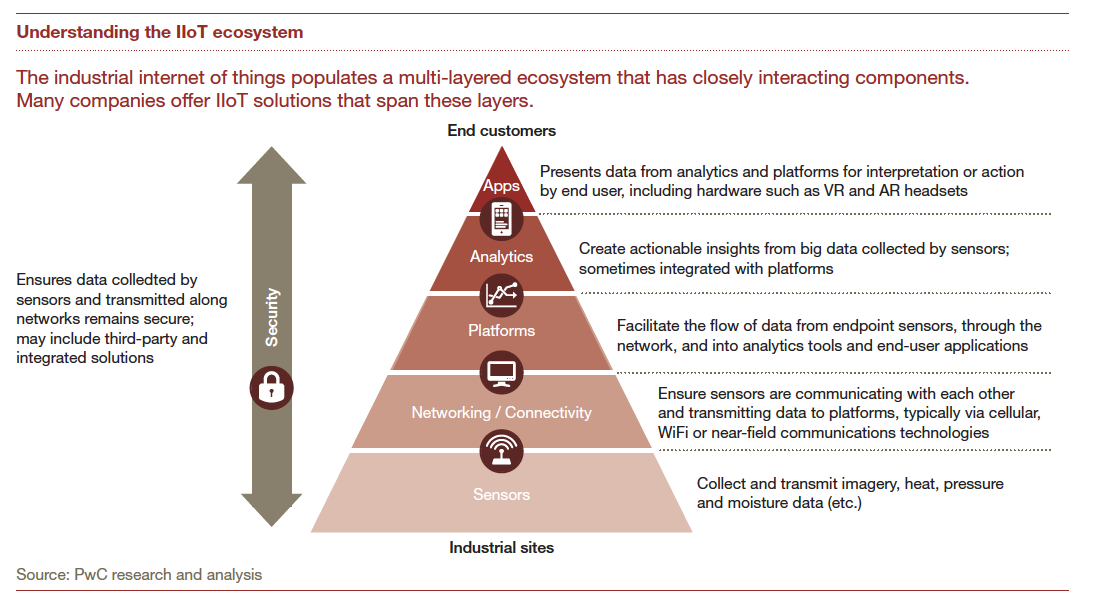
Courtesy PwC Lead or lag? What the Industrial Internet of Things means for deals
This is why, in food manufacturing, leading food manufacturing equipment companies such as Marel are partnering with Worximity to bring their machinery into the IIoT ecosystem. They see that industry is moving in this direction and that they need to accelerate their progress through strategic partnerships that help them to provide the IIoT stack shown above.
What Analysts Don't Mention is that Gaining Synergy Between Your IIoT Technology and Your People is Core to Getting Real Business Results in Manufacturing.
While we agree with much of what the PwC report has to say, as seasoned IIoT practitioners, we see a significant missing ingredient in how analysts view the IIoT market. An age old IT trope is that to effect real business change, you have to address three things, Platform, Process and People.
When these 3 are in synergy, magic happens.
According to the Wikipedia page on Change Management:
“Placing people at the core of change thinking was a fundamental contribution to developing the concept of change management.”
In other words, unless you address Process and, most importantly, People as well as the technology Platform, you’ll not achieve real business results with your IIoT investment. This is what we call Synergy.
Fortunately, manufacturers have a deep toolbox of proven improvement processes available to them.
It's our view that the most successful IIoT implementations will incorporate real-time machinery analytics into a dashboard that is configured to support a proven manufacturing improvement process.
A solid manufacturing IIoT solution snaps right into the implementation of the following processes in order to deliver synergy between the people responsible for delivering business results and the IIoT technology:
Six Sigma is a commonly used company program that intends to reduce production problems and inefficiency in manufacturing companies. Specifically, it aims to eliminate variation in products so that fewer products are lost from production as a result of defects. It is structured so that employees are put on different teams to be assigned to specific projects that aim to increase the company’s net profit. On these teams, some individuals have more advanced project management training than others, and “belts” are used to indicate who the most advanced members of the team are, with “black belts” being the most advanced members.
Lean Manufacturing is another common process that aims to reduce waste. It was originally used by the Toyota Motor Corporation in Japan, and has helped shape the company they are today as the world’s largest auto manufacturer. Different types of waste originally identified under lean manufacturing include defects, overproduction, waiting, non-utilization, transport waste, inventory, motion and excess processing. Under this program, anything that a company spends resources on that doesn’t directly help bringing a product to a customer is considered loss, and must be minimized or eliminated.
Total Quality Management is a process centered around customer satisfaction, and emphasizes involvement of every employee. TQM has 8 main principles, some self-explanatory such as having customer-focused goals for customer satisfaction, full employee involvement and communication.
Other TQM principles include:
- Process-Oriented Thinking – Finding steps in a system where improvement is possible
- Integrated System – Each department understands how they interact with others
- Systematic Approach – Creating action plans when improvement projects start
- Continual improvement – Diverse solutions found to meet customer and shareholder expectations
- Fact-Based Decisions – Data used to pinpoint trends and make future projections
The Plan-Do-Check-Act(PDCA) Cycle is a process that is meant to tackle small problems and to make incremental improvements in many areas of a company. The cycle has four phases, as indicated in the name. The “Plan” phase pinpoints an area to focus on and involves creating an action plan to tackle the problem. The “Do” phase aims at testing the Plan phase’s effectiveness on a small scale. The “Check” phase analyzes the results and identifies improvements that can be made within the cycle. Finally, the “Act” phase implements wider changes if the test yields positive outcomes, if not, the cycle is restarted at the planning phase.
Statistical Process Control (SPC) is also a type of company program, but it involves more automation than others. SPC uses control charts to monitor process behavior, identifying Common Cause Variation(CCV) and Special Cause Variation(SCV). CCV is unavoidable imperfection in a process, where as SCV is variation caused by external factors. Automated data gathering instruments can accurately collect data that can identify if SCV is occurring, and can help a company decide if corrective action needs to be taken to change a production process.
Historically, the failure points of implementing these processes have been:
- having accurate Real-Time analytics that enable rapid decision-cycles that can help practitioners to converge on manufacturing improvement steps that deliver results fast enough
- engaging employees in contributing to the success of these initiatives by training them in proven processes with defined business goals
Smart Factory Analytics technologies such as Worximity now provide the real-time analytics that process improvement practitioners have been lacking. Companies need to address process and training in order to fully take advantage of IIoT technologies in manufacturing and gain real synergy between these technologies and the people responsible for delivering results.
Gaining Synergy Between Your IIoT Technology and Your People is How Real Business Results Will be Delivered
Companies like Worximity now provide proven platforms that are delivering significant real business results every day. The most important missing ingredient of most IIoT implementations in our view is getting people on board.
With our implementations, in order to get real synergy between our IIoT technology and the people under pressure to make it work, in addition to enabling and supporting proven manufacturing improvement processes, we also focus on serving key roles within the organization.
You can see how an IIoT implementation that connects real-time machinery data with analytics dashboards can be role-based for key roles like Operators and Operations Management and C-Level Executives or Senior Leadership.
This is also why as you peruse our blog, you’ll see a large body of content related to the people side of Smart Factory Analytics and IIoT implementations.
Interested in gaining real synergy between your IIoT implementation and your people?
Get the best-practices guide here!