What does Industry 4.0 mean for the food and beverage industry and what are some of the logistical considerations? A recent article by Megan Ray Nichols at Industry Today looks at how Industry 4.0 (I4.0) and the Internet of Things (IIoT) will affect the food and beverage industry and what some of the pitfalls moving toward it might be.
Uses of Industry 4.0 in the Food & Beverage Industry Now
This includes the use of digital and online technologies for efficiency gains—to collect information about processes, equipment performance, suppliers and orders as well as big data aggregate information from suppliers, manufacturers and clients.
Manufacturers can make informed decisions based on quantitative data. Research and development time be can decreased (e.g. using 3D printers to make prototypes.)
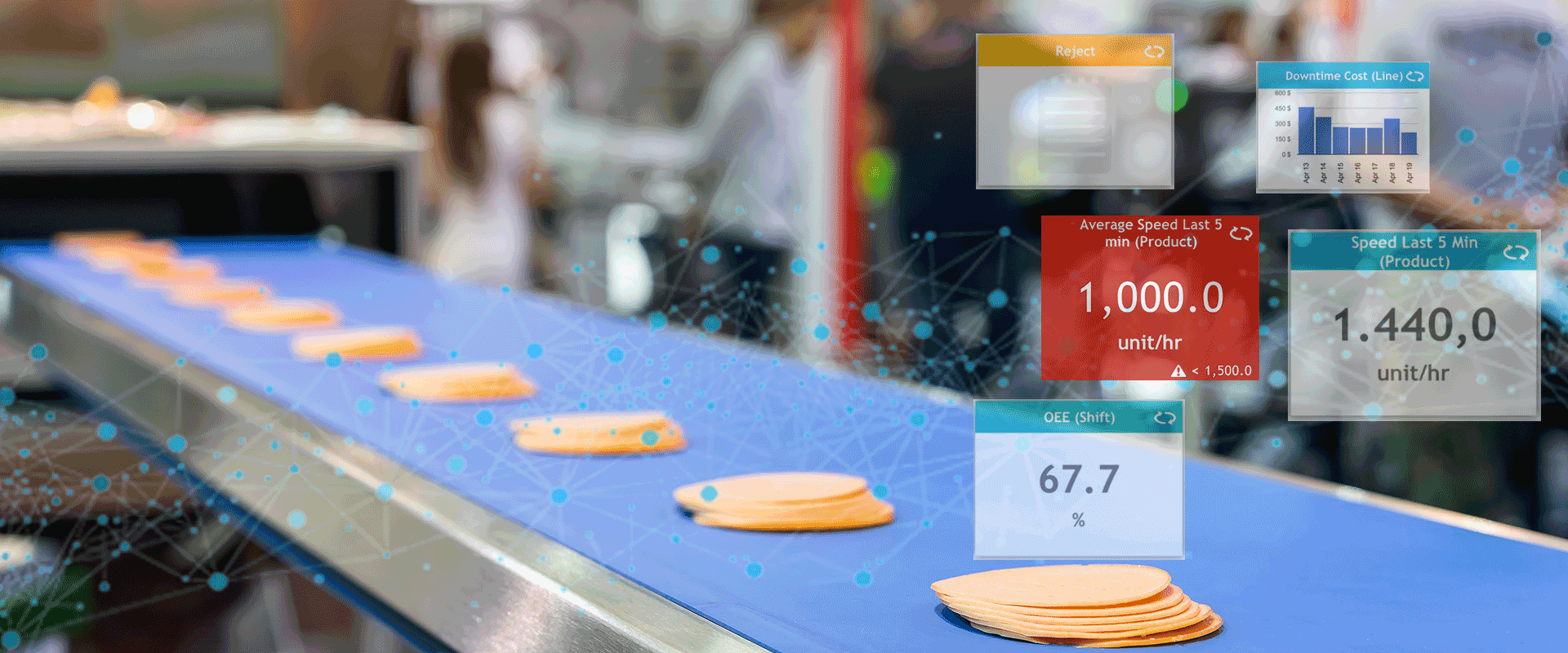
Advantages to Using I4.0
While common challenges in the industry range from product recalls to serving customer demands—data gathered from using I4.0 technologies can turn manufacturers into predictors rather than reactors.
Some examples of I4.0 in food and beverage manufacturing that bring a competitive edge include:
Tracking
- RFID technology (radio-frequency identification tags) helps source ingredients & trace products.
Data:
- analysis speeds up response time to problems;
- collected on problems is easily accessible;
- collected from online customer shopping makes it easier to track preferences; and
- from customer profiles can be used to predict purchases, timing & quantity.
Maintenance
- I4.0 helps predict equipment maintenance using wireless sensors.
- Predictive maintenance keeps flow of foods going, prevents blockages.
Barriers to Transitioning to I4.0 in Food & Beverage Manufacturing
- Up-front investment in employees & new equipment.
- Manufacturers may be hesitant to replace equipment that still works.
- Replacing less-skilled workers with technical professionals.
Problems With Implementing I4.0
- Over-implementation of IIoT tools creates digital waste & unnecessary information.
- All aspects IIoT need to be implemented for best results.
- Hidden costs: Maintenance, higher paid employees, spending on unnecessary equipment.
- Distraction: Focusing too much on the technology & not on needs of the production facility.