Paper-based data collection systems or no data collection systems are a serious problem for manufacturers who want to cut costs, maximize profitability and stay competitive.
Not knowing what’s going on across the factory floor can result in massive productivity disruptions and waste. With the capabilities and accessibility of sensor-based data collection systems, there are fewer barriers to implementing an automated data collection system and real-time dashboard display.
Decreasing downtime with machine monitoring
Even providing basic information such as downtime on real-time dashboards and mobile devices can have a huge impact on uptime. Everyone will react faster to seeing red, and make more of an effort to fix the problem and get back into a green zone. As more data is captured, trends can assist in preventing downtime in the future.
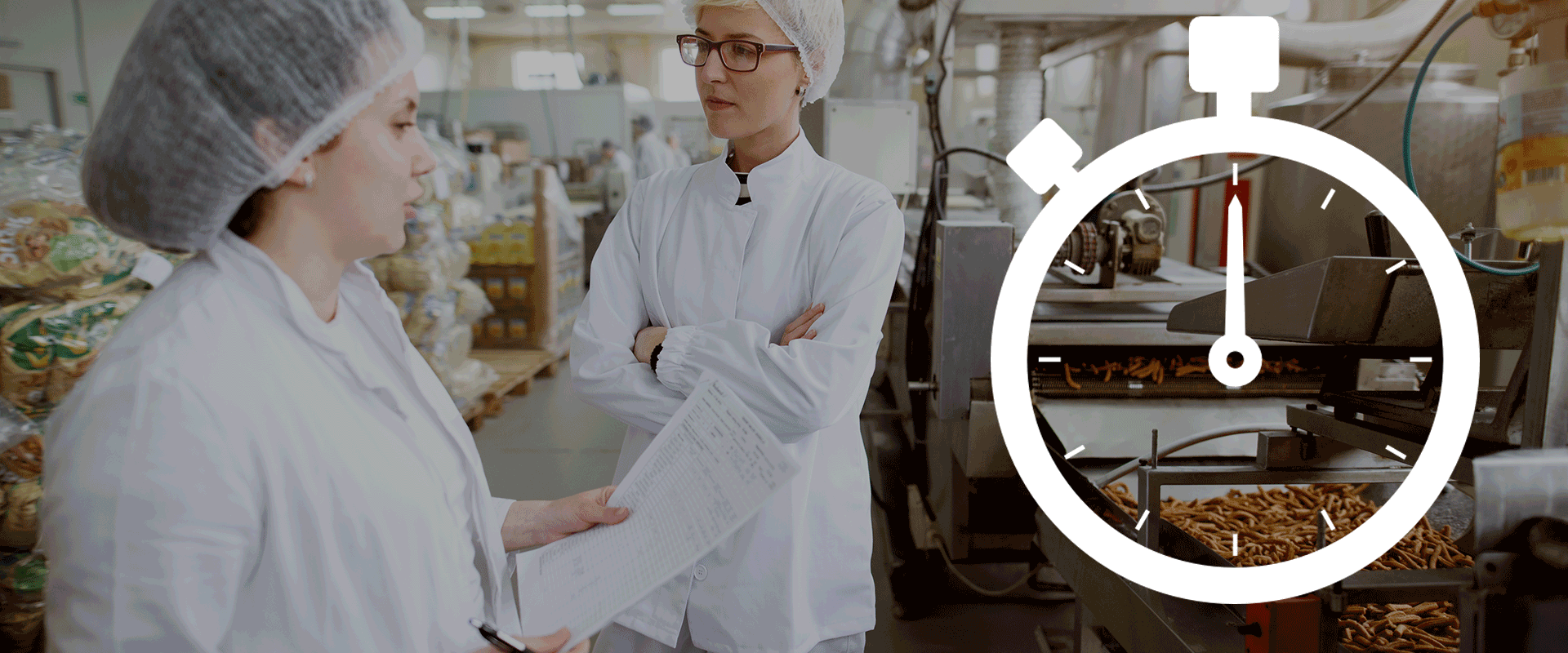
Improving quality with machine learning
By tracking which cells or lines are consistently above and below acceptable quality levels, you can quickly identify and remedy underperforming operations. Continuous monitoring throughout the process helps identify quality problems early for more effective, less costly solutions that don’t rely on manual quality checks.
With enough data and the proper analytics, machine learning can start to predict quality issues. For example, if a situation has occurred several times in the past when the temperature is at a certain level, a certain raw material is at the upper tolerance limit, and a quality issue arises in a much later step in the process, machine learning can flag that pattern when it’s happening. Identifying a problem before it even occurs is a revolutionary approach to controlling quality. Pattern identification is a powerful potential benefit of an IoT solution and making the most of all the data you’re collecting.
Scheduling with better precision
Gathering actual production data, with machine monitoring, gives you more precise, real-world data to work with when planning and scheduling. Sensor-based data enforces consistency, eliminating variances caused by different operators reporting information using personal interpretations.
If there’s a suspicious variance in time required to produce the same item, analytics can highlight that discrepancy, and link to related data so the causes of below-average performance can be investigated and remedied.
Improving inventory accuracy
Machine-generated counts of finished goods produced are much less prone to inaccuracies and errors than manual systems. With real-time information there is no waiting for a manual count. The actual levels of all inventory are available at all times and in all stages of the production cycle.
With true inventory counts, capabilities can be determined with much higher confidence, allowing order fulfillment rates to increase.
Planning maintenance with machine monitoring
If a something on a machine needs repair, do you stop the line to fix it or keep patching the process together to keep the line moving? That’s a strategic decision that shouldn’t necessarily be made by the machine operator. With real-time dashboard information, the maintenance issue can be made visible to the level of management required to decide when to schedule the required fix.
Real-time data displays offer many benefits that show results quickly.
Discover more benefits of real-time dashboards.