Le client
Founded in 1867, Arterra Wines Canada is a leading wine producer offering some of Canada's most popular brands. The company’s portfolio features a wide range of products, from premium to mass-market, including brands like Jackson-Triggs, Inniskillin, and Sandbanks. Arterra is also known for its innovation in wine production and commitment to sustainability, with several initiatives aimed at reducing environmental impact, such as sustainable vineyard practices and eco-friendly packaging solutions.
With three commercial wineries, Arterra employs more than one thousand workers and operates 10 facilities throughout Ontario, Quebec, and British Columbia. Widely recognized throughout Canada, Arterra is beginning to establish an appreciation for Canadian wines outside of the country.
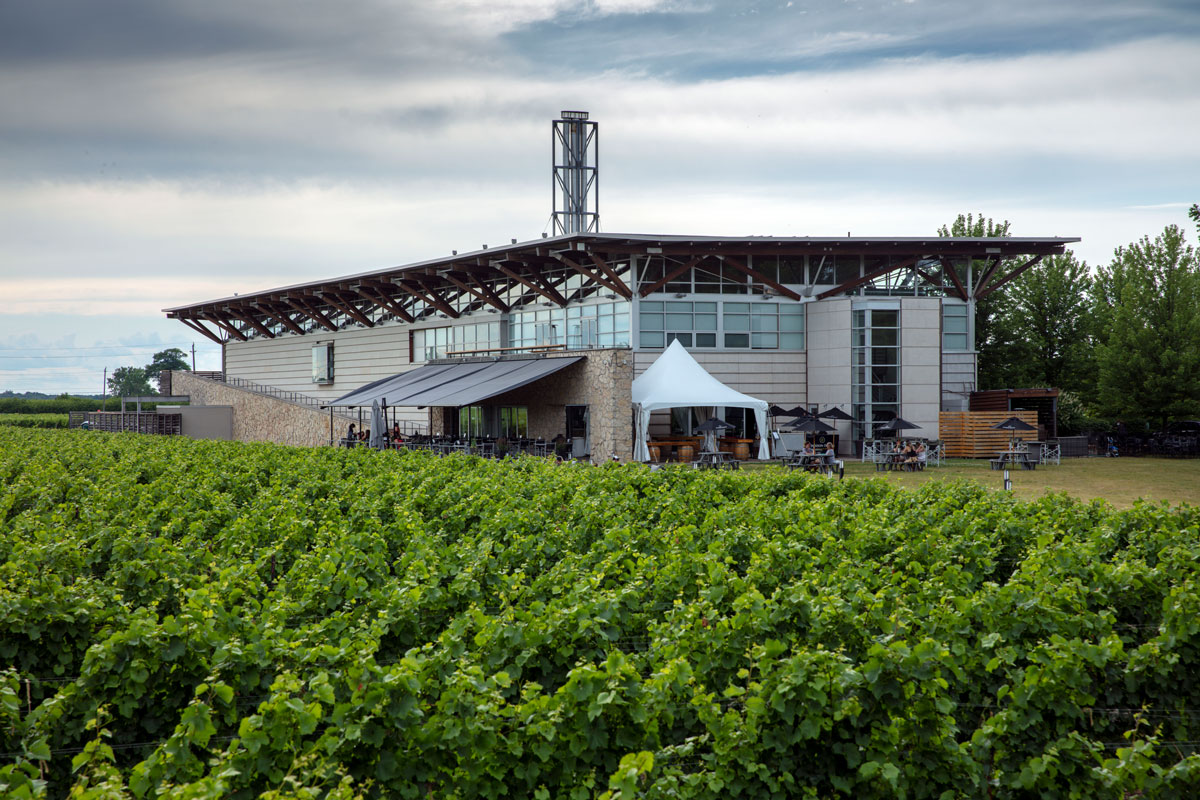
Le défi
Arterra processes and bottles fresh seasonable fruit from its domestic vineyards along with the blending of imported wines . Thanks to Ontario’s recent retail modernization, the company’s brands are widely available through a growing variety of outlets such as Costco and Circle K as well as convenience stores and service stations.
With larger distribution comes fulfillment challenges and Arterra is continually searching for ways to optimize production efficiency, control costs, and leverage its skilled workforce. Much of the responsibility at the company’s Niagara Falls facility rests with Operations Manager Adam Fairman. A thirteen-year veteran with the company, Fairman oversees and coordinates activities associated with warehousing, bottling, selling, production and maintenance. This includes ensuring that operating budgets conform to the labor, supply, and maintenance standards and production requirements of each line.
Balancing rising costs with competitive pricing is a constant battle for any business, and winemakers are no exception. Fairman explains that with climbing inflation, high interest rates, increased safety regulations, unpredictable supply chains, labor shortages, and a looming recessionary cloud, production efficiency is critical to maintaining profitable cost-per-case targets.
“We have a specific cashflow goal for the company and it’s important that we hit that mark. There’s a complex formula that rolls up into what a cost-per-case would be averaged over box and bottle formats. We use that data to set an internal cost-per-case budget. If we can hit that goal and produce the case of wine for X amount of dollars, we make X amount of profit. In turn, the customer buys it for X amount of dollars, and everyone gets a win.”
For Arterra, understanding exactly where, when and why production downtimes occur is critical. And until recently, this was information that their production monitoring and reporting system was not providing.
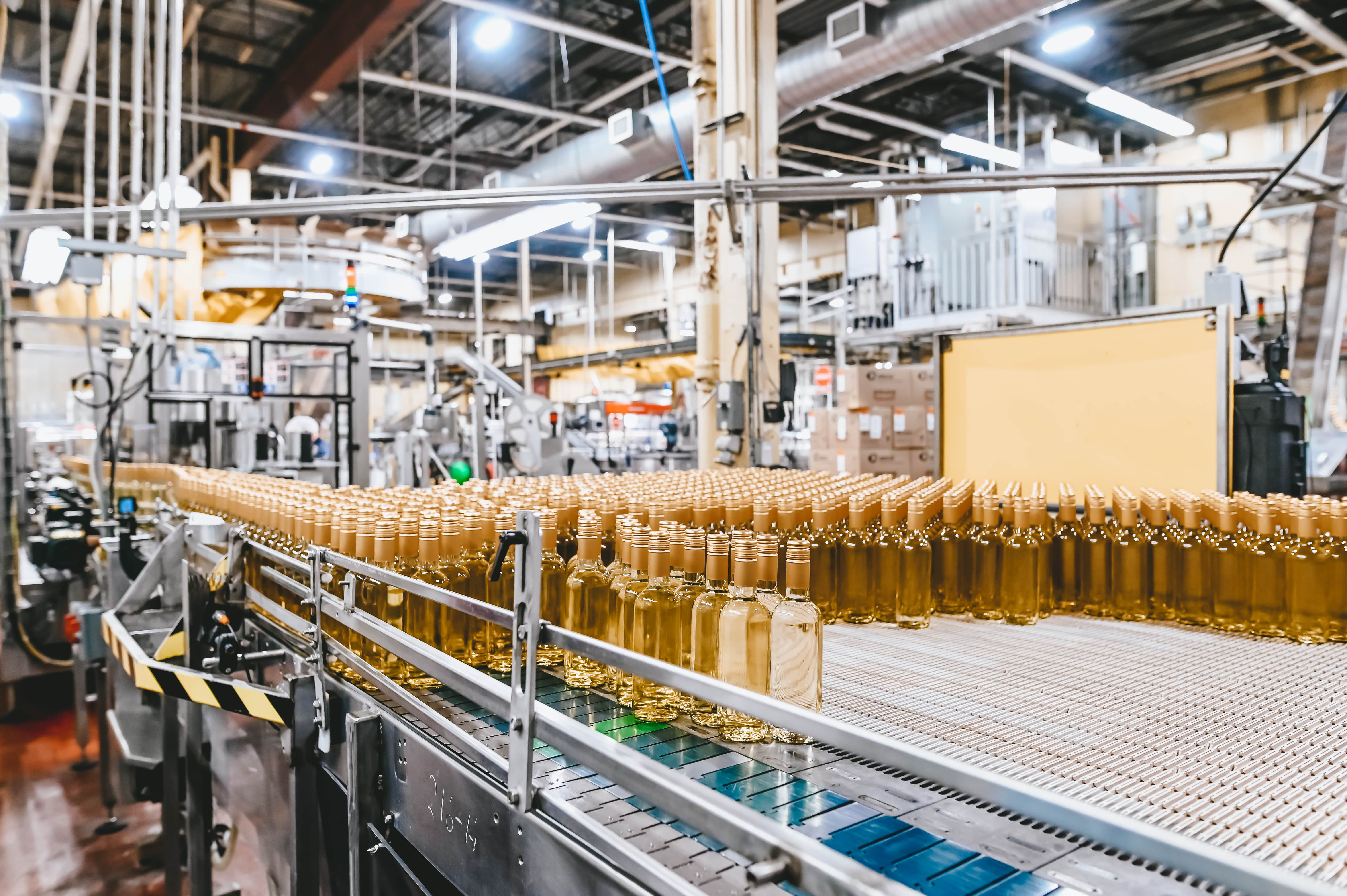
Thanks to Worximity, we’ve got a new problem. We’re ahead of schedule! This is great because we can plan. In the past, we would hope to meet schedules, now we can stay ahead of the game.”
La solution
While visiting the company’s British Columbia winery, Fairman was introduced to Worximity’s production monitoring and analytics solution. Almost immediately he recognized its value.
“The difference between Worximity and what I was using at the time was night and day. Worximity was flexible and user-friendly, displaying a variety of metrics like OEE, output, speed and so on. Not long after, our Quebec operation adopted the solution. Then, I was offered a chance to try it and jumped on the opportunity. I was excited to validate what I knew Worximity could do for us.”
Fairman selected a line for evaluation, and with some assistance from Worximity, a pilot project to test the software was underway. The results and feedback from the operators were encouraging and it was decided to roll the system out across all four production lines.
“While our previous system provided a lot of data points, it was very difficult to collate that information into anything useful. The ease with which Worximity translates raw data into analytics and insights is huge for us. I can run reports within seconds to pinpoint our top three or top ten downtime issues. And we can drill as far down as we like into issues. As managers, we sometimes think we know what our challenges are. But now, we can identify the real issues with confidence. Armed with this information, our focus is suddenly redirected to a different area, saving time and money.”
While change can sometimes be a challenge, Fairman said that workers across the lines have enthusiastically embraced Worximity.
“From supervisors to operators, everyone loved the software from day one. The previous system was very clunky and cumbersome. Identifying reasons for downtime was difficult, even though the software was connected to our equipment PLCs.
With Worximity, we can customize our data like discounting micro stops. This gives us a better picture about what’s really impacting production and why.”
Every quarter, each Arterra winery presents a business report to the executive team using data from Worximity. These reports outline performance and downtime, along with issues and corrective actions. Fairman can also generate custom reports on downtime associated with changeovers, maintenance challenges, and late start-ups. This helps to set immediate priorities in daily team meetings as well as long-term strategies for management meetings.
“Each day starts with a review of the previous day’s report where we identify the top three things we’re going to work on to make tomorrow better. It’s a constant evaluation of what needs to be done and what gets priority. We assign a realistic timeframe for actions. If we’re replacing a part on a packer, for example, we’ll assign that as a 24-hour fix. Other issues might take longer to wrap up, such as a nitrogen shortage we once experienced. But regardless, we’re always aware, measuring, addressing and improving which is the important thing.”
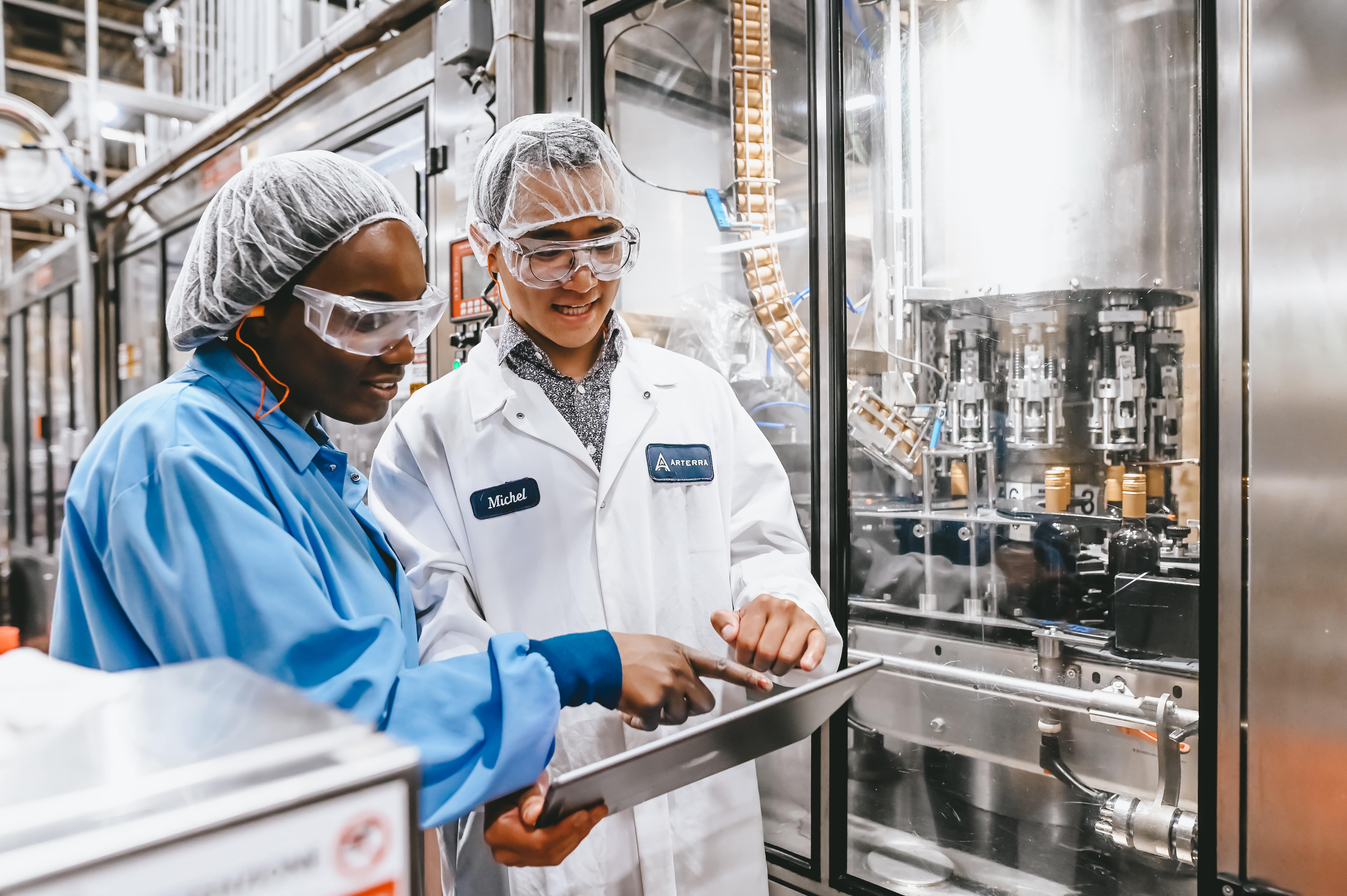
Les résultats
With four lines and three shifts producing over one million cases a year, Arterra Niagara Falls is the company’s largest facility offering a significant opportunity for improvement. With Worximity’s support, the winery is reducing costs while increasing capacity and operational efficiency.
The results speak for themselves:
- Downtime on the packer line was dramatically reduced. In just 4 months, downtime was slashed from 4,043 to 1,554 stoppages. This translates into $125,000 Annual savings.
- Line performance was increased measurably. A 16% productivity improvement is netting the company an additional.
- Line changeover time was reduced from 8 to 5hours. This translates into annual savings of $100,000.
- Better communication and employee engagement.
By adopting Worximity’s solutions across all wineries, Arterra has opened the door to improved collaboration across plants and within each winery. What’s more, streamlined processes are delivering breakthrough levels of improvement which is presenting Fairman with what he gladly refers to as some unique challenges.
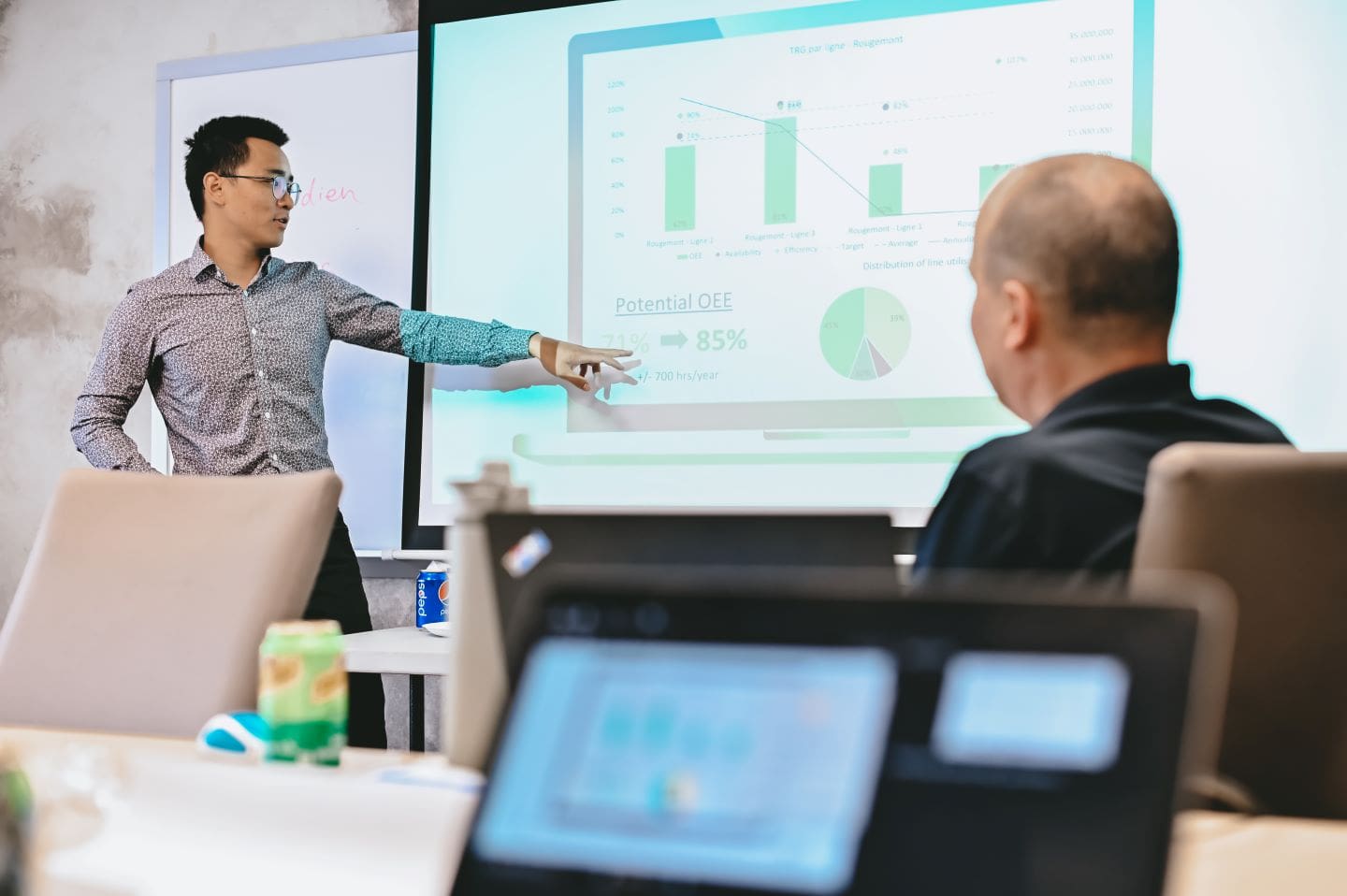
“Thanks to Worximity, we’ve got a new problem. We’re ahead of schedule! This is great because we can plan. In the past, we would hope to meet schedules, now we can stay ahead of the game.”
Heads that the partnership between the companies is invaluable.
“Worximity is incredibly responsive to our needs and requests. When we propose ideas, the entire user community reaps the benefits if they align.”
Improving OEE is beneficial for any manufacturer, and, with documented results in hand, Fairman is quick to recommend that any manufacturer strongly consider taking a closer look at Worximity.
“I showed the software to a visitor who was touring our facility. He was impressed by what I was able to do right from my phone. In addition, leveraging Worximity’s BI services to automate the shift report saves us time. Our daily meetings are shorter and more productive. Now supervisors are back on the floor rather than spending time behind their computer.”
And on a personal level, Fairman says that he has greater peace of mind away from work.
“I have my phone on 24/7, that’s a part of my job. But now I can rest a little easier knowing there’s better communication, less confusion, and the software is doing its job. It’s a level of confidence that I never had before.”