Operating equipment effectiveness (OEE) as a lean manufacturing metric can serve as the primary measure driving a company's lean improvement program. Because of OEE's comprehensive construction, values for this metric represent an excellent overview of how effectively a plant is functioning and can demonstrate the success of ongoing improvement efforts.
Lean manufacturing allows managers to react quickly to changing marketplace conditions and face unusual challenges that arise. The sudden and life-changing appearance of COVID-19 highlights the need for constant vigilance and the ability to respond to changes quickly. Worximity stands ready to assist our customers respond to current changes and meet the challenges presented by this outbreak.
What Is Lean Manufacturing?
Lean manufacturing is a method of production that incorporates the following five key performance principles:
- Understand and focus on the inherent and specific value of each product, considering customer expectations, preferences, and aversions.
- Analyze and remove any non-value-added process for each step that moves a product from its origination to customer delivery.
- Ensure the product flows through the value stream without any delays, interruptions, or stops.
- To the degree that it can be accomplished, allow customers to pull product from one step to the next through the process without interruption.
- Manage and change the production process such that the amount of time, the number of steps, the amount of information, and the number of rejects continue to fall.
OEE Is Closely Tied to Lean Manufacturing
OEE is a powerful lean manufacturing metric that reflects the current condition of the five performance principles that make up lean manufacturing. Specifically, the OEE formula includes values for the following:
OEE = Availability x Performance x Quality where
Availability is (Run Time/Planned Production Time), and
Performance is ((Ideal Cycle Time x Total Count) / Run Time), and
Quality is (Good Count / Total Count)
The overall OEE score, therefore, includes factors that drive progress in lean and continuous improvement. For example, because “run time” in the OEE equation includes downtime, which is a ”waste” within the concept of lean, eliminating downtime will make a positive contribution to both OEE and lean manufacturing. Therefore, by improving “run time,” a manufacturer can move closer to the goal of process perfection while, at the same time, improving the OEE score. In today's highly competitive marketplaces, companies must continue to improve or risk losing market share.
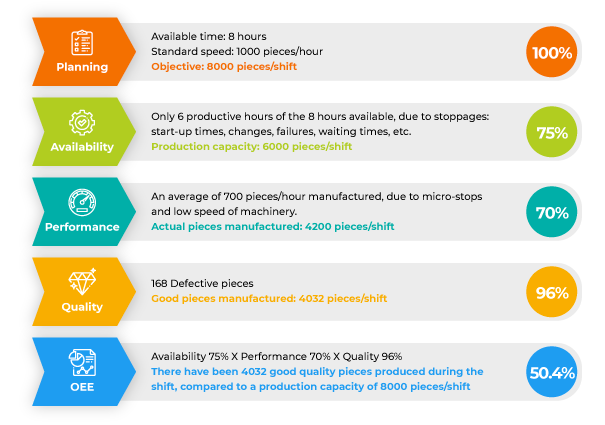
How Does OEE Impact Lean Manufacturing?
Integral to OEE are metrics that support and guide a company’s process improvement effort. Interdependence between OEE and lean manufacturing applies to all of the contributing values that make up the OEE formula. As a result, using OEE as the primary lean manufacturing metric of improvement, a processor can track how changes are impacting operations period by period.
The Importance of Tracking OEE and Other KPIs
Understanding what is happening within manufacturing processes results from interpreting OEE and KPI calculations and results. These metrics track where a manufacturer has been and point the way to the future. The application of technology to gather and develop production line data is an important key for linking people, processes, and equipment.
Up-to-the-minute operating information is crucial for watching the progress of any manufacturing process. Should the process swing out of specification, immediate knowledge of the problem allows a manager to take quick corrective action. Applying technology at the process step level helps manufacturers move ever closer to Industry 4.0's Smart Factory.
How Worximity Technology Tools Can Help Manufacturers Become Smart Factories
The drive toward the factories of the future is a result of the integration of processes, technology, equipment, and management. These four critical components are gradually merging and will continue to do so with the incorporation of artificial intelligence, merged machine processes, human-machine interfaces, smart equipment, robotics, and improvement in information.
Worximity Technology provides a suite of data collection and analytical tools to help manufacturers monitor OEE and move toward Industry 4.0. These tools integrate with both old and new production equipment to provide OEE and lean manufacturing metrics. Using the Internet of Things (IoT), Worximity's tools gather operations and process data, store it in the cloud, and prepare applicable performance monitoring measures.
Worximity's system design is configurable to fit any processing situation. TileConnect (data gathering) sensors are fastened to equipment, collect needed data, and transmit the information to the cloud in real time. This data is then processed using Worximity's Smart Factory analytics software, after which OEE and other KPI results are displayed on Tile Boards or dashboards located throughout the factory. Applying this data to the five principles of lean manufacturing, managers can develop strategies for improvement.
Reducing process cycle times, improving quality, reducing costs, and increasing throughput can be achieved using Worximity's production monitoring tools. For managers on the road to the factory of the future, using Worximity's Smart Factory analytics systems is a big step in the right direction. To learn more about OEE and lean manufacturing metrics, call Worximity today to discuss your applications and schedule a demo.