There's no doubt about it: Industry 4.0 technologies are imperative for manufacturers wishing to remain competitive. For many, the first step consists of automating processes that were otherwise manual. As these automated systems are an integrant part of digital systems, increased digitalization is reached with Internet of Things. Such technology involves the use of smart sensors to attain greater production performance with real-time data analysis. Increased manufacturing productivity is what entices and motivates manufacturers to make the shift. The same product volume can be produced at a lesser cost, or more products can be manufactured for a negligible increase in cost, if any. In that case, investments in technology serve as a competitive enabler. A research conducted by Siemens revealed that by opting for digitalization of their processes, productivity gains made by manufacturers were to be equivalent to between 6.3% and 9.8% of their annual revenues.
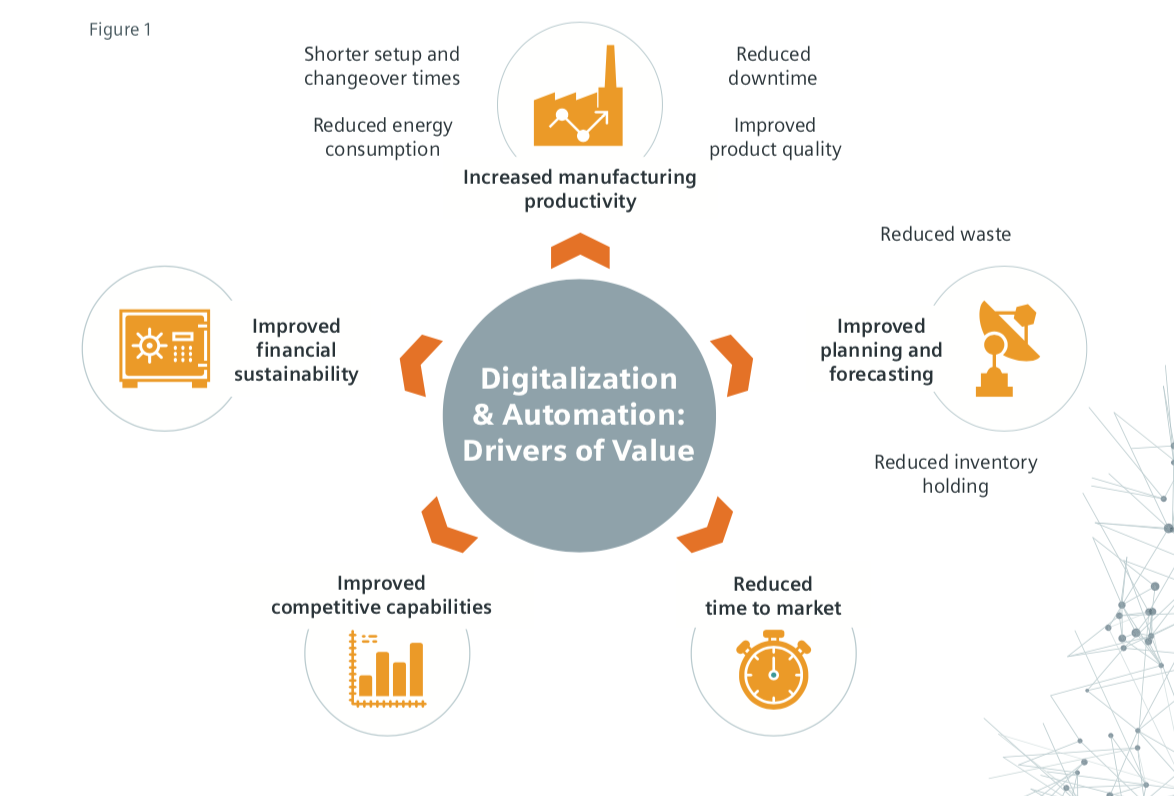
What does this means for dairy producers?
Slowly but surely, Industry 4.0 is making its entrance in the Dairy Product Industry. Sensors, enabling an automatic processing of ingredients, consumables and packaging re-orders, also allow for a collection of production data. This data can be paired with historical demand trend information to predict future consumption habits.
What concrete results does it yield? For starters, less waste, enhanced customer service and better reactivity to changes in demand - waste management and production capabilities being key productivity and cost-control factors for food manufacturers. Furthermore, machine performance can be remotely monitored in order to reduce downtimes and maximise uptimes. Amongst one of the most meticulous industries, dairy producers grant a very particular attention to safety controls. Contributing to food quality and safety, smart sensors also used to improve other areas such as traceability and packaging.
We have reached a point where smart factory technologies such as Worximity's TileBoard software can be programmed to send off alerts when critical limits are attained. Thus, floor employees and plant managers can improve their reaction time, which in return minimizes losses and costs. Manual tasks are slowly phased out to enhance safety, decrease the amount of avoidable errors and reduce legal liabilities.
One thing remains certain, the benefits of implementing such a technology cannot be overlooked. As mentioned by the Operations management of a major dairy products group,
“Digitalized technology has allowed us to see what is happening in detail within our production environment in real-time throughout each day. We have full insight into downtime detail and production rates, which is helping us to continuously introduce improvement adjustments in each of our lines. Overall, we’re seeing average productivity improvements of around 13%."