If you’ve identified security and resistance to change as risks to incorporating Industry 4.0 in your factory, you’re not alone. Security must be taken into consideration, balancing caution with manageable risk. However, sometimes, an even bigger obstacle to implementing Industry 4.0 is resistance to change. Something as basic and necessary as monitoring KPIs can cause friction with operators, but there are ways to manage the risk and overcome it.
Increase functionality with no new restrictions
One strategy is to ensure that you aren’t losing any functionality or introducing any restrictions when implementing a connected solution. For example, a properly configured automated downtime monitoring solution should make less work for an operator, requiring less manual intervention to track information.
If operators previously had to use a clipboard to write down reasons for downtime, an automated system with pre-configured prompts can make it much easier to simply select a reason with just a few clicks, saving time and reducing disruptions. To ensure that no functionality is lost, the pre-configured prompts should match reasons the operators know and use.
FIND OUT HOW PREMIERE MOISSON GAINED 27% IN RESPONSIVENESS IN CASE OF DOWNTIME.
Make monitoring a game
Another strategy is to use gamification, or game mechanics such as points, challenges and incentives for reaching goals. These incentives help increase employee engagement and can make them less fearful about the change.
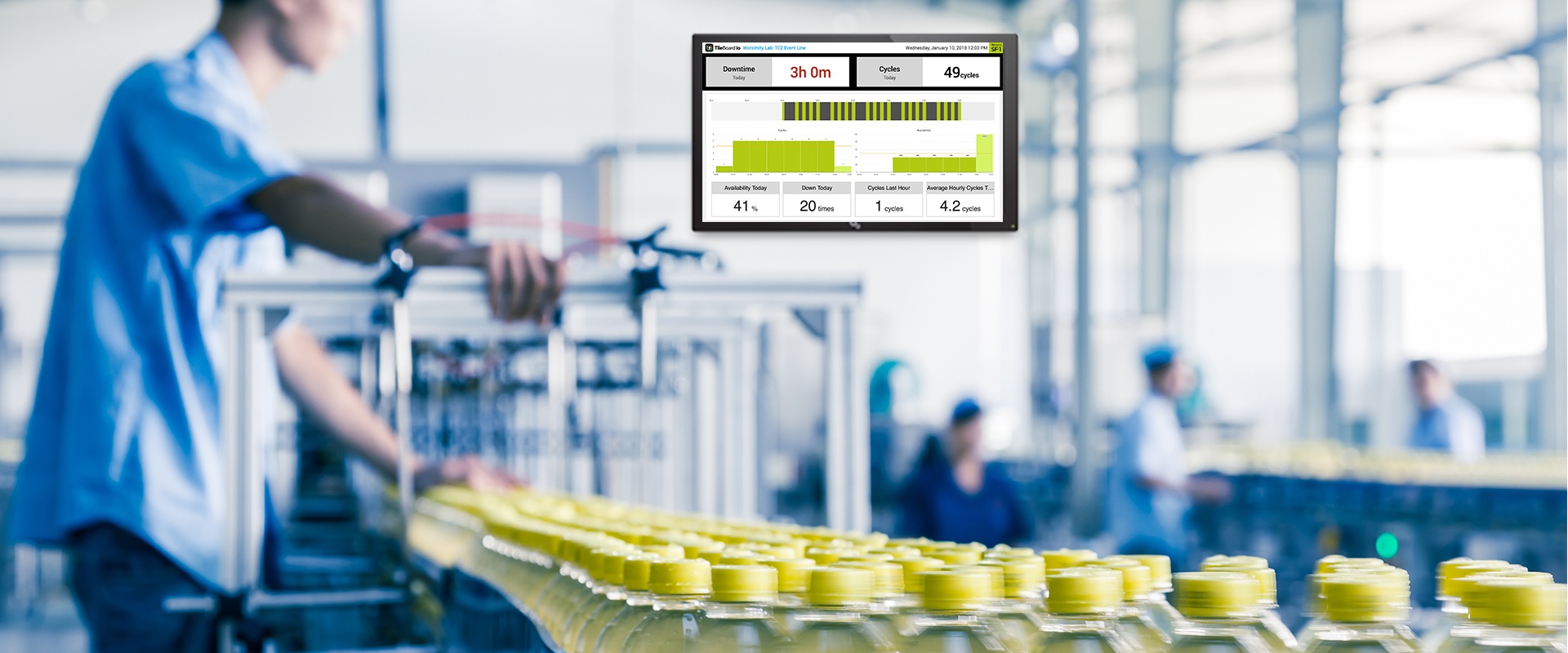
Monitoring solutions can feel less like “watchdogs” and more like trackers when they’re introduced as part of an incentive program or game. Introducing new display information as tracking toward incentivized goals can make people more interested in learning the new system, and working together to win.
Involve IT from the beginning to manage security
Not all risk is the same. Which risks are acceptable and which are not? Your IT security team needs to be involved from the early planning stages to ensure that security protocols are implemented along with any connectivity, and that all security procedures are followed and enforced. The potential of Industry 4.0 to connect your factory and allow communication to flow is powerful, but that power must be balanced with responsible use. There is a balance point between refusing to allow any connectivity due to paranoia, and making it easy for unauthorized devices to connect.
Show benefits early
When planning an Industry 4.0 implementation strategy, including some big wins in the early phases can help win people over and soften resistance to change. One good example is using alerts to allow supervisors to stay connected even while away from the factory floor. By setting up parameters for any indicator such as downtime or below-average productivity, the supervisor will receive a smartphone alert with key information.
Instead of being caught unaware that there was a problem that started hours ago on a remote line, supervisors and managers can have all important information sent automatically in real time. Maintenance personnel can also be alerted automatically, instead of waiting for a phone call. Automated alerts free people to focus on fixing problems rather than trying to track people down to keep them informed.
Even though Industry 4.0 is a technical solution, it’s the people involved who will have the most impact on its success.
Learn more about the benefits of real-time notification.