According to Forbes magazine, “it is estimated that in the last 25 years, global milk production has increased by 61% (average 2% per annum) and there would be an increase up to 177 million metric tons by 2025.”
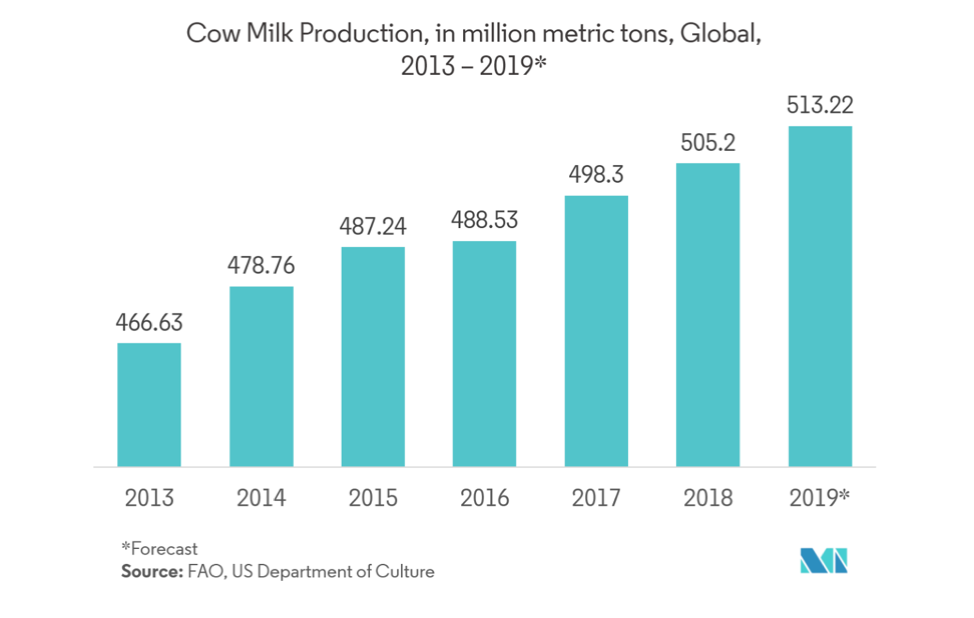
Global Milk Production Trends Source USDA
In North America however, even while there’s extreme price pressure on milk, there is increased demand for certain types of dairy products as opposed to fluid milk, in part because there’s increased interest in protein and probiotics as key parts of a healthy diet.
This means that milk products such as whey (for protein powders) and yogurts and cheeses are seeing increased demand even as the consumption of fluid milk softens in favor of milk analog products such as soy milk.
So while dairy companies must keep production costs in check, they’ll want to take advantage of the increased consumer interest in cheeses and yogurts.
While some dairy farms are introducing advanced manufacturing concepts such as Robotics, Lean Manufacturing and Industry 4.0, farms themselves are still largely a manual labor intensive business. However, once raw milk is delivered to a dairy processing facility, all of the primary processes of turning raw milk into value added products are machinery intensive.
This means that dairy processing facilities are ripe for disruption using Industry 4.0 technologies and in particular Smart Factory Analytics that monitor machinery activities directly to improve process efficiency.
According to a recent report on Dairy Industry Packaging Trends:
- Over the past few years, the consumption of dairy products in the United States has increased, especially cheese, parmesan, provolone, and mozzarella, which is likely to boost the dairy packaging market in the country.
- The rapidly changing consumer preferences towards packaged food and changing economic scenario are significantly affecting the US dairy packaging market. Considerable expansion of dairy product portfolio, primarily into sports nutrition, along with an increasing number of casual users is expected to drive the market further.
Dairy products such as yogurt and cheese are often packaged in thermoformed plastic packaging, and in fact “the most popular material in current use for fresh yogurt is thermoformed TiO2 (Titanium DiOxide) pigmented high impact polystyrene (PS-HI), with either an aluminum foil/plastic laminate or a paper/plastic laminate heat-seal lid or closure.”
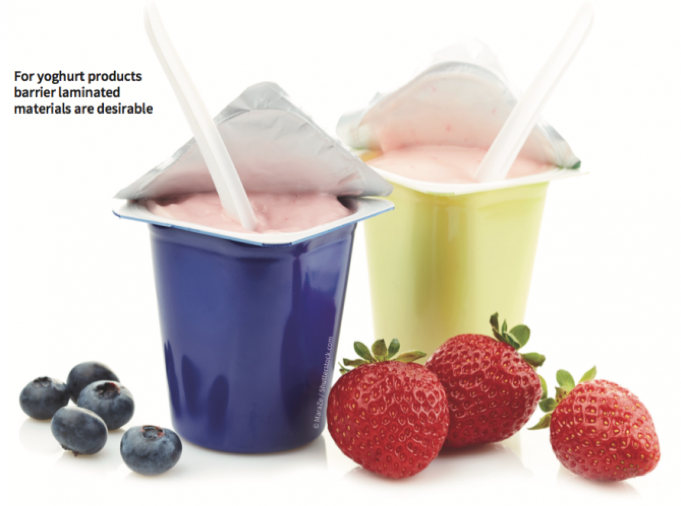
Thermoformed Yogurt Packaging - Courtesy New Food Magazine
According to one study, Curbing variations in packaging process through Six Sigma way in a large-scale food-processing facility, “the cost of packaging ranges anywhere from 10 to 64 % of production costs” of consumer dairy products. This is a useful example for those looking to implement a Lean Six Sigma program at their dairy processing facility.
Therefore it’s vital for dairy products manufacturers to be able to deliver thermoformed packaged goods efficiently.
Thermoforming lines are very complex, often with a wide range of support systems that enable the process. Whether the line is sheet fed, fed from rolls or continuously fed from extruders, all thermoforming lines will have a molding function which forms the packaging container. The mold may use a male and female component to press packages into shape or they may use vacuum or pressure to mold packaging components. This means that a given thermoforming line may have air service lines, vacuum service lines and cooling lines in addition to the ability to heat the thermoformed sheet to a very specific temperature.
With all of this complexity, it’s relatively easy for thermoforming lines to have excessive downtimes, particularly when they are subject to micro-stops which can be difficult to track and measure.
Worximity has developed a range of resources for thermoforming line operators and managers to help to understand and minimize the productivity losses that can occur with the thermoforming process and ways to optimize thermoforming productivity.
You can learn ways to improve your dairy thermoformed package processes here:
Improving Throughput in Food Packaging Processes
How Worximity Improves Thermoforming Efficiency in Food Packaging Process
Why You Should Consider Monitoring OEE On Multivac: Thermoforming Packaging Machines
The Future of Food & Beverage Packaging for CIOs
OEE & Thermoforming: Using Real-Time Dashboard is Key
Why You Should Consider Monitoring OEE On Multivac: Thermoforming Packaging Machines
OEE Increase of 34% in a Plastics (Thermoforming) Plant
Improving Throughput in Food Packaging Processes
The Worximity Factory Analytics solution includes TileConnect smart sensors that are easily installed across your dairy thermoforming packaging machinery. One cheese manufacturer, Amalgamated Dairies Limited (ADL), installed sensors on the output side of their packaging equipment. The small form factor of the smart sensors enabled them to easily find suitable installation locations. Using high-accuracy optical sensors they were able gather packaged food production rate data in realtime.
ADL produces a wide range of cheeses from wholesale and retail Feta as well as speciality cheeses such as Cheddar and Havarti and grated cheeses. Within a few months of real-time monitoring, ADL had increased its production capacity by over 14%.
Additionally, they are finding additional savings such as significantly reducing overtime.
To learn more about this dairy packaging optimization case study, download it here!