Many factors can lead to Overprocessing Waste. Sometimes, products that are excessively processed are highly complex and expensive and it can be difficult to clearly identify overprocessing. At other times, a comparison of detailed customer specifications or the elimination of rework can eliminate overprocessing.
By using Lean Manufacturing, products are designed and fabricated using equipment and design methods that help to ensure products that exactly meet end customer requirements.
Causes of Overprocessing Waste include:
- Poorly communicated customer specifications that leave doubt as to exact requirements
- Rework to meet product specifications or quality requirements
- Poorly planned work processes that cause extra steps along the way
- Including more components or material than necessary for the product to meet specifications
- Delivering higher precision dimensional components than necessary
- Using materials with properties that unnecessarily exceed specifications such as strength, hardness, purity etc.
A simple example of overprocessing waste is when a part of a product is highly polished using labor and machinery when it’s not a customer or product functionality requirement. Excess Processing also can include running more analysis than is required to meet specifications, having to adjust components after installation or over engineering products.
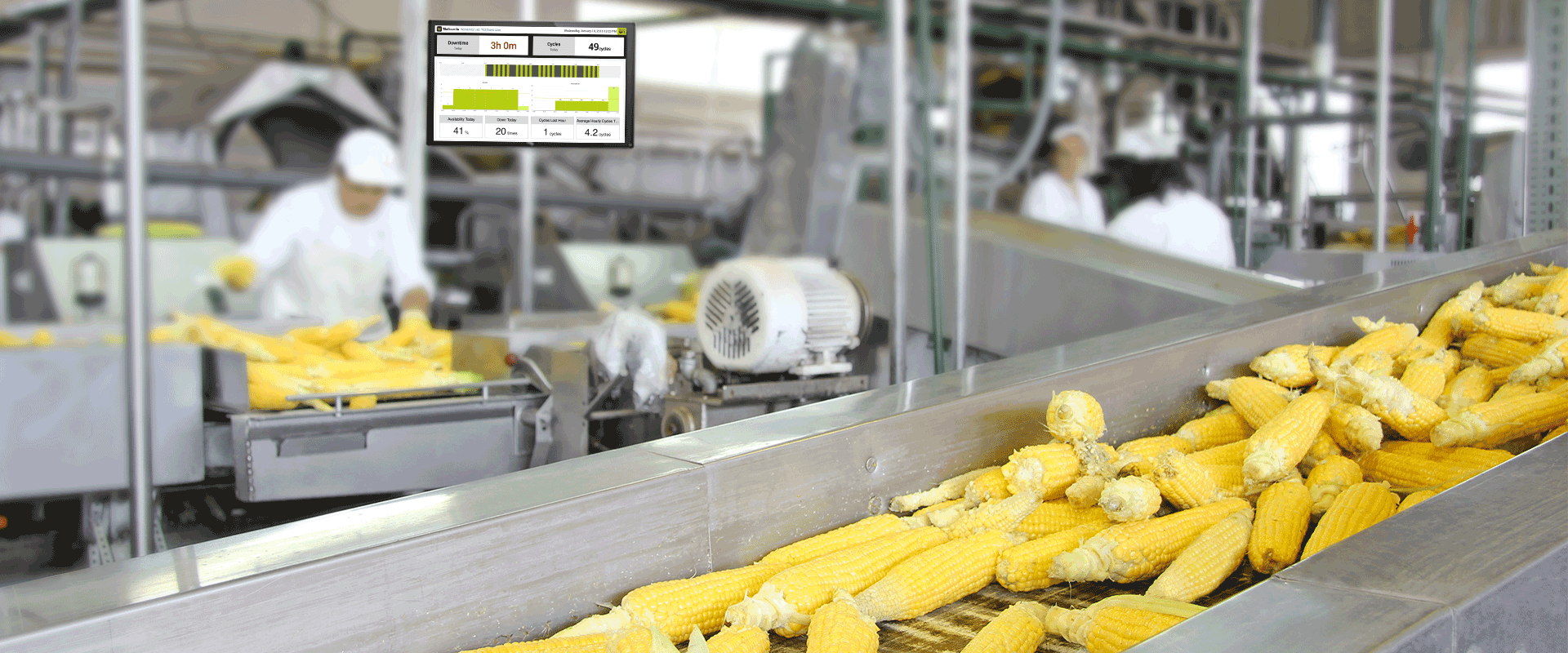
As with other types of waste, Overprocessing Waste can occur in the office as well as manufacturing areas. Producing more detailed reports than necessary in order for one report to satisfy many users is one from of office overprocessing waste. Using Smart Factory Analytics with customized dashboards for each role can be one way to reduce excess processing waste.
Lean Consultants will often coach an organization to ‘put themselves in their customer’s shoes’, in other words, to see specifications and products through their customer’s eyes. By looking at a final product for a customer in this way and mapping your own product vision more closely to theirs, you can gain insights into where excess processing may be occurring. You are then able to work backwards through the entire process to root out overprocessing wherever it occurs.
Lean Consultants will also coach businesses to ‘Learn to See Waste’ and in fact undertaking Lean Manufacturing is sometimes also called ‘learning to see’.
Having reviewed our 8 Part Series on Waste in Lean Manufacturing you can now run an eight waste ‘learn to see’ audit on your own and likely produce significant value for your business. Of course, having data from your production process can help you to not only to uncover hidden waste but also to quantify obvious waste so that you can both assess costs of improvement and measure the results of progress.
Once Smart Factory Analytics are in place, you can teach employees the types of waste (DOWNTIME) and team them in pairs with clipboards to begin to observe and document where they see waste occurring. Smart Factory Analytics can be a critical technological and cultural catalyst to help people to become empowered members of your Lean Manufacturing team.
The eight wastes of lean manufacturing can be remembered with the acronym DOWNTIME:
Read More: Types of Waste in Lean Manufacturing - Part 1 - Defects Waste
Download our Free Lean Manufacturing Industry 4.0. to understand how technology can help you reduce your waste.