There is no question that the meat processing market is becoming far more complex and that there are increasing pressures on meat packers and processors to adopt a wide range of new technologies in order to compete.
A tour of a recent leading international trade show for the meat processing industry shows that a host of solutions and technologies are coming to help meat processors and packers to respond to these market and competitive pressures. A range of demonstrations displayed clearly both the market shifts in play for meat processors and some of the solutions coming to market to provide technical answers to these pressures.
Meat Processing Market Forces
With the advent of pre-packaged meal solutions like Hello Fresh or Blue Apron providing unprecedented meal preparation organization and convenience for consumers, grocery stores are quickly learning how to adapt and compete by selling similarly packaged products and solutions.
One demonstration that we found interesting at the show mentioned above involved the capability to deliver ‘single set-weight’ meat portions. It’s clear that there is consumer demand for ‘retail-ready’ meat products and portions. Many consumers no longer have the time to wait for a butcher to select, cut and wrap individual portions and want to buy a ready-to-prepare product where each portion is precisely equal in order to prepare a set number of plates. They may possibly buy the meat portions for use with a meal preparation product that only needs meat as the additional ingredient, or they may be simply looking for the speed and convenience of nearly identical single-serve portions.
The precision and accuracy of these systems to slice, batch and pack automatically is quite remarkable. One system can repeatedly cut and individually package a 100g steak within +/- 4g. This requires a meat processing and packaging system to analyze the next cut for the estimated yield (weight), accounting for the meat density and any abnormalities in the particular cut.
Advanced Meat Processing Technologies
Responding to consumer desires, such as ready-to-prepare, precisely cut, single-serve, single-set-weight meat products of course requires a very precise automated piece of equipment like that on display. While a machine like this can deliver this consumer-driven product, it is capital intensive and therefore needs continuous uptime in order to be a profitable investment. Machinery like this can be finicky however and can easily suffer from unplanned downtime, driving OEE lower.
Also on display at the show was a conveyor system for these retail-ready products that can manage what can seem like an infinite number of SKUs. If you can imagine a mathematical array of 4 product attributes; meat product (meat cut), grade (such as 'prime'), precise serving weight and number of servings per package and you feel like your customer needs a broad mix of these attributes to choose from at point of purchase, the SKUs quickly proliferate. In a meat processing environment this also requires traceability of individual products or batches to meet regulatory demands.
The conveyor system shown was magnetically-driven with rapid transfer and merging of products, and being magnetically driven, 90 degree transfers are possible because a motor and chain or belt-drive are eliminated.
The lack of mechanical drive also meant that the system could be stopped by hand with very little force, leading the author to imagine the frequent undiagnosed micro-stops that are possible and the significant lack of production being the result as seconds or minutes of micro-stoppage accumulate to hours or days of unplanned downtime over an extended period time.
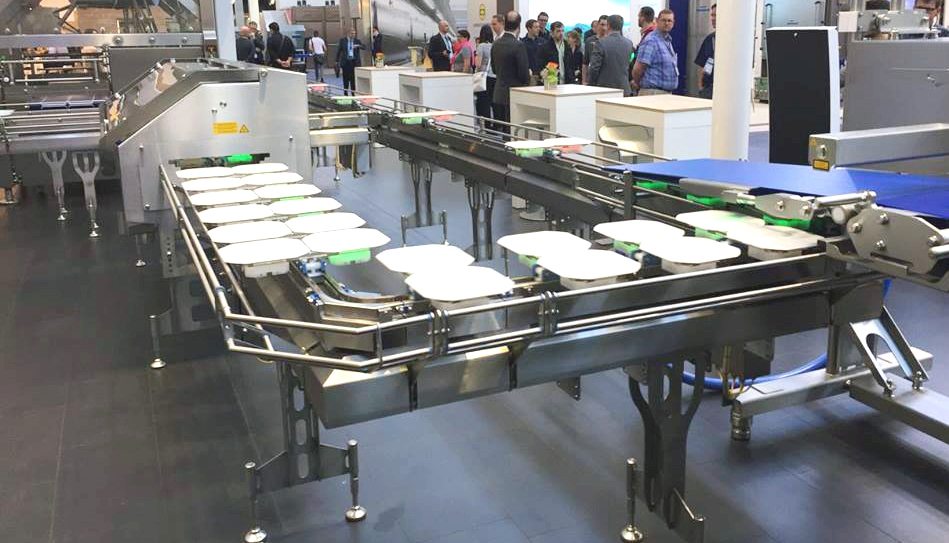
Example of Magnetically Driven Meat Packaging Conveyor on Display
In addition to the portion control and conveyance systems mentioned above, there are new ranges of meat processing robotics systems which were on display including for slaughter applications, historically a manually intensive operation.
The system below uses two robots that work in synchronization to perform all the movements necessary for pig slaughter lines. Each carcass is digitized by measuring the surface profile and a 3D model is created so that each carcass is individually processed to maximize yield.
Meat Processing and Packaging is Becoming Increasingly Complex and Capital Intensive
The level of complexity, automation and capital intensiveness of the meat processing industry is clearly rapidly increasing, particularly in the packaging processes. At the same time, there’s significant room for improvement managing the existing equipment that’s in most meat packing operations.
As a result, monitoring OEE for Meat Processors and Packers is becoming increasingly vital to compete.
From the recent report Uptime, from MultiVac:
“Corey Arrick, currently manager of technical operations, Overhill Farms, believes many plants have room for improvement in tracking downtime events and recording how downtime events are resolved. ‘When you start collecting that data and combine it with a review process you are easily able to target the top three to five issues. Packaging machines are subject to influences from upstream and downstream units, the product being packaged, materials, personnel, environmental conditions and the equipment itself, so it’s important to understand the root cause of equipment downtime.”
“‘Our biggest cost is labor’” says Patrick Williams, secretary/general manager of Premier Foods, which specializes in portion-sized chicken breasts and tenders, marinated breasts, specialty cuts and private labels. “When equipment goes down we have 90 people standing around doing nothing.”
And a recent article in PackWorld regarding OEE notes that “one process engineer from meat / poultry said, ‘downtime is usually associated with maintenance problems. There is a need for process machinery with more preventive and predictive schedules and self-diagnosis'.”
This point begins to support the connection between monitoring OEE and getting predictive maintenance insights.
In a recent survey of food manufacturers, the State of Food Manufacturing, the question was asked, ‘what keeps you up at night?’.
“The big issue is throughput, and several factors contribute to it such as OEE; automation or a lack of it...” with 71% of respondents, nearly three quarters of respondents citing this as their number one concern.
And from Packaging Strategies Magazine:
“As packaging lines have become more efficient, waste or problems on the line can become less visible and harder to identify. For example, lines might be slow due to multiple micro-stops, or overall line performance might falter due to lack of standard work or process for operators. We can miss what we don’t see.
But there are solutions available that allow line managers to better see and correct problems. Overall Equipment Effectiveness (OEE), a Lean manufacturing principle that measures the productivity of a line, shift or piece of equipment over a given timeframe, is one such solution.”
What’s the answer for meat packers and processors looking to compete with all of these competitive pressures and technological advances.
Start with the Packaging Process and Focus on OEE.
In a must-read study for meat processors and packers, a producer and distributor of cooked meat products had a goal “to shorten the time between production and packaging to ensure its packaged meat products were fresh and well before their expiration date when delivered and sold to customers across the country.”
In the study, Use of packing equipment efficiency as an estimate of the overall plant effectiveness and as a tool to improve financial results of a food-processing unit, the researchers established that:
“the use of data collected from the packing line to mimic the whole unit’s efficiency suggests a heuristic method based on the geometric properties of OEE to define what parameters shall be targeted to plot an improvement plan.”
Whew! That’s a lot of jargon.
The essence of what they’re saying however, is that the packaging line, being the choke point for most meat processors and packagers, is an ideal place to start to measure OEE.
Why? Because it’s like saying that the packaging line is the ‘heart’ of the process and putting a heart monitor there will help you to establish the health of the overarching process.
Additionally, through mathematics and correlation, you can begin by measuring packaging line OEE, and extrapolate what you see to what is causing lower than desired OEE at the packaging line to what is happening both upstream and downstream.
Part of what makes this resource so powerful is that:
“in addition, it is shown how OEE correlates with earnings, allowing for the calculation of the impact of continuous process improvement to business results.
The analysis of data collected in a commercial food processing unit made possible: (i) the identification of the major causes of efficiency loss by assessing the performance of packing equipment; (ii) the definition of an improvement strategy to elevate OEE from 53.9% to 74.1% and; (iii) the estimate that by implementing such strategy an increase of 88% on net income is attained.”
%2520OEE%2520to%2520Operational%2520Profitability.png)
Relating the Improvement of Meat Packaging Line (and Plant) OEE to Operational Profitability
Wow.
Their methodology and mathematics can seem quite complex, but the essence is:
“Losses accounted for upstream will eventually result in losses downstream. These disturbances will be noticed and recorded while calculating the OEE of the nth equipment.
In a typical food processing plant the last equipment in the factory that has a fixed position and where a data collecting station can be placed is the packing line. Afterwards the finished product is moved to the storage facility to wait for shipping to customers.
Therefore it is recommended to calculate the overall plant effectiveness of a food processing plant by measuring the OEE of the packing line” (emphasis added).
They did state that for this study:
“Measuring the OEE was another challenge. Since all data was collected manually, it took a full day of data entry work to calculate the OEE, an expensive, time consuming and ineffective process.”
So naturally in a meat processing or packing production setting, using Smart Factory Analytics technology to measure OEE can radically compress response time to downtime but can also drive faster and more accurate insights to maximize OEE optimization efforts.
According to Food Quality and Safety magazine:
“The biggest issue facing the food industry with respect to machines is that the vast majority of machines are not connected and, therefore, provide very little information to the corporate network for analysis.”
Worximity has a proven solution for improving meat process OEE and particularly deep experience measuring and improving meat packaging line OEE, which with a bit of math, can be a proxy for operation-wide OEE measurement.
For meat processors and packers to compete today, solutions like Worximity are vital to success.
Take advantage of the Worximity teams’ knowledge in packaging processes optimization in the meat industry and start to gain your competitive advantage by booking a demo with a solutions consultant today.