Lean Manufacturing Examples from Top Industry Leaders
Implementing Lean Manufacturing can seem daunting. Looking to what the best have accomplished as examples and inspiration can be motivating!
Introduction to Lean Manufacturing
Lean Manufacturing represents a paradigm shift in how businesses approach production processes, emphasizing efficiency, waste reduction, and continuous improvement. Originating from the Toyota Production System, Lean principles have since permeated industries worldwide, offering a systematic framework for optimizing operations. At its core, Lean Manufacturing aims to streamline workflows, minimize non-value-added activities, and maximize value delivery to customers. By fostering a culture of relentless improvement and empowering employees at all levels, Lean transcends mere cost-cutting measures to cultivate sustainable growth and competitiveness. This introduction sets the stage for exploring the fundamental concepts and methodologies underpinning Lean Manufacturing, offering insights into its transformative potential for organizations striving for operational excellence in today's dynamic business landscape.
For many companies, switching to a continuous improvement and lean manufacturing culture is daunting. The numbers have shown that incredible gains can be gleaned by implementing lean and continuous improvement tools. Still, the aversion to the risk associated with major company change can be intimidating.
But if there’s one great selling point for any process or product, it’s showing how it has helped someone else, and both the service and manufacturing industries are full of lean success stories.
Key Principles of Lean Manufacturing
Elimination of Waste
At the heart of Lean Manufacturing lies the principle of eliminating waste, known as "muda" in Japanese. Waste can manifest in various forms, including overproduction, excess inventory, unnecessary motion, defects, waiting time, and underutilized talent. Lean methodologies meticulously identify and eradicate these sources of waste to optimize processes and resources. By streamlining workflows and focusing only on activities that add value to the end product or service, organizations can enhance efficiency, reduce costs, and improve overall productivity. <H3> Continuous Improvement: Central to Lean Manufacturing philosophy is the concept of continuous improvement, or "kaizen." Rather than viewing improvement as a one-time endeavor, Lean encourages a culture of ongoing refinement and innovation. This iterative approach empowers employees at all levels to identify opportunities for enhancement, experiment with new ideas, and implement incremental changes to processes. Through continuous improvement initiatives, organizations can adapt to evolving market demands, enhance product quality, and drive sustainable growth over time.
Just-In-Time Production
Just-In-Time (JIT) production is a cornerstone of Lean Manufacturing, aiming to synchronize production with customer demand while minimizing inventory levels. By producing goods or delivering services precisely when needed, organizations can reduce inventory carrying costs, alleviate storage space requirements, and mitigate the risk of obsolescence. JIT principles also facilitate smoother production flows, shorter lead times, and improved responsiveness to market fluctuations. However, successful implementation of JIT relies on robust supply chain management, reliable suppliers, and efficient production processes.
Flexibility and Adaptability
In today's dynamic business environment, adaptability and flexibility are paramount for success. Lean Manufacturing emphasizes the importance of agile operations that can swiftly respond to changes in customer preferences, market conditions, and technological advancements. By fostering a culture of flexibility and adaptability, organizations can quickly reconfigure production processes, reallocate resources, and pivot strategies to capitalize on emerging opportunities or mitigate risks. This agility not only enhances competitiveness but also fosters resilience in the face of uncertainty.
By embracing these key principles of Lean Manufacturing, organizations can unlock new levels of operational efficiency, quality, and customer satisfaction, positioning themselves for sustained success in a rapidly evolving marketplace.
Real-World Lean Manufacturing Success Stories
Toyota
The Toyota Motor Company is one of the greatest examples of lean manufacturing and continuous improvement. Their methods for continuous improvement are so well developed and precise they have their own name, the Toyota Production System (TPS).
With TPS, lean ideas are built into the fabric of the company at all levels and integral to the organization’s value stream. Production line workers are recognized as vital to improving manufacturing processes and are carefully selected. The same is true of every other department, including sales, engineering, service, accounting, human resources, and more. Toyota also pays unprecedented attention to workers in its use of team-building training, and resources spent to teach all employees the importance of collaboration. This results in workers coming forward when they have an idea for improvement, a practice which leads to 2 million suggestions generated per year worldwide, with 95% of the workforce contributing. Most impressive of all, 90% of these suggestions are implemented.
Starbucks
Starbucks, a global coffee giant, faced significant challenges in the late 2000s amidst the fallout of the global financial crisis, which led to the closure of underperforming stores and a decline in product quality and customer satisfaction. Recognizing the need for change to stay competitive in the dynamic coffee industry, Starbucks embarked on a comprehensive change management program that included Kaizen and lean techniques. The company identified key areas for improvement, including streamlining operations, refocusing on core products, and enhancing customer service.
To achieve these goals, Starbucks implemented various strategies, such as closing underperforming stores, improving product quality, launching a customer feedback program, and revamping store designs. However, the change management process was not without its challenges, including resistance from some employees and the risk of losing customers during the transition. Despite these obstacles, Starbucks successfully navigated the change process, resulting in improved financial performance, enhanced product quality, and increased customer satisfaction and loyalty.
Factors contributing to Starbucks' success included strong leadership, effective communication, employee engagement, customer focus, and flexibility. By prioritizing these elements, Starbucks created a culture of continuous improvement, ultimately driving sustained growth and success. The Starbucks change management experience serves as an insightful case study for businesses looking to implement change successfully and improve their value stream in today's dynamic market environment.
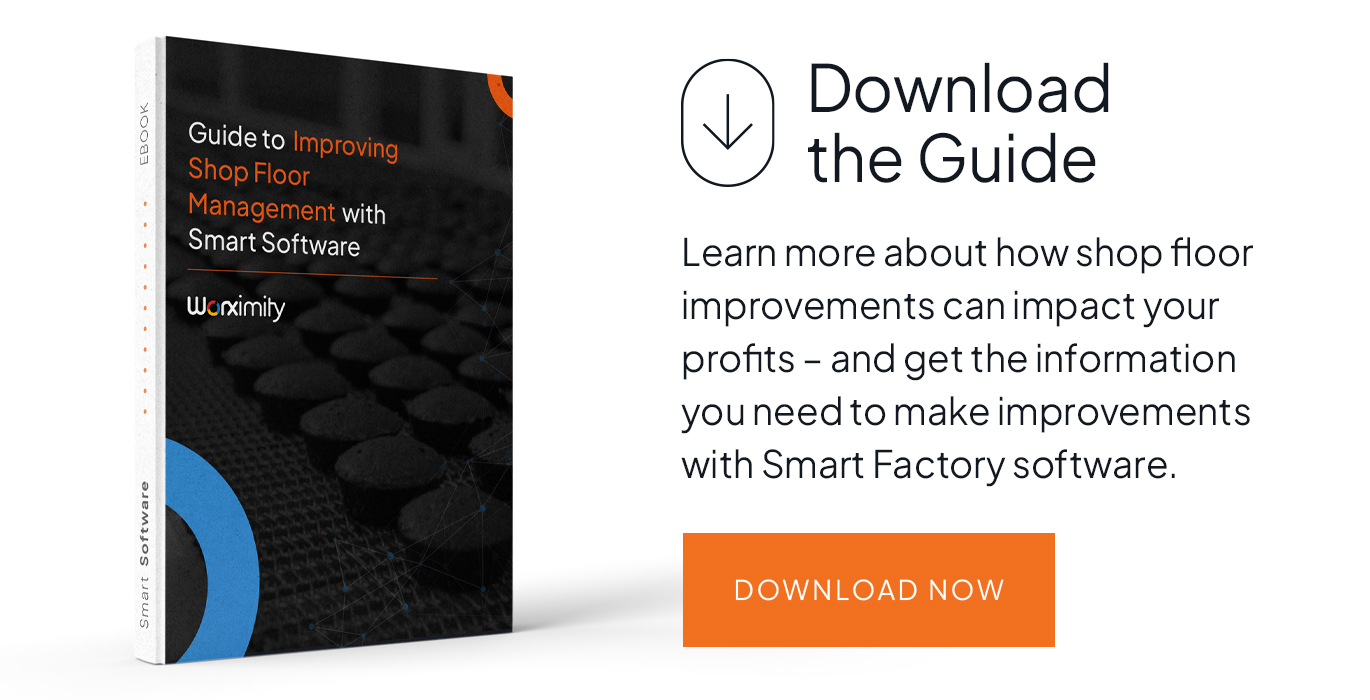
Motorola
Motorola's utilization of Lean Manufacturing principles stemmed from a pivotal moment in the early 2000s when the company faced a critical juncture marked by declining product quality and dwindling customer satisfaction. In a bid to reclaim their competitive stance in the market, Motorola turned to Six Sigma, a data-driven methodology renowned for its efficacy in process enhancement.
With semiconductors being a cornerstone component in many of Motorola's products, rectifying quality issues in semiconductor production became imperative. Through the implementation of Six Sigma's Define, Measure, Analyze, Improve, and Control (DMAIC) method, Motorola underwent a transformative journey. The methodology enabled them to pinpoint the root causes of defects plaguing their semiconductor production process, leading to a series of strategic changes that bolstered production quality and customer satisfaction. By fostering a culture of continuous improvement and employee engagement, Motorola not only addressed immediate challenges but also laid the groundwork for sustained operational excellence.
The outcomes were striking – a reduction in defects, enhanced customer satisfaction, and increased profitability. Motorola's success story with Lean Manufacturing principles serves as a beacon for organizations navigating similar quality dilemmas, showcasing the transformative potential of data-driven methodologies in optimizing business processes and fostering enduring success.
Implementing Lean in Your Operations
Implementing Lean in Your Operations presents both challenges and opportunities for organizations seeking to enhance efficiency, reduce waste, and improve overall performance. By embarking on a Lean journey, businesses can transform their operations, streamline processes, and drive sustainable growth. However, success in Lean implementation requires careful planning, dedication, and a commitment to continuous improvement.
Starting Your Lean Journey
The first step in implementing Lean in your operations is to foster a culture of Lean thinking throughout the organization. This involves educating employees about Lean principles, creating awareness of the benefits of Lean, and garnering buy-in from all levels of the organization. Establishing a cross-functional Lean team can help drive initiatives forward and ensure alignment with strategic objectives. Additionally, organizations should prioritize identifying and prioritizing areas for improvement, setting clear goals, and developing action plans to initiate change.
Overcoming Challenges in Lean Implementation
While Lean offers numerous benefits, its implementation can present challenges that organizations must navigate effectively. Resistance to change, lack of leadership support, and inadequate resources are common obstacles that may hinder progress. To overcome these challenges, organizations should invest in employee training and development, foster open communication, and provide adequate support and resources for Lean initiatives. Additionally, organizations should embrace a mindset of experimentation and learning, recognizing that setbacks are opportunities for growth and refinement.
Measuring Success in Lean Manufacturing
Measuring success in Lean Manufacturing requires defining clear metrics and key performance indicators (KPIs) to track progress and evaluate the effectiveness of Lean initiatives. These metrics may include measures of productivity, quality, lead time, inventory levels, and customer satisfaction. By regularly monitoring and analyzing these metrics, organizations can identify areas for improvement, celebrate successes, and make data-driven decisions to optimize performance. Additionally, organizations should solicit feedback from employees and stakeholders to gauge the impact of Lean initiatives and identify opportunities for further refinement.
Worximity is deeply committed to the philosophies of Continuous Improvement and Lean Manufacturing in food manufacturing. Using our IoT technology we provide company-wide visibility into the statistics that matter to manufacturers and accelerate TTV (Time to Value) of investments in company culture and training to achieve outstanding productivity.
Download our Free Lean Manufacturing and Industry 4.0. to better understand where to start!