The Food and Bev industry use Vertical-Form-Fill-Seal processes to output high value retail or bulk packaging products, especially in the fresh & frozen meat, fruit and vegetable, dairy, snack, pet food, various beverage and pharmaceutical industries.
While vertical form fill seal machines are never used alone, they are often near the end of high value packaging solutions and need to be carefully upkept and monitored, since they can easily become a continuous production bottleneck. It is essential to minimize Downtime, Change Over delays and maintain Uptime, by keeping a steady CPM (Cycles Per Minute).
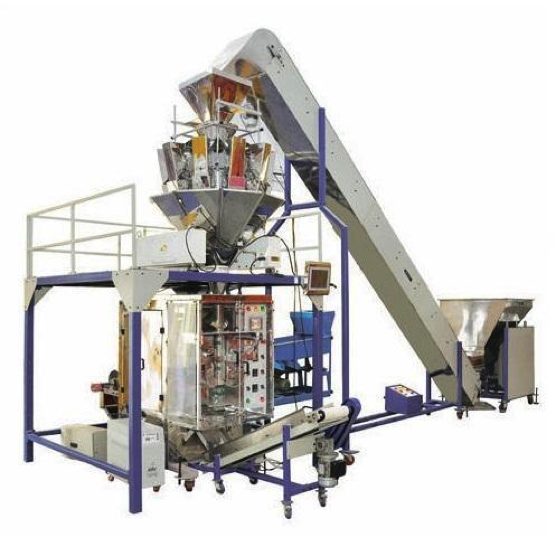
Where can I connect to monitor my equipment?
Vertical form fill seal machines or VFFS baggers can be configured for a variety of packaging missions, however, they all have the same operating principle:
① Form-Fill-Seal → ② Print Bag ID → ③ Cut (& Release) → ④ (Film Advance).
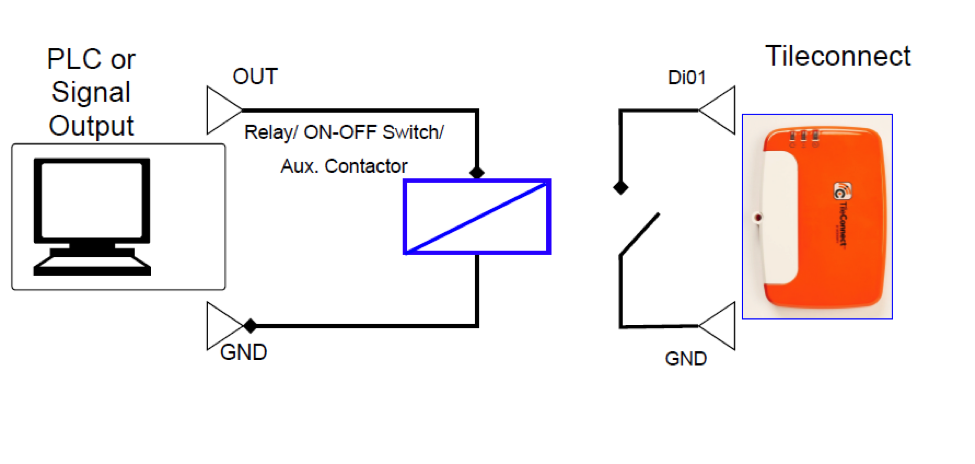
At each step of the process, it is possible to acquire a binary equipment output. From the PLC, the relay board or from a parallel relay connection, a dry contact loop can be setup, reflecting the operating ON/OFF status.
For recent vertical form fill seal machines, a PLC controls the equipment through a digital relay board, allowing a binary status output. The HMi allows for an easy setup on which binary channel to output, making it easy to chose.
The common, and accessible, data monitoring points on a VFFS Bagger are:
- Printer/ Inkjet relay trigger
- Knife relay trigger
- Film advance trigger
An accurate and accessible output should always reflect real time equipment production status.
How can I accurately monitor Downtime, determine Change Over delays and track Bagger CPM?
Data loggers, such as Worximity’s Tileconnect Smart Sensor was designed to acquire binary machine status, through its digital port. By connecting a dry contact loop to the knife relay trigger or the (film advance relay), the Tileconnect will be counting the number of machine cycles per minute (CPM).
Downtime KPi’s can be calculated by tracking the measurements sent over a wireless network, by devices such as the Tileconnect. In real time monitoring platforms, such as Tileboard, it is also possible to associate measured Downtimes and record them as specific causes, such as Film Roll Change Over, Printer Out of Ink or Film Advance Servomotor Damage. This adds value to measured data since it provides a status report as well as becoming a tool for root-cause analysis.
Uptime KPi’s can also be derived from real time measurements. Devices, such as Tileconnect, continuously feed data through wireless networks, reflecting machine status. This Allows users to login into platforms, such as Tileboard, to monitor equipment CPM, Quantity produced and other production related parameters. Tileboard also allows the quick setup of Alerts on specific KPi’s, automating warning signs, should CPM drop below threshold rates.
How can I add value to my collected data?
The best way to add more value to collected data is to use platforms, such as Tileboard, that allow flexible manipulation of information. In addition to Downtime and Uptime KPi’s, as well as (Root Cause Analysis) tools, Tileboard also allows measurements to be associated with specific product codes, or SKU’s. The provided analysis Production Report feature and a simple data export function, containing all available Downtime and Uptime KPi information, allow the in-depth analysis of Equipment performance, for each product code and each work shift. Connect your vertical form fill seal machines today!
Discover how ADL overall productivity increased by 14%. Read the full case study: