Within modern manufacturing, no one knows better than you that money is made and lost on the shop floor. Understanding the key differences between various solutions on the market and the value they provide is important in determining which ones can meet your specific needs and help you minimize losses. Not every manufacturer, for example, needs an ERP or MES. Machine Monitoring and OEE (Overall Equipment Effectiveness) are effective at boosting overall efficiency, but what is the difference between them and what is best for your operations?
Machine Monitoring
Machine Monitoring was developed at the University of Cambridge in 1991 when engineers connected a live feed of a coffee pot to their network. Why did the engineers need a live feed of their coffee? It was a 10-minute walk from their office to the coffee pot and they were often left with unexpected downtime and frustration when the pot was not ready when they arrived. This was the humble beginning of Machine Monitoring.
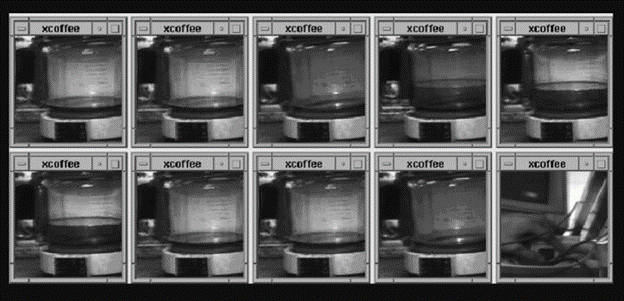
Fun Fact: This was also the first use of a webcam!
Machine Monitoring is a process of collecting and analyzing data from industrial machines, providing you with real-time visibility into your manufacturing operations - visibility that helps empower your shop floor. Collecting machine data can provide valuable insights on:
- Machine status
- Utilization
- Downtime
- Cycle time
- Production performance
- Product quality
Manufacturers that are proactive and leverage these insights will have an edge in their market. For example, machine monitoring can help detect potential equipment failure, flagging maintenance to fix the issue before downtime occurs. Using machine monitoring lets you gather important information about your manufacturing operations and uncover insights that support your continuous improvement efforts.
OEE Monitoring
OEE Stands for “Overall Equipment Effectiveness” and was introduced in Tokyo in the early 1980s. As a plant becomes more mature and regular activities ensue like shift changes and maintenance, there is a high probability that production losses will occur. OEE is a KPI that is calculated from the data acquired through machine monitoring.
To help monitor and find actionable solutions to better increase OEE, let’s look at what goes into calculating Overall Equipment Effectiveness.
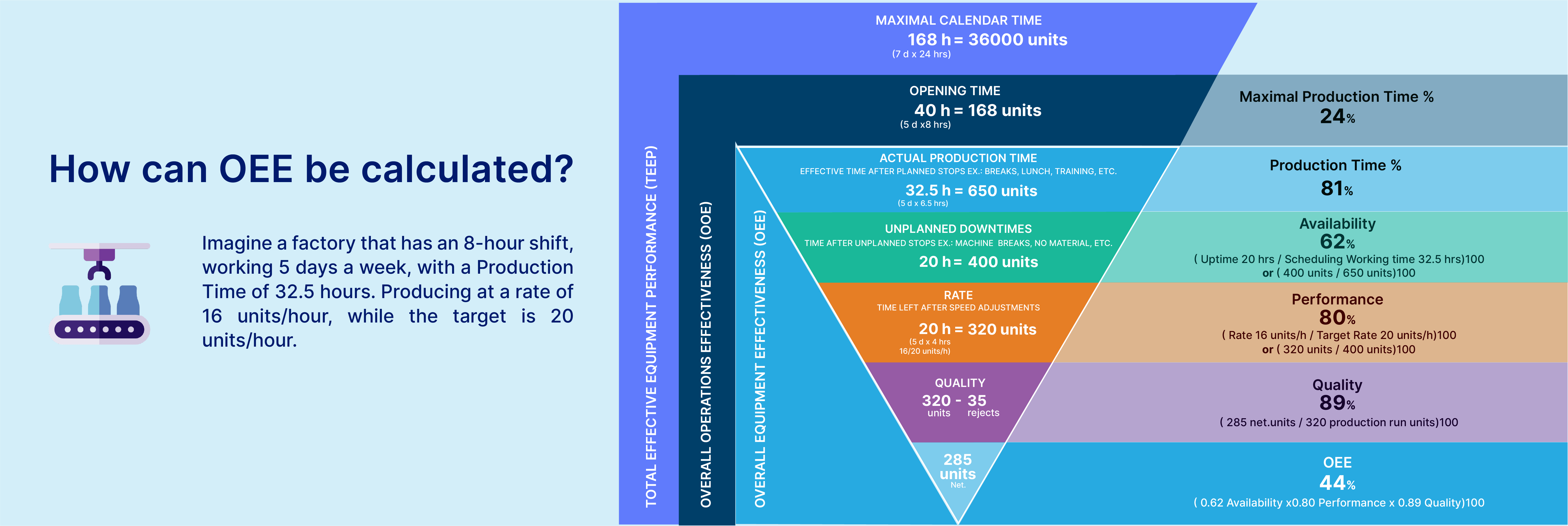
Availability:
The ratio of the actual time machines are running (Run Time) to the planned time for production (Planned Production Time).
Performance:
Evaluate performance loss, which covers any factors slowing down the manufacturing process or the rate at which you are producing whether measured in days, shifts, hours or even minutes. This includes slow cycles and small stops. Instances like machine wear, substandard materials, misfeeds, and jams.
Quality:
Monitoring parts that don't meet standards due to factors like giveaway, scrap, and rework.
Interpreting OEE:
Overall Equipment Efficiency is a performance indicator for machinery. A higher percentage signifies optimal efficiency with minimized downtime, while a lower figure suggests potential areas for improvement in equipment availability, performance, or quality. Essentially, it serves as a quick gauge for assessing the overall effectiveness of production processes.
Worximity’s Dashboard
Worximity's cutting-edge production monitoring solution employs strategic IoT sensors and PLC integration, translating terabytes of data into accessible metrics on a user-friendly dashboard. Featuring key KPIs like OEE (Overall Equipment Effectiveness), Downtime, and Giveaway. Beyond data acquisition, the dashboard’s ability to showcase important real-time KPIs listed above to lower-level employees empowers them to efficiently manage production rates without overwhelming upper management fostering a sense of responsibility into the hands of your key employees.

Conclusion:
In summary, while Machine Monitoring excels in immediate, granular data creation and analysis and can predict and prevent machine failures, OEE Monitoring provides strategic insights into manufacturers' key areas like Quality, Performance, and Availability. OEE is necessary for achieving short and long-term efficiency gains. The synergy of these tools empowers manufacturers to navigate the complexities of modern manufacturing, ensuring both immediate improvements and sustained growth in the era of Industry 4.0.