A driving force behind lean manufacturing is waste elimination. When waste is eradicated—or at least greatly reduced—from your manufacturing processes, what follows should be increased profitability for your company.
As we’ll see, there are many opportunities for reducing lean manufacturing waste. The advent of Industry 4.0 and the introduction of connectivity through the Industrial Internet of Things (IIoT) for continuous improvement increases the potential for waste reduction opportunities.
We’ll be discussing some of those opportunities in this eight-part series outlining the types of waste that must be addressed in lean manufacturing.
Undoubtedly, we all want to be more “green” as stewards of the environment. And becoming a lean manufacturing operation certainly contributes to that on many levels.
But let’s be honest. In striving for a lean manufacturing operation, the other green we’re also concerned with is making a profit. Without a profit, the business perishes. Not only that, but we are responsible to our employees, stockholders, stakeholders, customers, and end users to ensure we produce a quality product at a fair price.
And we need to do that with the utmost responsibility.
The 8 Types of Lean Manufacturing Waste
While some experts only consider seven types of lean manufacturing waste, a growing majority recognize eight. These types of waste (known as “muda” in Japanese) are:
- Transport
- Inventory
- Motion
- Waiting
- Overproduction
- Overprocessing
- Defects
- Unused talent (not recognized in the first iteration but introduced in the 1990s)
The first seven lean manufacturing wastes are directly related to the manufacturing process, while unused talent belongs to the realm of manufacturing management.
We’re diving deep into each of the lean manufacturing wastes, starting with waste caused by defects.
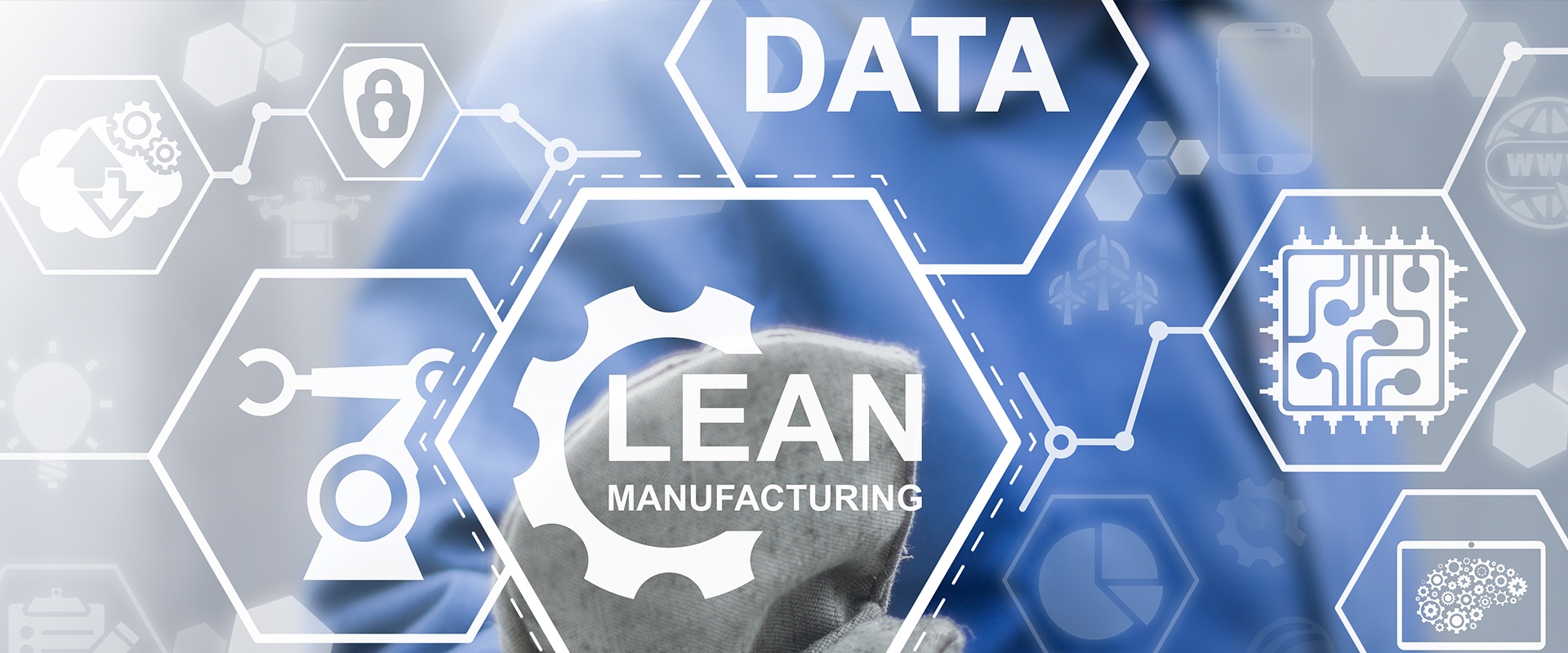
Lean Manufacturing Waste No. 1: Defects
In a perfect world, our parts, components, and products are made perfectly the first time every time. There’s no need for rework, rerun, or disposal.
This is not a perfect world. Defects happen.
A defect can be defined as any instance wherein a product does not meet design or manufacturing specifications. While the possibility of exact, carbon-copy reproduction is nil in the vast majority of cases, parts and products can be manufactured or produced within acceptable parameters.
In the machining of metal and composite parts, these parameters are called tolerances and are plus or minus the target within a defined percentage. As long as the part falls within the parameters or tolerances, it’s a good part.
Anything outside those tolerances is a defect and must be dealt with accordingly. It may be as simple as trimming the flash on a plastic part or sanding/grinding an imperfection on a machined block of steel. But, while the part may be salvaged and is still usable by the end user, it still has a defect, and waste still happens, both in time and money.
The more defects there are—even if repairable—the more waste there is in time, money, and materials. While defects cannot be eliminated, the waste can be minimized by machine and process monitoring, guided by written documentation of what is and isn’t acceptable.
One of the goals of monitoring and documentation is the achievement of a higher overall equipment effectiveness (OEE) score. A score of 80 and above is considered world class. However, most manufacturers fall into the 60 and above classification.
There is always room for improvement, and smart sensors connected to the network, along with data analytics software, help companies achieve a higher OEE. Data analytics software also helps determine which defects are the most crucial to address.
Deciding How to Approach Defects in Lean Manufacturing
It may be difficult—if not impossible—to address all defects found in lean manufacturing processes. Some defects cause major waste, others not so much. That is why applying the Pareto principle helps keep waste to a minimum.
Some data analytics software, in concert with proper documentation and procedures, use the Pareto principle—80 percent of defects are caused by 20 percent of process issues, and 20 percent of defects cause 80 percent of waste—to create charts that offer guidance when determining what needs to be fixed first.
Addressing that 20 percent increases your OEE dramatically. Defects with the highest negative impact are often reduced quickly, and you can then concentrate on other issues that improve the process more incrementally.
Be aware that not all defects are the result of defective machinery or processing. Sometimes there are other issues that lead to defects. Some of them are:
- A lack of process standards or poor documentation of the standards
- Inadequate quality controls
- A lack of a defined process altogether
- A poorly designed product configuration
- Undocumented design changes
These should be considered during your analysis of product defects. But sometimes, particularly in the food industry, there are outside forces over which you have little or no control.
Those defects can often be handled with a plan B to lessen their impact.
Developing a Plan to Minimize the Impact of Defects in Lean Manufacturing
It’s not always possible to rerun or rework a defective product. Sometimes, disposal seems like the only option, and that means you throw cash in the trash.
But there may be alternatives that, while still not as profitable as selling an unblemished product, may lessen the financial blow to your operation.
The poultry industry is a prime example of using a plan B to handle defects. In whole-bird processing, the product is graded using strict guidelines. The grading categories may be:
- Premium grade (free of any defects)
- A-grade (few, if any, noticeable defects)
- B-grade (some defects but sellable to a less discriminating market)
- C-grade (major defects, often handled by repurposing the product for cut-up operations or further processing)
While premium-grade products have the highest profit and lower grades have increasingly less, defects are not necessarily deemed a total loss.
Note that defects in the product aren’t always the fault of the processing. Often, live birds come to the facility in less-than-perfect condition.
You can also find this repurposing of defective products in the manufacture of some hard goods. For example, some defects, such as scratches, small dents, and similar issues, do not affect the operation of the finished product.
Scratch and dent appliance retailers showcase the concept that some defective products can still make a profit for the company, albeit not as much as a premium, defect-free model.
Waste caused by defects in the lean manufacturing product needs to be addressed. While all defects may not be eliminated, you should be able to identify and correct those that will affect your profitability.
At a bare minimum, to mitigate defects, you should develop:
- Documented standards
- Excellent, documented quality controls
- A defined, repeatable process
- A well-designed and tested product configuration
- Documented design changes, should there be any
- The use of IIoT-enabled smart sensors for data collection and data analysis
If you would like more information on how Worximity can help you reduce lean manufacturing waste, talk to one of our experts today.