Understanding Throughput in Manufacturing
Defining Throughput and Its Importance in Industry
Throughput, in a manufacturing context, refers to the rate at which a system produces goods. It is a crucial metric that indicates the efficiency and productivity of a manufacturing process. Higher throughput rates typically imply a more efficient process, which can lead to increased profitability and competitive advantage.
Key Factors Influencing Throughput Rate
Several factors impact the throughput rate, including:
- Machine Efficiency: The performance and reliability of machinery directly affect production speed.
- Labor Efficiency: The skill and productivity of the workforce can enhance or hinder throughput.
- Material Quality: High-quality raw materials reduce the likelihood of defects and rework, thus maintaining a steady production flow.
- Process Optimization: Streamlined processes and effective management of workflow are essential for maintaining high throughput rates.
Calculating Throughput Formula: A Step-by-Step Guide
Components of the Throughput Calculation
The basic throughput formula is:
Throughput=Total Production Time/Total Production Output
To calculate throughput accurately, you need to consider:
- Total Production Output: The total number of units produced in a given period.
- Total Production Time: The total time taken to produce the units, including downtime and delays.
Applying the Throughput Formula in Real-World Scenarios
Consider a factory that produces 10,000 widgets over 8 hours. Using the throughput formula: Throughput=10,000 widgets/8 hours=1,250 widgets per hour
This calculation helps in identifying areas where production can be optimized to enhance throughput.
Three Proven Techniques to Improve Throughput
Enhancing Plant Safety for Better Throughput
Accidents can have a more significant impact on throughput than most processors realize. An accident classified as a “lost time accident” is one that results in the employee being absent from work for at least one full day. By contrast, a “lost time injury” results in an employee’s work being delayed because of stoppage or short-term absenteeism.
The Bureau of Labor Statistics estimates that, in 2019, there were more than 116,000 cases of lost time accidents in manufacturing. Minor accidents, which may go unreported, can still account for minutes or hours of production downtime.
For any processor, the impact of safety incidents is significant. Any incident may result in a line being down for hours or even days and can cause substantial amounts of lost throughput. Production is lost because of the initial incident and may continue to be impacted by damaged equipment, rejected products, and lower team morale. Time and throughput are also lost during the subsequent investigation of the accident itself.
Safety incidents may not be daily occurrences in most plants, but when they occur, the negative impact on production and throughput can be extremely high. Maintaining the highest levels of safety is a proven method for improving throughput rates.
Safety improvements reduce downtime due to accidents and machine failures. Ensuring that safety protocols are followed can lead to a more stable and consistent production environment, thereby increasing throughput.
Identifying and Eliminating Production Bottlenecks
Bottlenecks can be a persistent and frequent reason for reduced throughput. Some bottlenecks are readily apparent: When production at one station outpaces the next, the product will begin to stack up behind the slower operation. This accumulation causes all functions in the production line to slow down to pace themselves to the slowest process, which signals that the slowest process is creating a bottleneck.
In many cases, because operators adjust equipment feeds and speed to ensure the line operates smoothly, the bottleneck may not be readily apparent. Nevertheless, analysis of equipment capacities should reveal the bottleneck, and corrective action can be taken.
Connecting equipment electronically using online data capture technology gives managers the up-to-the-minute throughput information they need to identify and eliminate bottlenecks. Monitoring production processes carefully on a real-time basis can help managers improve throughput rates.
Automating Production Data Collection with Worximity
Production monitoring tools like Worximity streamline data collection, providing real-time insights into performance. By automating this process, manufacturers can quickly identify inefficiencies and areas for improvement, leading to increased throughput. In addition, line operators can monitor their individual performance, check progress against goals, and identify issues as soon as they occur. With real-time feedback from Worximity, operators can correct processing time, address slowdowns, and ensure throughput rates are on target. Providing employees with ongoing performance metrics improves business processes, reduces operating costs and increases team involvement while promoting individual accountability.
Ensuring Throughput Calculation Accuracy with Worximity
How Worximity Simplifies Data Analysis
Worximity’s monitoring and analytics platform collects and analyzes production data in real-time, offering precise and actionable insights. This helps manufacturers accurately calculate throughput and identify areas for optimization without manual data collection errors.
The Role of Real-Time Data in Accurate Throughput Measurement
Real-time data is crucial for accurate throughput measurement as it reflects the current state of production. With real-time monitoring, manufacturers can make immediate adjustments to processes, ensuring optimal performance and accurate throughput rates.
Implementing Worximity for Optimized Throughput Calculation
Getting Started with Worximity for Improved Throughput
Getting started Worximity is quick easy. It revolves around three core steps:
- Connect: Integrate Worximity’s technology on the shop floor and instantly gain real-time visibility.
- Measure: Configure the dashboard to monitor and measure performance metrics such as throughput, speed, downtime and quality in real-time data. Start setting targets based on actual performance.
- Improve: With a clear understanding of your performance, access the inisghts and analytics platform to learn where your biggest opportunities for improvement are.
FAQ
What is the formula for throughput in costing?
In costing, throughput is often calculated as:
Throughput = Sales−Direct Material Costs
What are the components of throughput rate?
The components include total production output, total production time, machine efficiency, and labor productivity.
How does Cycle Time Affect Throughput?
Shorter cycle times generally lead to higher throughput rates, as more units can be produced in the same amount of time.
How can you calculate production capacity?
Production capacity can be calculated as: Production Capacity=Total Machine Hours Available×Efficiency Rate
What factors influence throughput in a manufacturing process?
Factors include machine efficiency, labor productivity, material quality, and overall process optimization.
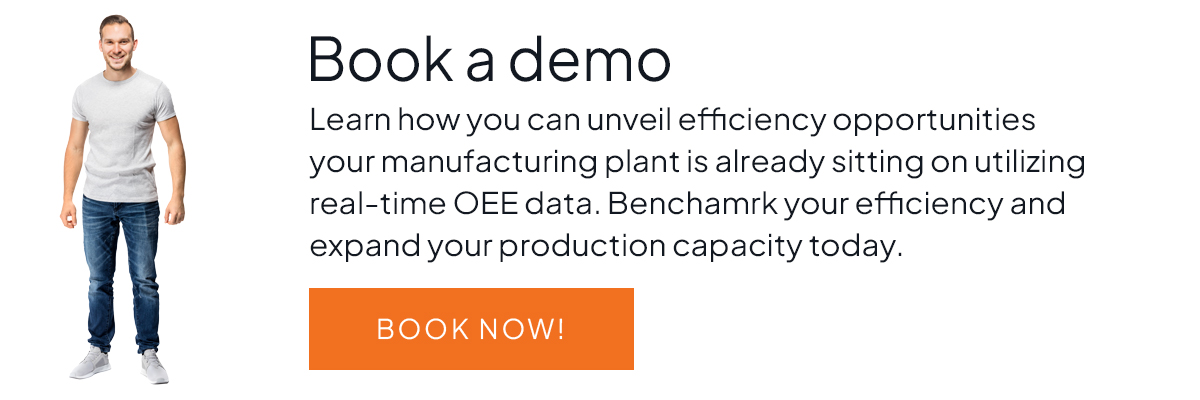